Dual gas-lubricated seals use a pressurized, nitrogen gas barrier—usually at a higher pressure than the pumped fluid—combined with lift features to separate the seal faces to a small, controlled gap. Lift features—such as spiral grooves, waves, T-slots and hydropad grooves—create aerodynamic lift with the barrier gas pressure and shaft rotation, which generate a high film stiffness. This film keeps the seal faces separated, even during challenging conditions, such as vibration and cavitation. This combination of features and design elements provides advantages not offered by other solutions. “Sealing Sense” articles in Pumps & Systems, November and December 2009, presented an overview of the basic principles of design and application of these seals. This “Sealing Sense” discusses the advantages that these unique seal designs offer when compared to other sealing solutions.
Energy Efficiency, Negligible Heat Generation
The small gap generated by the combination of lift features and pressurized gas means that dual gas-lubricated seals can operate without any contact or wear. The only friction comes from the shearing of the pressurized gas, which at normal pump speeds can be as low as 6 watts (0.008 horsepower). A single liquid-lubricated seal operating at similar conditions may generate up to 300 watts (0.4 horsepower) of friction. The low heat generation of dual gas-lubricated seals typically causes less than 2 degrees of temperature increase at the seal faces, eliminating the need for external cooling. Another advantage is that, because heat generation is so low, virtually no thermal distortion of the seal faces occurs, which must be carefully considered when designing liquid-lubricated seals.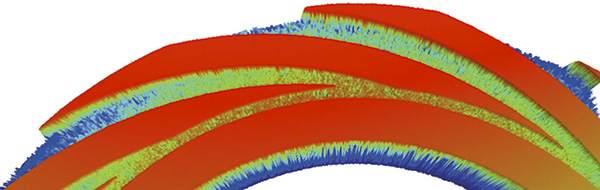
Process Fluid Temperature Control
In addition to low energy consumption, the seal’s low heat generation offers an advantage in applications that are sensitive to temperature changes. Some process fluids must be carefully controlled to a narrow range of temperatures to control a chemical reaction, limit flashing or vaporization, or to maintain the ideal fluid properties for pumping.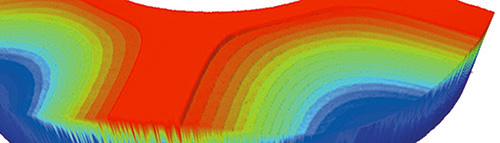
Unaffected by Dry Running
Single liquid-lubricated seals rely on the pumped fluid for friction reduction and heat removal at the seal faces. Cavitation, dry running and other poor lubrication conditions can significantly shorten seal life. Dual gas-lubricated seals are designed to run dry and do not rely on the pumped fluid for lubrication or heat removal. If the pump runs dry, the seal will not be affected. Tank unloading often causes problems for single liquid- lubricated seal installations. Pumps in these applications usually operate for several minutes after the tank empties to strip the tank of as much of the product as possible. Dual gas-lubricated seals offer a good alternative if a reliable pressurized source of gas is available at the unloading station. They require no regular maintenance to refill a barrier fluid tank. Dry running tolerance is another advantage of the dual gas-lubricated seal compared to many sealless magnetic drive pump designs. These pumps often rely on ceramic journal bearings that require lubrication and will fail if the pump runs dry.No Emissions, No Contamination
Pressurized dual seals, whether liquid lubricated or gas lubricated, will only leak their respective barrier fluids to atmosphere. This can be critical in situations in which volatile organic compounds (VOCs) are pumped and regulated by the Environmental Protection Agency. While it is possible to obtain low emissions of 500 parts per million (ppm) or less with single seals, the application must be carefully monitored and have well-controlled equipment operation to achieve this. Dual pressurized seals can achieve zero emissions consistently, even under difficult operating conditions.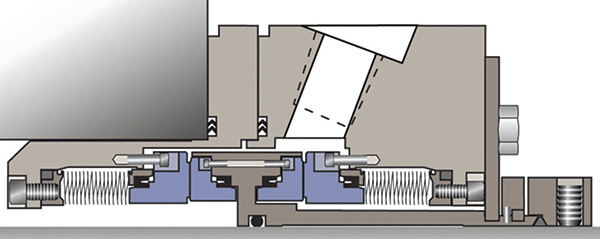
Low Cost of Ownership
Dual gas-lubricated seals can also offer an overall lower cost of ownership as compared to liquid-lubricated seals. The reduction of energy consumption is a major contributor to this advantage as confirmed by analysis with the FSA Life Cycle Cost Estimator. While the initial capital cost for a dual gas-lubricated seal may be higher than that for a comparable liquid-lubricated seal, when the total cost for the seal and its support system is included, the dual gas-lubricated seal may become more economical because of the simplicity of its support systems. This advantage becomes more compelling when the installation of dual gas-lubricated seals and their systems are considered. The control panels for dual gas seals usually only require simple inlet and outlet connections. However, a liquid seal requires more complex plumbing with proper location, piping slope and cooling water connections. Dual gas-lubricated seals also require little, if any, maintenance when compared to the regular refilling of dual liquid-lubricated seal support fluids.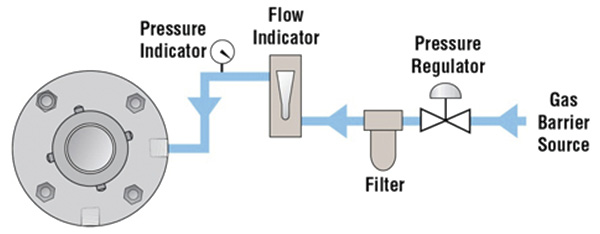