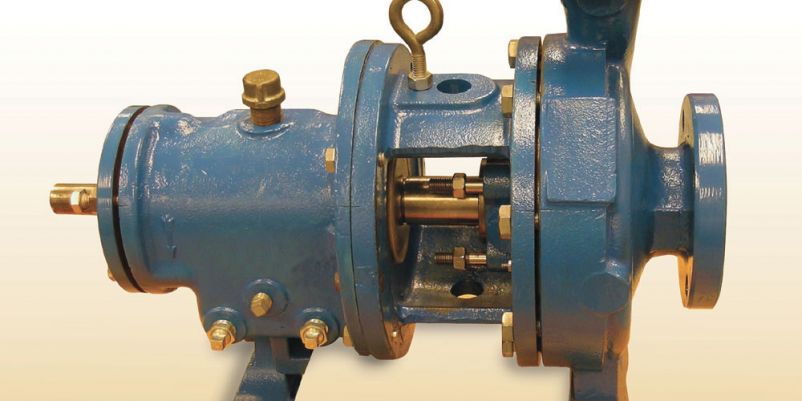
Engineers often worry they are being conservative in their system design. There are many uncertainties in the design process including differences in actual operating conditions, varying fluid properties, component degradation over time, pipe scaling and more. Engineers account for these items using design factors to prevent undersized components from being purchased. They also account for the effects of aging on the system. However, some engineers fail to consider that applying too much of a safety margin to a design can actually have the effect of increasing wear on components and decreasing system life, especially when sizing pumps. When selecting a pump and piping system, the primary goal is typically to achieve the required pressure and flow for the application, whether this is a cooling water system, fuel pipeline, chemical production plant or one of many other applications. The required flow rate for the system is used to determine the total dynamic head at the pump, which is then used to compare pump curves for potential pumps. Oversizing or undersizing a pump can have a serious impact on the system, which is why using an accurate operating point for this process is crucial. If the chosen pump is undersized in terms of power, a lower flow rate than required will be achieved in the system. This will either require additional pumps or adjustments to the system, such as opening discharge valves and adding recirculation lines. An oversized pump will deliver more flow than is required for the system. Depending on the application, it may be necessary to reduce the flow with a throttling valve, or by trimming the impeller. In cases where the pump operating point can be corrected for by simply adjusting valves in the system, it may appear to have little effect on the system. However, the effects of oversizing or undersizing the pump become more apparent when considering the pump efficiency. The best efficiency point (BEP) is the ideal operating point for the pump at which the maximum percentage of energy used to operate the pump is being transferred to the fluid. As the pump operating point is shifted away from the BEP, several things occur. The most obvious effect is that the efficiency decreases, requiring more power to be used by the pump. This energy not being transferred to the fluid has to be outlet in other forms such as heat or vibration. So, as efficiency at the pump decreases, the amount of vibration and heat being generated at the pump increases. In small amounts, this has little effect on the pump, but the farther away that the pump is operating from BEP, the greater this effect will be. It is generally recommended by centrifugal pump standards such as the Hydraulic Institute (HI) standard HI 9.6.3 to operate the pump within approximately 80 to 110 percent of BEP to avoid these effects. Above this, the operator risks cavitation from a low net positive suction head (NPSH) margin, as well as damage from vibration and heat. Below 80 percent of BEP negative effects such as pump seizure, low flow cavitation, fluid recirculation and high temperatures can occur. Over time, high maintenance costs, high energy costs and a lower pump operational life can result from this kind of pump operation. The question then is how can the engineer effectively employ design factors to avoid either undersizing or oversizing the pumps in their system?