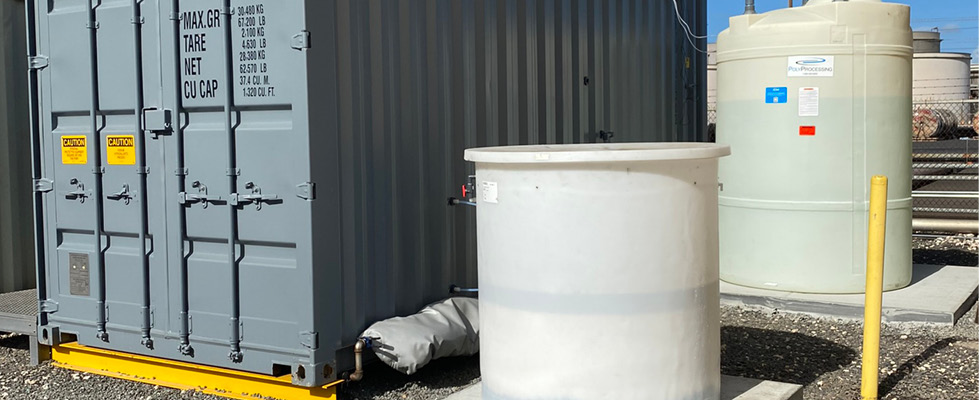
Buying bulk sodium hypochlorite (bleach) has historically been the go-to method of securing disinfectant chemicals to treat cooling tower biofouling at power plants. The upfront costs of installing electrochlorination technology to make bleach on-site have been too high to justify the investment. When comparing this capital cost to the low cost of bulk bleach, switching to on-site generation was always a nonstarter.
But in a post-COVID world, bulk bleach is no longer the cheap commodity it once was. Prices have increased from a pre-
COVID average of $0.60-$1.75 per gallon to as high as $5+ per gallon for remote locations. Additional downsides to buying in bulk include relying on a more volatile supply chain with a higher risk of shortage, the safety risks and liability of
transporting, storing and handling dangerous chemicals, the cost of chemical degradation caused by storage temperature and time and the heavy use of transportation and resulting carbon emissions. Meanwhile, the cost of on-site generation through electrochlorination has remained relatively stable through technological advances, and it only requires salt, water and electricity. On-site generation resolves every problem of bulk bleach delivery and storage and creates measurable value in lower operating costs, improved safety, increased sustainability and a more resilient operation.
Trends are converging to a place where the capital costs of installing on-site biocide generation systems are more than rationalized economically, with a return on investment (ROI) of less than three years for a growing number of power plants.
Managing Cooling Tower Water
Water is both essential for life and a highly destructive substance. As such, managing water is a critical and complex activity in cooling tower operation to maintain peak performance and efficiency. Operators must actively battle the corrosive and scaling nature of water while also preventing microbial life from causing biofouling, which reduces efficiency and can also present a biological hazard (often legionella) to operational staff and visitors. Disinfectants must be carefully balanced to effectively inhibit biofouling while minimizing corrosion and scaling.
Cost Savings
While the savings potential will vary from plant to plant, many more power plants are now discovering economic advantages from on-site generation that were not available just a few years ago. On-site electrochlorination systems can cost anywhere from $15,000 to over $1 million depending on size, scope and source water. These costs can be recouped quickly through operational savings because the cost of generating bleach on-site usually hovers around $0.60 to $0.70 per pound—which was the pre-pandemic cost average of bulk bleach.
Based on the concentration and amounts of bleach a plant needs, what it pays for bulk bleach and what it pays for water, electricity and salt, plant operators can calculate the amount of savings they can realize from generating their own electrochlorination systems instead of buying premade disinfectants. In many cases, facilities can recoup their capital costs in less than three years, after which they can make bleach at a fraction of the cost of what they would pay for market price bulk bleach.
The cost of water is a critical part of the economic equation. The degradation of bulk bleach contributes to the formation of by-products, which increase total dissolved solids (TDS). With more TDS, there are more frequent blowdowns needed to maintain target conductivity and prevent corrosion, scale and biofouling. Bleach generated on-site does not exhibit this degradation or cause these by-products and therefore optimizes blowdown, which results in reduced water consumption and associated costs of makeup water. A single on-site generator can be used for multiple applications at a site, delivering even more value and helping facilities recoup their capital investment faster.
In addition to cost savings, plants can realize other valuable benefits.
Improved Safety, Less Liability
Generating biocides on-site is safer primarily because it eliminates the transportation, storage and handling of hazardous chemicals. When plants make their own chemicals in the amounts they need for a short period of time, they can eliminate the risk and liability of storing hazardous chemicals on their site. The overall truck traffic to a plant can be reduced significantly with on-site generation, further improving a plant’s safety and security profile. It takes more than four deliveries of 12.5% bleach to equal the chlorine equivalent produced
by one truckload of salt, cutting truck traffic dedicated to water disinfecting activities by 75%.
Another safety advantage of on-site electrochlorination systems is that the technology can produce a nonhazardous 0.8% bleach solution. At this concentration, this chemical does not present a threat to public safety or require Occupational Safety and Health Administration (OSHA) process safety management, U.S. Environmental Protection Agency (EPA) risk-management planning, special personal protective equipment or special containment provisions in case of leaks. Although hydrogen is produced during brine electrolysis, systems have built-in mechanisms to contain, rapidly dilute and carefully vent this potentially dangerous gas into the atmosphere.
Greater Environmental Sustainability
As the climate continues to experience rising temperatures in air, surface water and seawater, it is becoming harder for cooling towers to do their job. Hotter temperatures exacerbate many problems faced by cooling tower operators, especially regarding biofouling. Not only is biofouling more prolific with warmer air and water, but ambient heat increases the speed of degradation for bleach as well; thus, both the problem and the solution are made worse.
Many of the advantages already mentioned also deliver greater environmental sustainability. With as-needed on-site manufacturing of bleach, a plant can eliminate the waste of chemical degradation. Less chemical transportation, storage and handling result in a reduced risk of environmental spills. Substantially reduced trucking reduces carbon emissions.
In an age of increasing water scarcity and unpredictability, water consumption is both an environmental and an economic concern. On-site generation leads to less frequent blowdowns and better water conservation.
Improved Resiliency & Future Proofing
By generating its own bleach, a plant can stop relying on a volatile market that is more vulnerable to price fluctuations, delivery delays and shortages compared to water, salt and electricity, and it can extinguish the threat of supply degradation due to heat or time. On-site generation better ensures a fresh and reliable supply of disinfectant than depending on a supply chain that, since the pandemic, has been proven to have significant weaknesses. Decentralizing the manufacturing of biocides helps facilities build a future that is more resilient and less susceptible to failure.
While on-site bleach generation was previously not a cost-effective option for most power generation plants, this is no longer the case. Due to the rising costs of bulk bleach and improved electrochlorination technology, many more power plants can now realize an ROI of less than three years due to operational savings from lower chemical and water costs. Additional benefits with indirect cost savings include greater safety, reduced risk and liability, better environmental sustainability and improved resiliency.