08/25/2015
Part 3
Editor's Note: While running a pump at its best efficiency point saves money, reduces downtime and improves performance, many plant managers are unaware of how their equipment is actually performing. This series, which began in the July 2015 issue of Pumps & Systems (Read the first part of this series here), depicts a real-world scenario that is intended to illustrate the importance of monitoring pump efficiency.
Last month, Bob Sellers from Duck Pump Company visited Jim, a maintenance manager at the Blue Creek Municipal Water Plant. After completing some testing, they discovered the plant's pumps were operating at reduced efficiency. Bob recommended that the plant repair the pumps and sent Jim and his team a quote for the job (Read the second part of this series here).
To investigate the problem further, Jim and his boss Charlie visited the storeroom to inspect the rotating assembly of the large double-suction, split-case pump. Grady, storeroom manager, and Rusty, a plant mechanic, completed the basic inspection and discovered that the entire rotating assembly was non-magnetic—with the exception of the wear rings.
They were concerned that what they thought was a completely stainless steel rotor was composed of regular carbon steel wear rings.
That, they concluded, could be causing rusting and wear, leakage across the rings, and decreased efficiency. Hoping to remedy the problem, Bob requested that Sandy from the Duck Pump engineering department come to answer the plant's questions and help clarify the situation.
"Hi Sandy!" Charlie greeted her as she and Bob stepped out of the car. "Good to see you. I'm glad Bob brought some reinforcement to help us troubleshoot these pump problems we seem to be having."
"Sure thing, Charlie. That's why I'm here. Bob said you had some questions on the metallurgy of the pump rotors. Can we see the rings?"
"Of course. We've got them in the conference room—both the impeller ring and casing ring, along with the magnet. It doesn't stick, so we suspect they're not 316 stainless steel, as compared with the rest of the rotor."
Sandy touched the rings with the magnet.
"You are right, guys. It doesn't stick, but that doesn't mean it is plain carbon steel. According to our specs, these are 416 stainless steel. The 400 series is called martensitic stainless, and it's not magnetic. The 300 series is also stainless but austenitic, and it's not magnetic. Both types are good against corrosion, but the 300 series is especially good against cavitation, which is why your impeller is 316 stainless steel and the rings are 416."
Rusty was not convinced. "But look, Sandy—the impeller is soft. I just scratched it a bit with a knife blade, and it cuts a groove in it like butter. How can it resist cavitation?"
"True, Rusty. 316 stainless steel is soft—but only initially." Sandy was flipping through her files. "Once in service and as it begins to get bombarded by cavitation (which is essentially a high energy of the imploding water bubbles against the impeller blades), the impeller material work-hardens, and any cavitation can't damage it from then on. But the 400 series is better for wear rings. Cavitation is not really an issue there, but they need to be hard enough to withstand occasional contact or wear by particulates like sand and grit."
"But Bob did this testing in the field and told me we are losing efficiency." Jim pointed at Bob's report. "He told me it is costing us a lot of money because the rings are wearing. If they are so hard, how come they wear so quickly?"
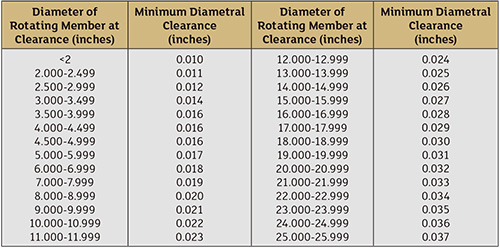
Part 4 of this series will reveal the measured wear ring clearances and explain the efficiency problem Jim discovered in Part 1. Read part 4 here.
References
- L. Nelik, Pumps & Systems magazine, March, 2007, page 18, "How much Energy is wasted When Wear Rings are Worn to Double Their Initial Value?"
- PREMS-2A Pumps Reliability and Efficiency Monitoring System, rev. 2A, March 2015: www.doctorpump.com www.pumpingmachinery.com/pump_school/pump_school.htm (PVA module 10A)