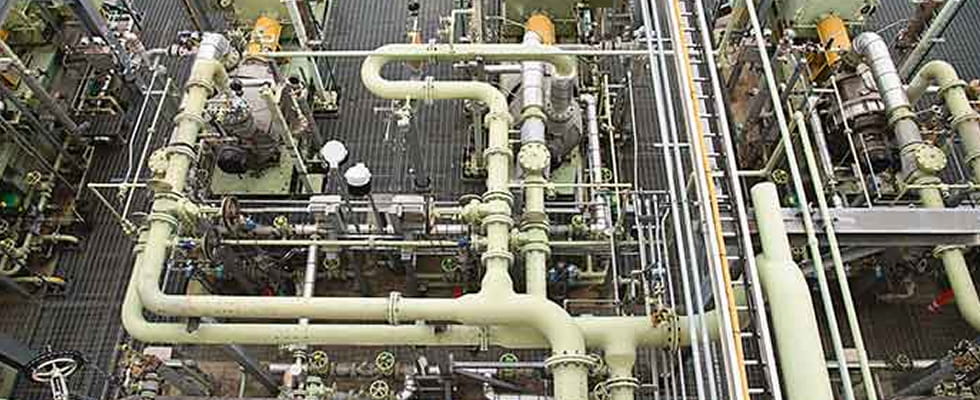
Gas flaring—the process of burning off associated gas from wells, hydrocarbon processing plants or refineries, either as a means of disposal or as a safety measure to relieve pressure—has extensive ecological and economic impacts. Managing the risks of flare gas is one of the leading challenges facing the oil and gas industry today. While the composition of flare gas varies by application and facility, more than 250 hazardous substances have been identified in flare gas. These include carcinogenic substances such as benzopyrene, benzene, carbon disulphide, carbonyl sulphide and toluene. Dangerous metals, such as mercury, arsenic and chromium, as well as poisonous gases like hydrogen sulfide and sulfur dioxide, are also present. Flare gas is one of the major factors contributing to climate change. Oil production facilities around the world burn off approximately 140 billion cubic meters of natural gas annually, causing more than 300 million tons of carbon dioxide (CO2) to be emitted to the atmosphere. (1) These chemicals can have devastating impacts on local populations because they contribute to serious health conditions, especially in newly industrializing countries with significant oil production levels.
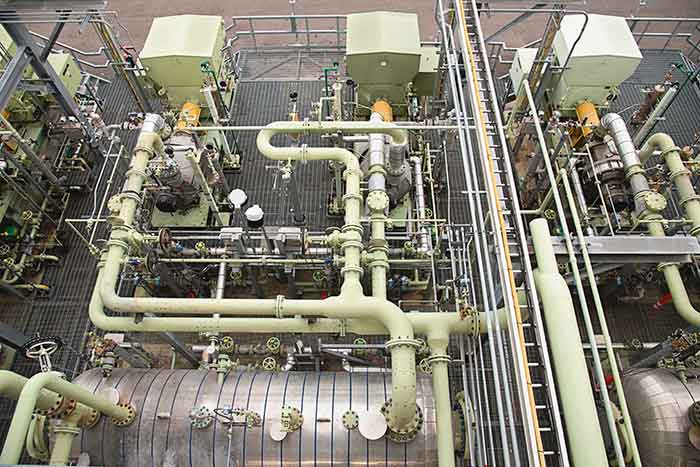
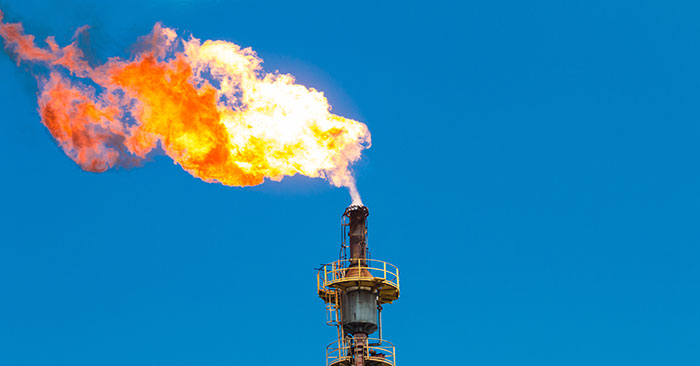
Flare Gas Recovery Systems
While the flaring of gas plays a vital role in plant safety and excess gas disposal, oil and gas operations need to reassess how they recapture these materials. One way to prevent toxic substances from entering the atmosphere is to use a flare gas recovery system. These systems can recapture up to 98 percent of emissions for use in other plant processes, such as the heating gas system. Flare gas recovery systems reduce noise and thermal radiation, operating and maintenance costs, air pollution and gas emissions, the risk of harming human health, and fuel gas and steam consumption. The compressor, a vital component of a gas recovery system, must be reliable and able to withstand the aggressive conditions typically found in oil and gas production, including below freezing temperatures, hot and humid climates, sandstorms and intensive sun radiation.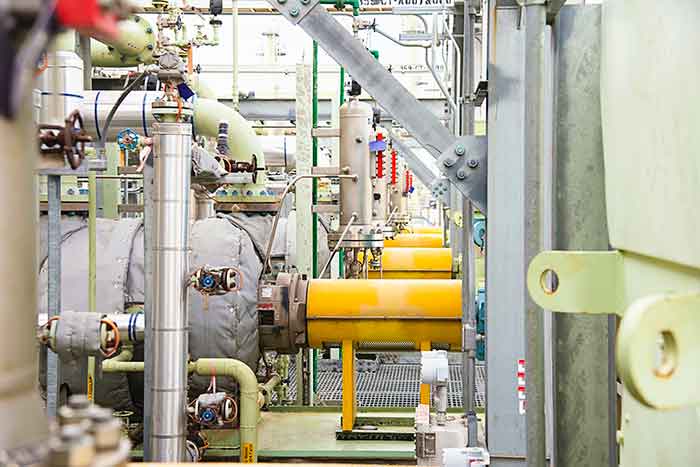