The term “water hammer” is used to describe pressure surges within a piping system. There are a range of mechanisms and triggers for water hammer, and having a clear understanding of what is causing the phenomenon in a particular installation is key to identifying the right solution. One cause of water hammer is when the leading edge of a fluid column in a pumping system encounters a blockage, such as a suddenly closed valve. When this happens, the flow of water at the leading edge is instantly halted, but the fluid behind is still moving and starts to compress. Because of this compression, a small amount of fluid continues to enter the pipework even though the water at the leading edge has stopped moving. The kinetic energy of the water in the system is converted to pressure energy as the water compresses. This pressure energy cannot continue past the blockage in the system. Instead, the pressure wave generated by the compression of water in the pipe will travel back upstream. The other primary cause of water hammer is water column separation and closure. This occurs when the column of liquid water within a piping system is separated and subsequently closes again, generating a damaging shockwave. This can occur in a two-phase system—one in which water changes state and can exist as both a liquid and a vapor in the same confined volume. This “phase change” (liquid water to water vapor) can take place whenever the pressure in a pipeline is reduced to that of the vapor pressure of the water.1 These various causes of water hammer have a number of triggers. Pump starts and stops can cause water hammer through both mechanisms. Additionally, a rapid change in flow and system pressure during starting or stopping can cause sudden closure of check valves, while changes in the direction of flow can induce water column separation. Regardless of the cause, the increased pressure generated by the water hammer phenomenon can cause significant damage to any system not designed to accommodate the stresses, leading to bursting pipes, damaging valves and more.
Calculating the Damage
The damaging potential of water hammer can be calculated using Equation 1. As an example, water is being pumped at a flow rate of 10 feet per second (ft/s).P(additional) = aV / 2.31g Equation 1 Where: P = additional pressure created in the system a = 4,860 ft/s (the speed of the pressure wave) V = velocity of the flowing water in the pipe (ft/s) g = universal gravitational constant (approximately 32 ft/s2)
A valve in the pipeline is closed instantaneously (one of the primary causes of water hammer), stopping the flow of water in the system. Using the formula P(additional) = aV /2.31g, it is evident that an additional 657 pounds per square inch (psi) of pressure will be created within the pipe. If the system is not designed to cope with the additional pressure, severe damage is likely to occur to the valves, pipework and/or pump.
Finding Solutions
Solving the water hammer problem requires either mitigating its effects or preventing its occurrence. There are a number of solutions to consider when designing a pumping system. Pressure tanks, surge chambers or similar accumulators can be used to absorb pressure surges, and they are useful tools in the fight against water hammer. However, preventing the pressure surges is often a better strategy. Controlling valve closure time is one solution. As previously mentioned, sudden closure of a valve is one of the primary causes of water hammer. Of the many variables at play within a pumping system, valve closure time significantly impacts the likelihood of damaging water hammer occurring. It is a factor over which operators have a level of direct control. Equation 2 shows the relationship between valve closure time and the magnitude of the water hammer pressure surge.P = 0.07 (VL / t) Equation 2 Where: t = valve closing time in seconds L = length of the pipe between the barriers in feet V = flow velocity in ft/s
The additional pressure generated by the closure of a valve is inversely proportional to the valve closure time. That is, the more slowly the valve is closed, the less significant the increase in pressure will be. By careful consideration of the variables within the end user’s control (closure time and flow velocity), incidence and intensity of water hammer can be notably reduced. Controlled valve closure can be achieved manually or through motorized valves. Electronic speed control during pump starting and stopping is another potential solution. Electronic motor control devices such as soft starters and variable speed drives (VSDs) can be used to control the speed of the pump during starting and stopping. This allows for a more gradual increase or decrease in pump speed (and hence, flow and head/pressure) to prevent water column separation, flow reversal and sudden check valve closure. Controlled starting and stopping of pumps also offers other advantages, including reducing mechanical stresses on the system and electrical supply caused by direct on line (DOL), across the line (ATL) and electromechanical starting. This results in reduced maintenance and extended life. Furthermore, soft starters and VSDs can provide a range of advanced motor and system protection functions as well as monitoring and control options. Examples of possible protection provided by these methods of controlled starting and stopping include:
- pump/motor overload protection to detect burst pipes
- undercurrent protection to detect blocked pipes
- phase rotation protection to prevent reverse rotation of the pump
- phase loss protection to prevent damage from power disturbances
- instantaneous overcurrent protection to prevent pump damage due to debris
- automatic timers and schedulers for control of operation
- operational logs and recording
Examining the Curves
The system curve displays the relationship between flow rate and pressure in the system. It is made up of two components: static head and dynamic head (see Figure 1).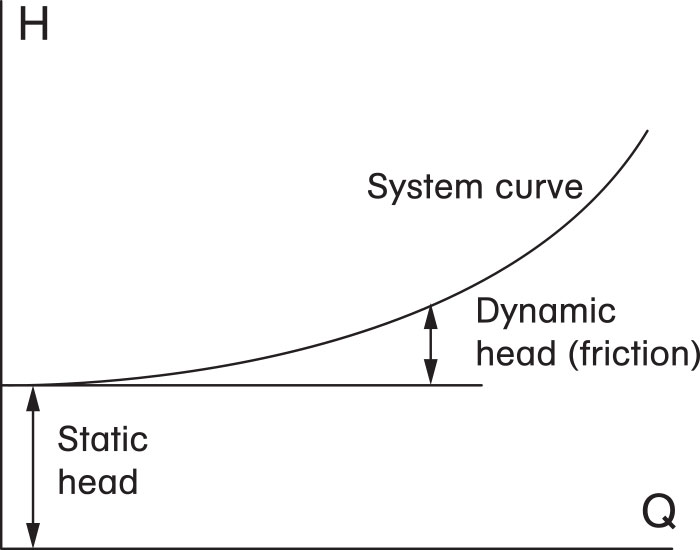
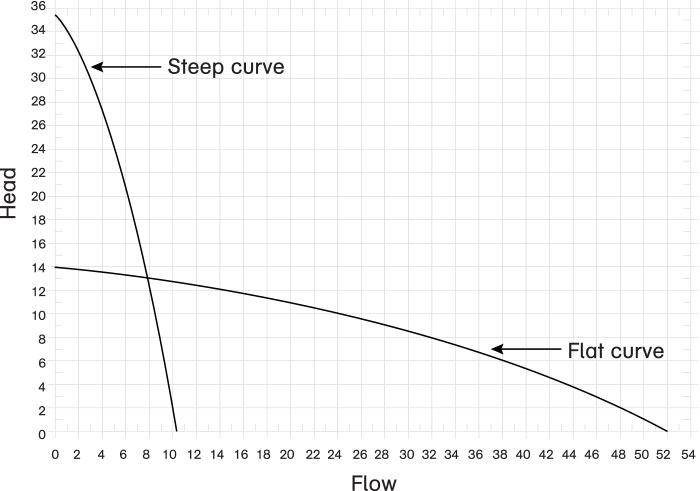
Selecting Soft Starters
With an understanding of water hammer mechanics, the system curve and the pump performance curve, the next step is to explore the correct application of soft start technology to prevent water hammer. Not all soft starters are created equal. Over the past 40 years, the starting and stopping modes offered by soft starters have considerably evolved. Voltage, current and, more recently, torque control are common approaches to starting and stopping. Each influences acceleration (and deceleration) but none provide direct control.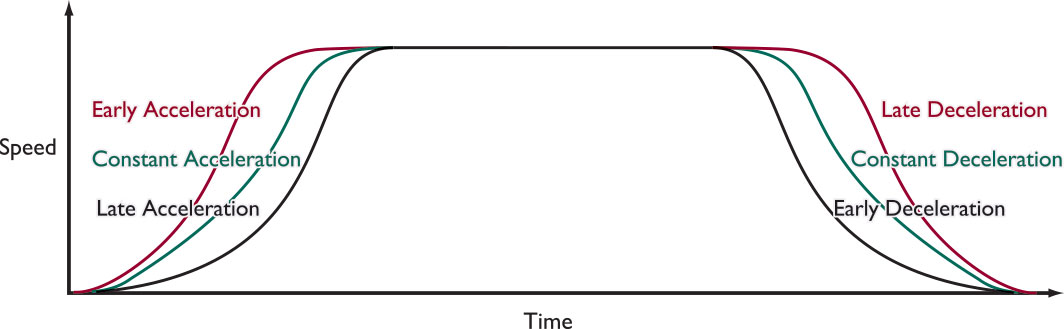
- Joe Evans, Ph.D, “Waterhammer Part 2 – Causes & Variables,” www.pumped101.com