How to bring predictability to an otherwise unpredictable process.
Flowserve
01/31/2019
Oil refineries and petrochemical facility personnel are excited about the potential for industrial internet of things (IIoT) technologies. Specifically, these operations are interested in how IIoT can streamline equipment maintenance to the point where reliability engineers can detect and resolve equipment problems before they happen. This ability to “see what matters” requires equal parts instrumentation (to capture real-time equipment performance information) and monitoring (to determine what this data means). Operations that want to leverage IIoT to its fullest need to get both parts of this equation correct, as deficiencies in either will impact the ability to get a complete picture of the equipment’s performance.
Emerging Instrumentation Advancements
Capturing and transmitting equipment data are critical; without an accurate baseline, it is difficult to measure deviations in performance. Today’s instrumentation technology leverages advancements in signal conditioning, transmission and reception, wireless manufacturing and industrial environments. These technologies use open and secure architectures and include seamless interfaces so facility operators can expand instrumentation devices as needs evolve. Wireless instrumentation systems can capture and transmit a variety of equipment data. This includes, but is not limited to, temperature, pressure, flow, vibration, torque, thrust and others. The data can be transmitted wirelessly either by “single-point” sensors that are self‐powered or self‐transmitting devices that do not require a line of sight.Incorporating Wireless Technologies
Oil and gas companies often question how to integrate these technologies into existing infrastructure. Interfacing instrumentation technology may require only a serial port connection. Hard-wired connections for analog or digital signals can also be incorporated. Most systems are configurable to meet a facility’s specific requirements. If an existing hard-wired system requires additional data points, reliability engineers can connect more devices (via plug and play) into the host receiver.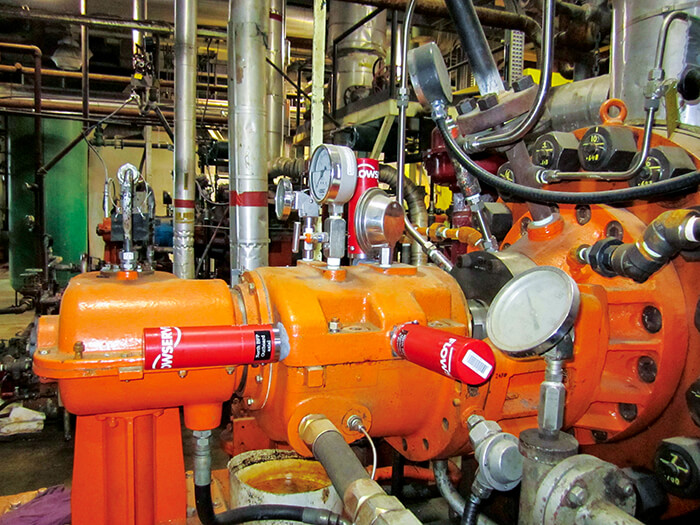