It is estimated that by 2020 there will be as many as 50 billion devices connected to the Internet of Things (IoT) operating in the consumer and industrial world. Additionally, there may be as much as 44 trillion gigabytes of information transferred, utilized and analyzed. In today’s major technological advances in plant assets, there is a significant increase in data that can be captured and transferred using the IoT. Modern sensors can be used for vibration monitoring; non-invasive motor testing; ultrasonic, electrical capacitance tomography; infrared thermography; oil analysis; and much more. Many of these sensors can be attached to equipment by magnets, screws or adhesives to provide feedback on the health of those assets. The goal of using these sensors is to monitor asset condition and take corrective action when anomalies are detected. Preventing equipment failure can provide tremendous bottom-line savings. With this information available, it is important to ensure that corrective action serves a proactive purpose rather than reactive. As organizations further develop Industrial Internet of Things (IIoT) strategies for their operations, they will be increasingly analyzing tremendous amounts of data. This has forced some organizations to create the role of chief data officer (CDO) to help decipher this immense amount of information, as well as develop proactive plans and key performance indicators (KPIs) to improve their operations. For example, a plant with annual revenues of $700 million may spend as much as 5 percent of revenues on maintenance, repair and operations (MRO) to keep vital assets running. Reducing these costs by 2 percent by incorporating advanced asset monitoring and proactive strategies can reduce overall expenditures by $14 million a year. Some suppliers provide systems that improve data management to help put necessary information into the hands of maintenance personnel immediately.
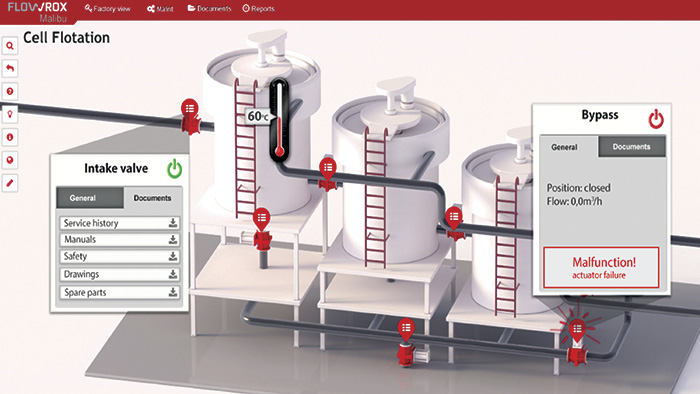
3-D Virtual Environments
Certain software can incorporate a 3-D virtual environment of an entire chemical plant, subprocess, or individual asset or system. The information can be set up in layers so the plant manager can view production matrixes and failure points or bottlenecks. The safety manager may view hazardous areas or key areas of concern. For instance, a chemical release can be monitored with gas sensors and tracked so that only the plant’s affected portion needs to be evacuated. The plant’s unaffected area can continue to work normally. Using the software, the maintenance team can navigate down to specific portions of the plant to individual assets. The maintenance professional can view previous failure reports of a given asset and learn possible remedies for the affected asset.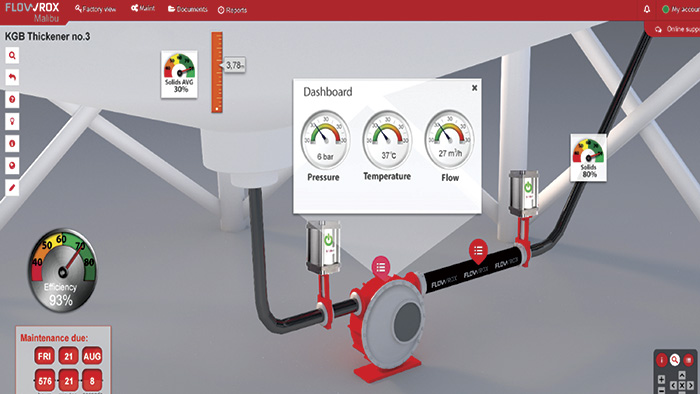