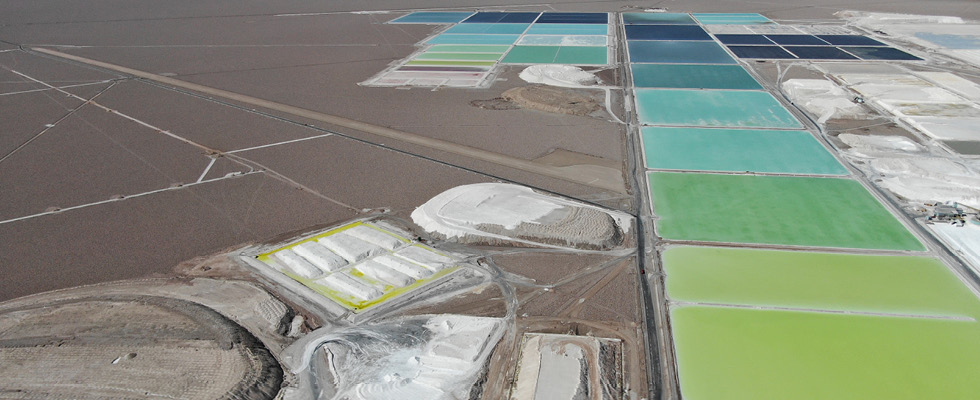
Lithium-ion batteries play a pivotal role in modern power generation, serving as a cornerstone technology for energy storage and distribution. Their high-energy density, long cycle life and efficiency make them indispensable in renewable energy systems, where they bridge the gap between intermittent generation and continuous power supply.
One key application for lithium batteries is storage of excess energy from solar and wind sources for use during peak demand or periods of low generation. Other applications include electric vehicles, electronic devices, smart watches, power tools, e-bikes and scooters and even electric toothbrushes.
Given the far-reaching, global use of lithium batteries, the demand for lithium is at an all-time high, with experts projecting the lithium battery market to reach $189.4 billion by 2032. As such, manufacturers the world over are exploring a number of ways to harvest lithium, including brine extraction, mining and recycling, and pumps are critical in each instance.
Lithium Extraction
Lithium-rich brine deposits are the most common source of lithium globally. These deposits are typically found in salt-rich bodies of water often located in underground reservoirs in geothermal areas.
To extract the lithium from these briny pools, pumps are used to bring the brine to the surface, where it is distributed into large evaporation ponds. Once it is at the surface, sunlight and wind are utilized to evaporate water from the brine, concentrating the lithium content over several months or even years.
During this stage, salts and minerals such as magnesium, potassium and boron are removed from the brine. The lithium brine concentrate is then transferred to a processing facility, where chemicals are pumped into the brine to isolate lithium compounds, such as lithium carbonate or lithium hydroxide, which are vital for battery production.
Lithium carbonate is a stable, less reactive lithium compound and is primarily used in consumer electronics and applications such as ceramics and glass manufacturing. Conversely, lithium hydroxide is a more reactive, higher-purity lithium compound used in applications that demand more battery performance, like electric vehicles.
Chemical-duty, air-operated double-diaphragm (AODD) pumps are used in brine extraction globally at a number of stages, including pumping the brine to the surface as well as drying lithium carbonate later in the process. The suction lift capabilities of an AODD pump make it a great resource for brine extraction.
Lithium Mining
The second most common source of lithium extract is mining spodumene pegmatites, the most abundant and economically viable source of lithium in hard rock mining. These deposits are found around the world, with the greatest concentrations found in Australia, Chile, China, Argentina and the United States.
The lithium mining process begins with the physical extraction of the ore through traditional mining techniques such as drilling, blasting and hauling. Once the ore is brought to the surface, it is crushed and processed to separate the lithium minerals from waste material.
The extracted lithium then undergoes a process called calcination, where it is heated to high temperatures to convert it from its natural alpha form to the beta form, which is more amenable to chemical extraction. The beta-spodumene is then treated with acid or other chemicals to extract lithium, typically in the form of lithium carbonate or lithium hydroxide.
Like lithium extraction from brine, pumps are a critical component of lithium mining. In fact, from the processing plant to treating the minerals with acids to isolate lithium, centrifugal, mag-drive chemical pumps are used at each step of the mining process, including separation, refinement and sintering processes.
Lithium Recycling
One of the most underutilized sources of lithium is from recycled lithium-ion batteries. Not only is this an environmentally friendly option, it is a lucrative one as well. The lithium battery recycling market globally was an estimated $3.45 billion in 2023.
Still, less than 1% of lithium batteries are recycled compared to 99% of lead-acid batteries. One reason may be the difficulty in recycling lithium batteries, as they present significant challenges, both technical and logistical, due to their complex design and composition.
Unlike single-use batteries, lithium batteries are composed of multiple materials, including lithium, cobalt, nickel, manganese, copper and organic electrolytes, which are often interwoven into tightly sealed layers.
Extracting and separating these materials is difficult and energy-intensive, requiring a combination of mechanical, thermal and chemical processes. Recyclers utilize either a high-temperature smelting process to recycle the battery, or they grind the battery down to separate the materials before sending them through a variety of processing streams to create a slurry. This slurry is then further refined via acids such as hydrochloric, nitric and/or sulfuric acids to separate out the lithium (as well as the copper and other minerals).
This is where choosing the right pump for these processes is especially critical. In hydrometallurgical recycling, a common method used to extract valuable metals like lithium, cobalt and nickel, chemical pumps are used to transfer acidic or alkaline leach solutions through various stages of the process. These solutions dissolve the target metals from shredded battery materials, creating a slurry that must be transported between tanks, filters and separators.
High-precision, chemical mag-drive pumps ensure consistent flow rates and pressures, which are essential for efficient leaching, filtration and precipitation. Additionally, centrifugal, sealless, mag-drive pumps handle chemical reagents and wastewater in the recycling process, contributing to safe and controlled material recovery.
This is particularly important given the environmental and economic challenges that further complicate the recycling of lithium batteries. Inefficient recycling processes can result in the release of hazardous materials, such as toxic electrolytes and heavy metals, which pose risks to human health and the environment. Installing an efficient, reliable pump can protect against these hazards.
Pumps are indispensable tools in the diverse methods of lithium extraction, playing a vital role in ensuring the efficiency, safety and scalability of these processes. Whether facilitating the transfer of brine in evaporation ponds, aiding in chemical processing during hard rock mining or enabling advanced recycling techniques for spent batteries, pumps are integral to the flow of materials at every stage.
As the demand for lithium continues to rise with the global transition to renewable energy and electric mobility, innovations in pump technology will be essential for enhancing the sustainability and productivity of lithium extraction.