Last of Four Parts Editor's Note: While running a pump at its best efficiency point saves money, reduces downtime and improves performance, many plant managers are unaware of how their equipment is actually performing. This series, which began in the July 2015 issue of Pumps & Systems (Read the first part of this series here), depicts a real-world scenario that is intended to illustrate the importance of monitoring pump efficiency. Last month, the team at the Blue Creek municipal plant discussed the correct clearances between the wear rings of a pump (Read the third part of this series here). Based on a chart of recommended clearances, Sandy, a Duck Pump Company engineer, predicted the clearance for the 12.125-inch rings would be about 0.023 inches. Charlie, plant manager, was gathering the data to review the impact on the efficiency measurements that Bob from Duck Pump Company and plant maintenance supervisor Jim had looked at in July. "OK, guys." Rusty, plant mechanic, pointed at the whiteboard of the conference room, where he, Charlie, Jim and storeroom manager Grady Cricket gathered to review the data and compare it with what Sandy told them last month. "I've got the measurements, and it's not 0.023 inches. I got nearly triple that. It's a huge clearance—almost seventy thousandths—and it's not a used rotor at all. This is a spare rotor we got at the storeroom. I don't know if it's similar to the one Bob tested in the field in July, but if so, we've got a problem!" Charlie pulled out the chart that Sandy gave him at the last meeting. "Let's see… The article where this chart came from talks about a smaller pump, about 16-by-18 in size, while our unit is a lot bigger—30-by-36. But if we assume the results are roughly applicable, we would expect, according to the article, about a 4 percent efficiency degradation with ring clearances double the size. Our case is triple the size, so should we assume, say, about a 6 percent degradation or so? I'm not a hydraulics guru, but just trying to make some sense with these numbers. Would that be a reasonable ballpark guess?" "I think that makes sense, Charlie," Jim said. "We can get a more accurate calculation from Sandy to verify, but for now, that is probably a close-enough estimate. So, as Bob told me in July, the pump he measured with his pumps reliability and energy savings monitoring (PREMS)-2A unit, gave him a performance drop of about 13.5 percent. According to the calculations, that led to about $125,000 per year wasted. If the real number is 6 percent, that would be roughly $60,000 in energy loss. In either case, we are wasting money because of flow recirculating through the incorrect clearance. Like you said, we still haven't determined if the pump Bob measured is similar to the spare rotor we just reviewed, but so far it looks to me like it has nothing to do with actual wear but with a mistake the Duck Pump company made with the brand-new clearances when they delivered the pump." Charlie asked Jim to email the findings to Bob and Sandy. "Let's also get Bob to come back and do his measurements on the other pumps as well. We've got five pumps at the main booster line and usually run only one or two—three at the most, depending on the demand—with the other units essentially installed spares. Which one did Bob measure with his PREMS-2A unit, Jim?"
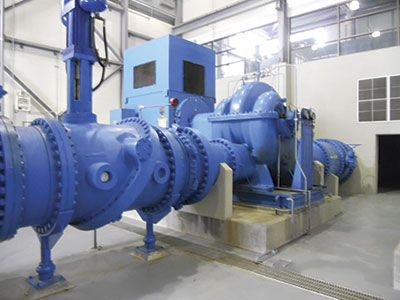
- Unit 1: (same as tested originally): 13.5 percent off (below) on efficiency
- Unit 2 and 4: 7 percent below
- Unit 5: 5 percent below
- Nelson, E., Maintenance and Troubleshooting of Single-Stage Centrifugal Pumps, TX A&M Pump Symposium, 1984
- PREMS-2A Pumps Reliability and Efficiency Monitoring System, rev. 2A, March 2015:
- doctorpump.com
- pumpingmachinery.com/pump_school/pump_school.htm (PVA module 10A)