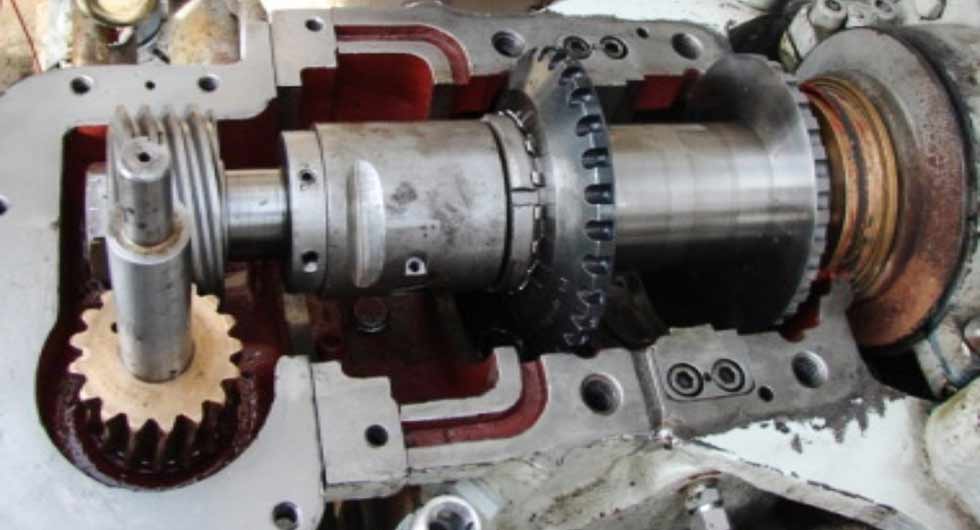
Anyone responsible for purchasing a new piece of plant equipment will ask the question: Will it deliver a swift return on investment (ROI)? When specifying pumping systems, this question will cover implications such as ensuring optimum reliability and productivity, minimal downtime and enhanced pump life span.
The importance of undertaking detailed analysis of the total cost of ownership (TCO) of a pump, which factors in projected running and maintenance costs as well as initial capital outlay, is arguably greater as the global focus on sustainable manufacturing practices intensifies. Quantifying energy use and water consumption, including effluent treatment costs, now carries environmental as well as financial significance.
The sealing solutions specified as part of a pump purchase can have a crucial bearing on the TCO when a pump is expected to operate efficiently over a period of decades. Therefore, it makes sense to consider which sealing systems offer not only the swiftest ROI but also the surest over the long term.
In addition, it is worth noting that, when purchasing from an OEM, the pump build can be adjusted to suit the preferred specifications. This is important where sealing solutions are concerned.
Lip Seals
The health of rolling element bearings can be the foundation on which a pump thrives or flounders. Bearings failure accounts for around 40% of rotating equipment stoppages in a plant, with contamination caused by water or process fluid ingress into the bearings chamber cited as a key cause.
A lip seal is a commonly used component employed in an effort to minimize this fluid contamination, but it has its disadvantages. Lip seals rely on surface contact with the pump shaft to create the seal. The resulting friction means that a lip seal can start to deteriorate almost immediately following installation, allowing leakage into the bearings chamber and leading to bearings failure and downtime. Damage to the pump shaft itself can be another costly consequence of the friction.
A motive for using lip seals is their low initial cost; so, it is worth calculating how many hidden costs could accrue as a result of repeat orders and scheduled downtime for maintenance and repair. There is also the more serious financial impact of unscheduled downtime caused by abrupt and unforeseen bearings failure to be considered.
Bearing Isolators
The repeat cycle of contamination, bearings failure and operational downtime can be prevented at the specification stage.
For example, regardless of the OEM pump build, advanced noncontacting bearing isolators can be requested as an alternative to lip seals.
These use the centrifugal force of rotating equipment to open a micro gap in the seal to allow the bearings to breathe, then immediately close the gap when the equipment is not running and the centrifugal force stops. This ensures that bearings are protected from the ingress of dust and water from the surrounding environment.
One paint manufacturer discovered the cost-efficiency of this dynamic lift technology when it replaced an OEM lip seal with a bearing protector.
Leaking paint from a badly aligned entry paint mixer was entering the motor bearing through the seal, causing the mixer motor to fail on average every two-and-a-half months. Each breakdown was costing around $1,800 (not taking into account loss of production).
The cost of replacing the lip seal with the bearing protector was repaid within one month of fitting and meantime between failure (MTBF) increased by 540%. The manufacturer saved around $10,000 in reduced maintenance costs and an expected nine-and-a-half days per year of lost production.
Savings & Sustainability Goals
The noncontacting, frictionless design of bearing isolators has the additional advantage of reducing the amount of energy required to drive the pump shaft.
The result is a guaranteed reduction in energy consumption over the long term, which has positive implications for companies looking to reduce their carbon footprint as well as keep a tight rein on operational costs.
When the less obvious long-term benefits of sealing solutions are considered, the immediate appeal of a low initial cost price of a sealing solution might begin to pale. Take the example of a pump specifier who selects a double mechanical seal with an advanced continuous loop water management system.
The environmental value of this choice is clear: A continuous loop water management system employs an integral vessel to provide a constantly recycled supply of clean, cool flush water to the seal faces, reducing wastage to virtually zero.
However, if the year-on-year costs associated with evaporation processes, or water treatment/effluent charges are taken into account, the ROI on this solution would be persuasive.
An international packaging and paper group that replaced 167 quench-to-drain seal support systems with continuous loop water management systems, conserved more than 4.5 billion liters of water over a six-year period. Moreover, the upgrade brought an ROI in just one year and annual savings of around $781,000, excluding effluent treatment costs.
When sealing solutions are proven to achieve the combined goals of improved pump reliability, reduced downtime and quantifiable benefits to both the environment and the bottom line, consider them at the specification stage.