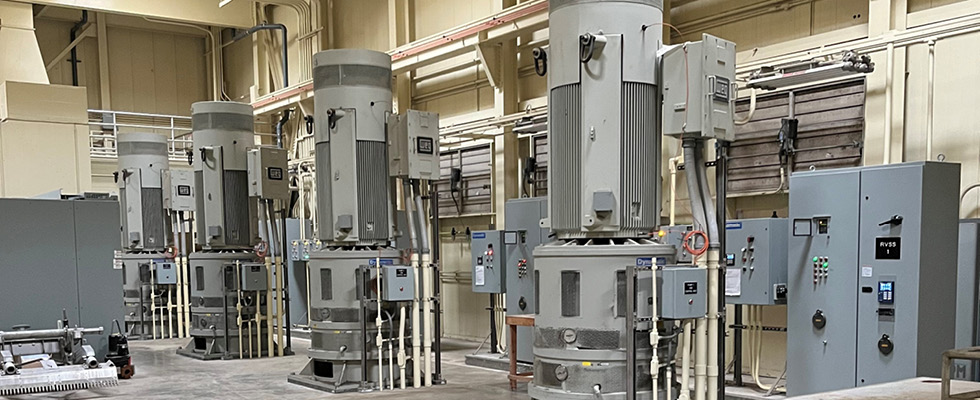
The merits of adjustable speed operation for centrifugal pumps have been recognized for most of a century. By far the most common driver for a centrifugal pump in an industrial or municipal setting is an alternating current (AC) induction motor, favored for its rugged simple construction and long service life. However, these motors have a significant drawback: They operate at only one speed, and the choice of that speed is limited to specific options, dictated by the line frequency (60 hertz [Hz] in North America) and winding configuration of the motor (number of “pole pairs”). Pump designers must choose a speed that most closely achieves the performance they desire (flow rate and pressure) and design the pump to match or approximate the required output.
However, many applications call for the ability to match performance to an unregulated variable demand. These pumps must be designed to achieve the maximum expected demand but operate at conditions often requiring far lower flow or pressure.
Over the decades, a variety of ideas have been devised for controlling the speed of a pump with a motor designed for only one speed. In the 1950s to 1970s, eddy current drives (ECDs) (aka magnetic drives, eddy current clutches) were a widely popular solution for variable speed operation. These devices used the mechanical power of the constant speed motor and transmitted torque to the load at a controlled value, thus controlling the speed of the pump, or regulating it as the load varied.
Beginning in the 1970s, a new technology began to emerge: variable frequency drives (VFDs). Advancements in power electronics technology made available a wide and evolving variety of semi-conductor switching devices with ever-increasing voltage, current and switching speed capabilities.
Circuit designers and their marketing colleagues devised VFDs that promised variable speed operation of AC induction motors with better efficiency, simpler installation, less maintenance and lower cost than the ECD. Encouraged by a plethora of manufacturers entering the market, users began to shift their choices and select a VFD solution in lieu of the ECD. However, VFDs have experienced some installation complications, including:
- Harmonic powerline interference
- Demand for harmonic studies prior to implementation
- Harmonic motor heating and increased losses
- Motor bearing damage
- Early failure of power electronics
- Sensitivity to heat, much of which was generated by the unit’s own losses
- Need for space to house the large cabinets
- Need to air condition space in a majority of applications
- Sensitivity to power quality problems
- Reliability problems (leading to the invention of the “bypass starter”)
- Early obsolescence making repair parts unavailable
- Standby generator interference
- Reflected voltages on long motor leads
Manufacturers and engineers have been able to devise solutions for many of these issues, but these solutions often come with added cost, space requirements and energy losses. For example:
- A large municipal user recently posted bids for a harmonic filter system to mitigate VFD harmonics at a water reclamation plant for an estimated cost of $387,000.
- A Texas consulting engineer recently commented that air conditioning failure was the single most common cause of an outage on VFDs.
As a result of these issues, many users are now returning to the use of ECDs for their variable speed pumping applications. Here are some examples from operations that have returned to this technology.
87th Street Pumping Station
Beginning in 2015, the city of Kansas City, Missouri, needed to add variable speed drives and replace pumps in a large wastewater pumping station. The city elected to specify four 450 horsepower (hp) 514 revolutions per minute (rpm) vertical ECDs at the 87th Street Pump Station. Eddy current technology replaced constant speed motors and pumps whose only means of flow control had been throttled valves.
Blue River Wastewater Treatment Plant
In 2018, 350 hp ECDs were supplied to retrofit three existing constant speed motors at the Blue River Treatment Facility. The influent pump array consisted of seven identical pumps, four of which were controlled with existing VFDs. The other three were rarely used, because their operation at full constant speed resulted in frequent cycling as the pump overran the demand flow.
A structural engineering review was provided to ensure the motor foundation could support the added weight of the ECD. The motors were sent to a local repair facility for inspection and refurbishment under a blanket agreement with that facility. Installation labor for the units was also supplied after the motors were sent, one by one, to be fitted with their new ECDs. A major consideration for choosing ECDs in this application was the lack of available space to house any more VFDs.
Round Grove Pump Station
In 2019, two 1,000 hp, 720 rpm ECDs and induction motors were specified for the new main pumps at the Round Grove Pump Station, replacing equipment that had been damaged when the station was flooded. Motors, ECDs and exciter/controllers were supplied for these pumps.
North East Industrial District (NEID) Pumping Station
Adjacent to the Blue River Plant is the NEID Pump Station. Pumps there were equipped with 500 hp motors and VFDs. In 2020, in a similar fashion to the Blue River project, three units with suitably sized ECDs were retrofitted while reusing the existing motors. This retrofit is especially notable because in this instance, the ECDs were replacing VFDs.
Industrial and municipal plants that need adjustable speed operation for centrifugal pumps need to consider the long-term benefits, expenses and maintenance requirements when choosing drive technologies.