Operators of general-purpose steam turbines have long stated the shortcomings of conventional carbon ring seals. One drawback is wear at the ring’s inner bore, which gradually increases shaft clearance and steam leakage and leads to regular replacement—as often as four times per year. Despite their disadvantages, carbon rings remain the standard in general-purpose steam turbine sealing. Because carbon rings are simple to install and have a replacement cost of less than $1,000 for a complete set, the cost of maintaining sealing with carbon rings may seem modest. However, there are further costs associated with the wear and potential breakage of carbon rings, including higher water costs resulting from steam losses and degraded bearing performance because of oil contamination and higher operating temperatures. For operators looking to reduce steam leakage and increase equipment reliability, two primary alternatives to carbon rings are available on the market: mechanical seals and the floating brush seal.
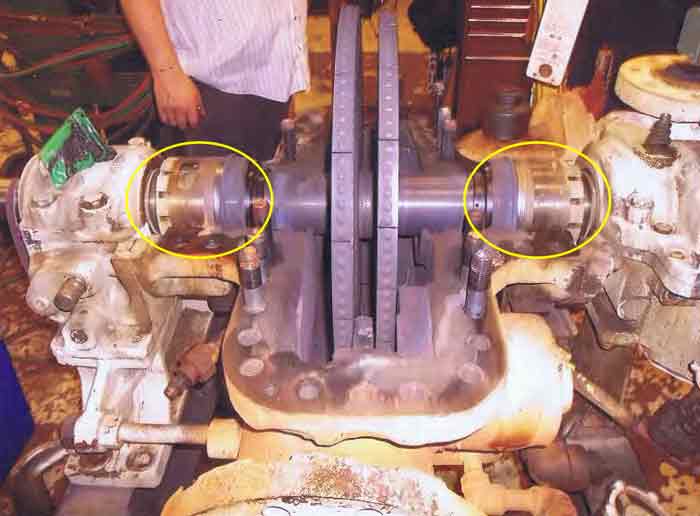
Mechanical Seals
Mechanical seals used in general-purpose steam turbines are a derivative of dry gas seals. A unique profile—spiral grooves—on one of the seal faces draws in steam, which creates a pressure dam that pushes the rotating and stationary seal faces slightly apart for a non-contacting, film-riding sealing interface. Resulting leakage is extremely low and measured in parts per million. With a design distinctly dissimilar to conventional carbon rings, the mechanical seal requires major modifications to a turbine’s existing gland box configuration. On steam turbines where the steam chest and gland boxes are individual components, the mechanical seal assembly can be bolted to either end of the steam chest in place of the carbon ring gland boxes. On turbines where the steam chest and gland boxes are one piece, major machining is required to fit the mechanical seals. In addition to gland box modifications, the turbine shaft may require modification to secure the seal’s rotating assembly. Final setting of the mechanical seal requires careful alignment with the rotor and casing to ensure proper sealing between the rotating and stationary seal faces.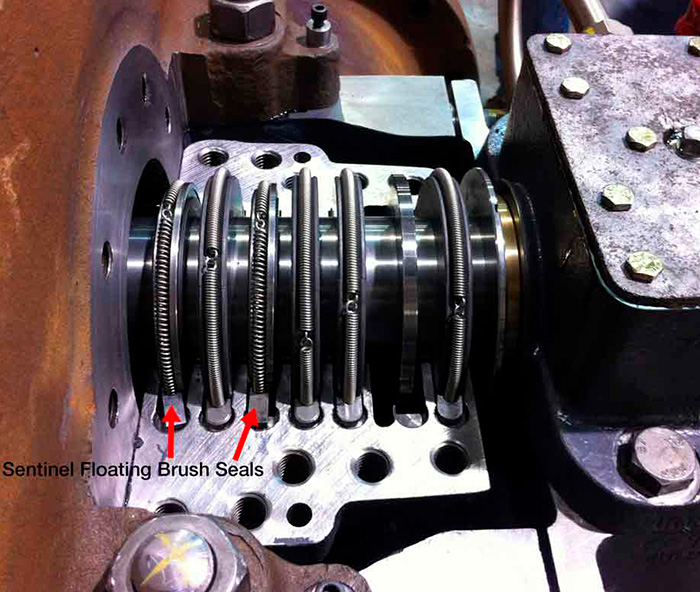
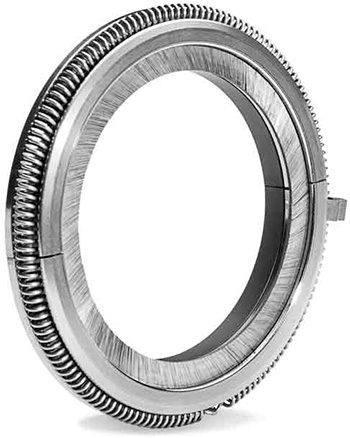
Floating Brush Seals
The second candidate for replacing carbon rings is a floating brush seal (FBS). An FBS combines a carbon seal with brush seal technology encased in a lightweight stainless steel band. This technology is designed to withstand condensate flashing while providing a lower, more stable leakage rate. As a floating seal, the FBS tends to be more tolerant of vibration, bearing failures and radial movement than other options. The brush seal acts as the primary shaft seal and faces the high-pressure steam. It provides immediate pressure reduction while its bristles filter out steam contaminants, protecting downstream carbon rings. The carbon ring of the FBS provides a face seal against the downstream gland wall or separator plate. Designed to fit the same space as a carbon ring, an FBS can be a drop-in replacement. The seal has a split design, with two segments held together by a garter spring. Its self-centering assembly may eliminate the need for an involved alignment procedure in some applications.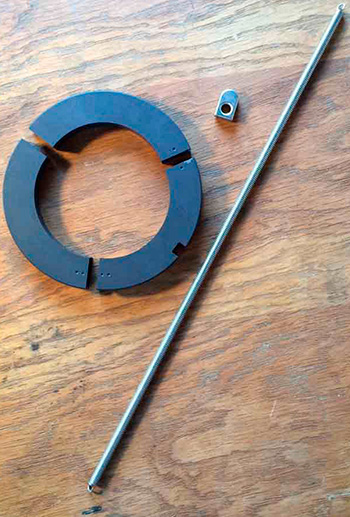