American municipalities face aging infrastructure problems in almost every aspect of their services to citizens, including roadways, electrical distribution, water and sewer distribution, and collection and treatment processes. Variable frequency pumping equipment in treatment plants and pumping stations can be especially vulnerable to early failure as a result of the repair-or-replace dilemma. Repairs may be impractical because of obsolescence on the part of the component manufacturers or equipment manufacturers. A recent survey of more than 200 water and wastewater professionals reveals that this is a concern in their industries. More than 75 percent of respondents reported that aging infrastructure issues have affected their plant's performance, breakdown frequency or capital equipment budgets (see Figure 1).
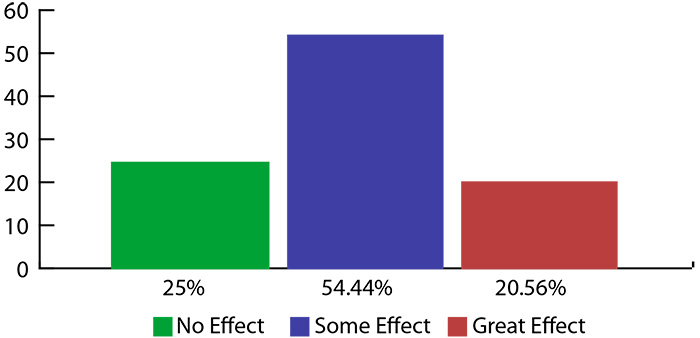
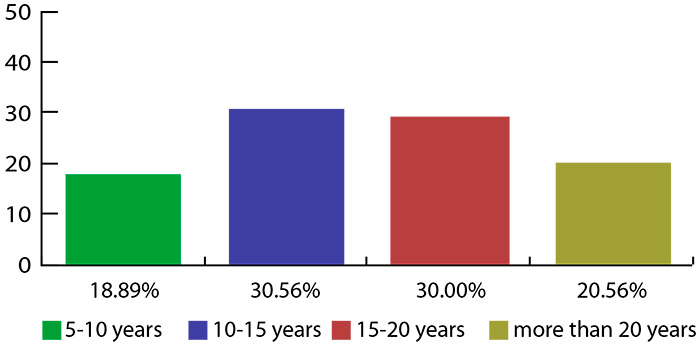
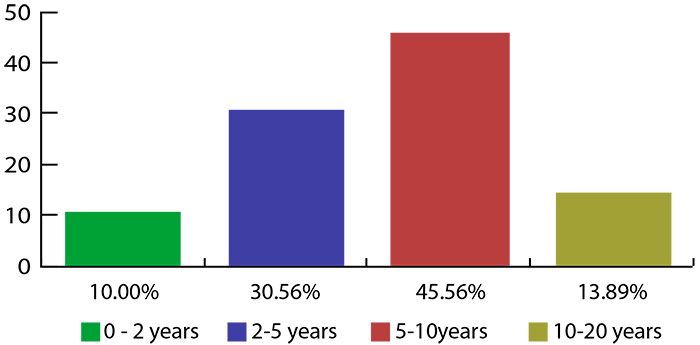
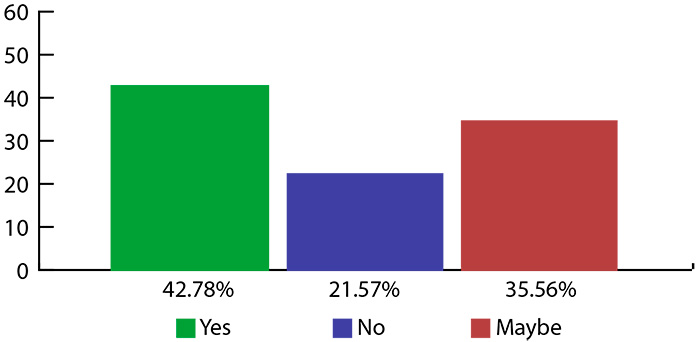
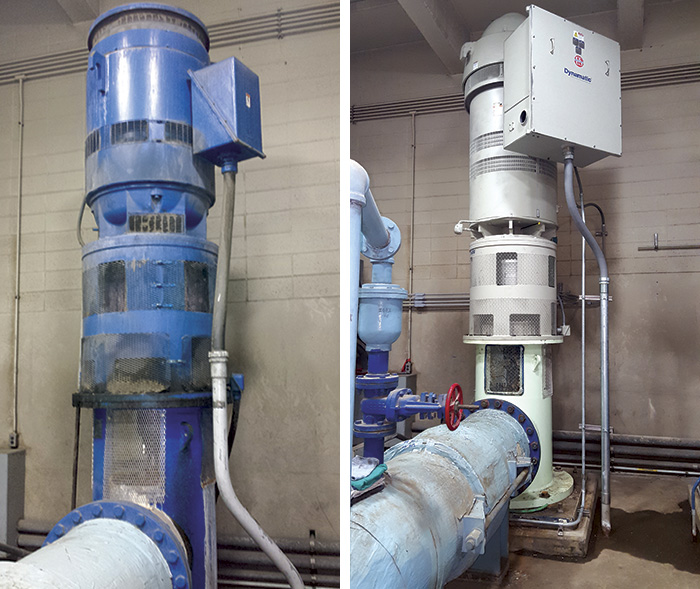