This technology can improve pump maintenance programs by lowering operating costs through extended mean time between repairs.
03/15/2016
Pumps are the primary drivers of any industrial plant's process flow system, providing process chemicals, slurry transport, cooling water and waste transport to the various parts of a facility. These pumps must operate reliably and efficiently to meet production goals and ensure safe operation. Pumps operate under fluctuating conditions including positive and negative pressures, elevated temperatures, corrosive solutions and abrasive slurry mixtures. The effects on the wet-end components of a pump's critical tolerances and the resulting impact on performance are numerous, and processes can impact these critical tolerances. For example:
- Insufficient discharge pressure can result in recirculation, leading to accelerated abrasive conditions if particulates are in suspension.
- Higher-than-expected temperatures can accelerate corrosive conditions of a medium, affecting a pump's metallurgical condition.
- Increasing amounts of solids in suspension can accelerate erosive wear of critical tolerances, reducing discharge pressures and increasing wear at suction spools, wear ring seats, cutwaters and volutes faces (see Image 1).
- Cavitation can impact impeller vanes, accelerating metal loss and weakening the vanes themselves (see Image 2) as well as damaging suction spools.
- Corrosion on pump wet-end internals from media changes or metallurgical deficiencies can lead to scale and corrosion deposits and/or pitting with resultant increased surface roughness that promotes pipe frictional forces and hydraulic drag (see Image 3).
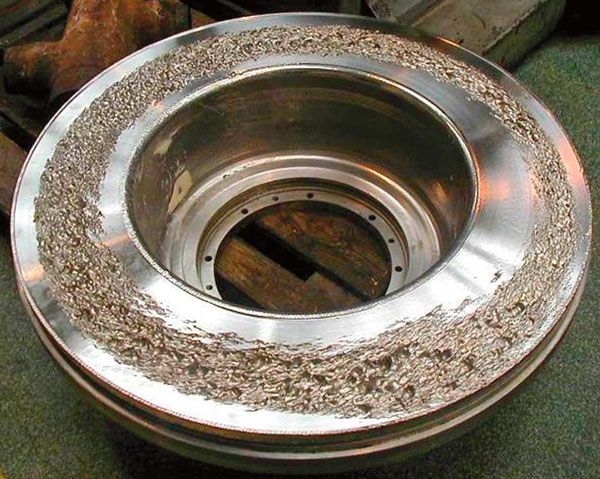
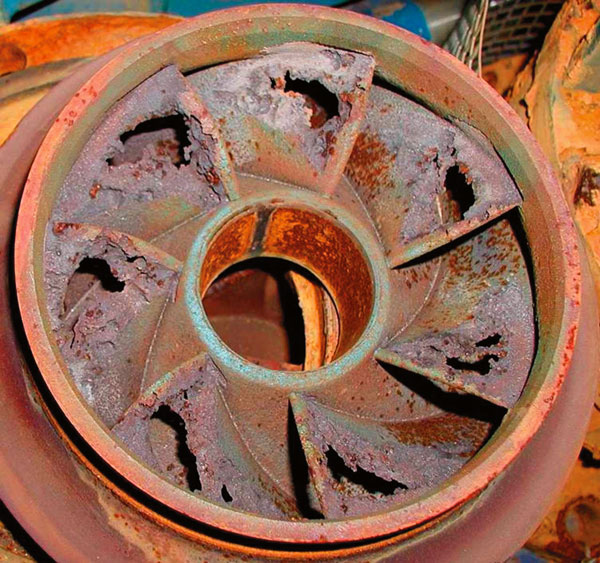
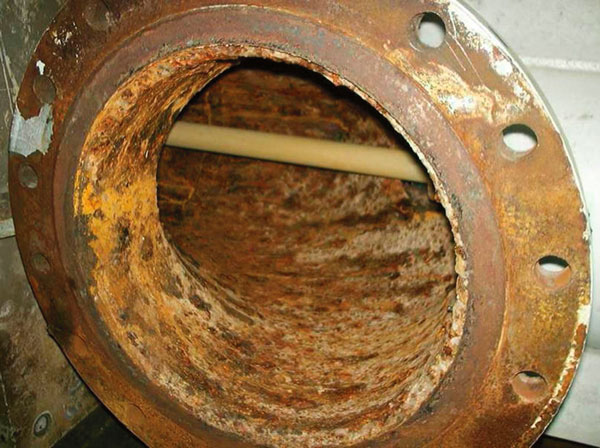
Solutions
The use of coatings to maintain a new pump as well as to improve an in-service centrifugal pump's performance and energy efficiency is not new. In 1948, A.J. Stepanoff discussed the use and benefits derived from porcelain enameling a pump's wet-end in his book Centrifugal and Axial Flow Pumps. If these coatings can resist the effect of corrosion/erosion, chemical attack and abrasion, the flow through the hydraulic passage becomes more efficient and the dimensional tolerances are able to be maintained for an extended period, resulting in longer life and more reliable operation of the pump. To determine how effectively a coating system can impact a pump's performance, one must first establish a performance reference point. This involves measuring flow and energy consumption over several duty points to establish a pump curve. Ultrasonic devices can accurately measure pump flow rates. Installing pressure gauges at suction and discharge establishes inlet and discharge pressures. By using amperage meters, one can measure the energy demand to the pump motor during flow. Once these steps are taken, the energy per unit flow (specific energy) can be established at a given discharge pressure. If the pump is impacted by corrosion involving scale buildup, reducing tolerances or increasing frictional drag, then a coating process can reduce corrosion scale buildup and frictional drag. If erosion or abrasion accelerated by corrosive chemical exposures has opened up critical tolerances in the wet end of the pump, a resurfacing grade coating that uses abrasion-resistant reinforcements such as aluminum oxide (Al2O3) or silicon carbide (SiC) may be applied to restore these tolerances to design specifications and provide extended wear resistance. There are specific considerations that need to be factored in to any coating material's selection such as adhesion of coating, resistance to chemical/corrosive attack, resistance to erosive/abrasive wear and resistance to operating thermal stresses. Any coating process also requires care in surface preparation to ensure the desired performance of the coating itself. This typically involves inspection and decontamination of the surface to remove impurities that impair adhesion, surface cleaning to remove scale and corrosion deposits, and grit blasting to increase the available surface area for maximization of the applied coatings adhesion. Application may require multiple steps to rebuild or smooth worn surfaces and to achieve the required total dry film thickness. These steps must be taken in a controlled environment and should only be undertaken by personnel experienced in the application of industrial maintenance coatings, who have been qualified by the manufacturer. Finally, inspection and re-assembly of the pump components must be done with care to ensure that tolerance fits and clearances are maintained.Case Study
In one example, a wastewater treatment plant where pump efficiency and reliability were a concern identified a pump for maintenance based on assessing losses in flow volume, reduced suction and discharge pressure, and amperage draw. After the pump was disassembled, areas of high wear and corrosion losses were noted (see Image 4).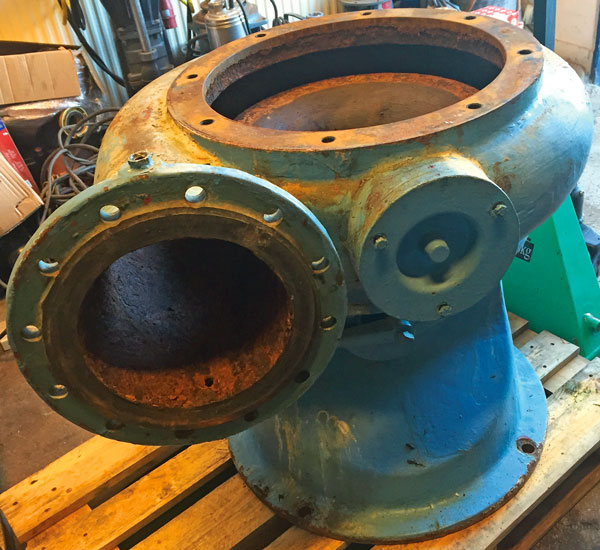
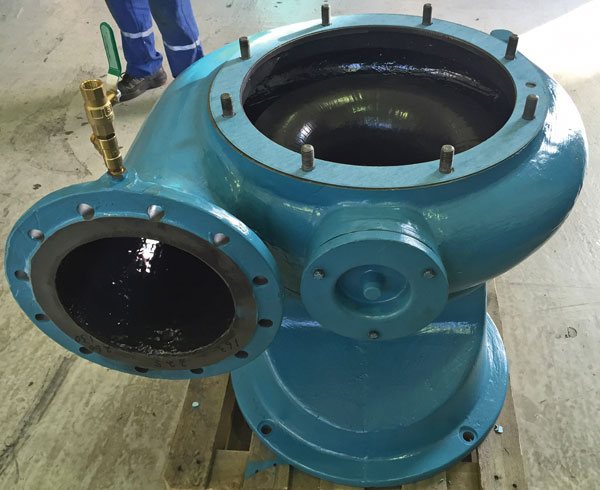
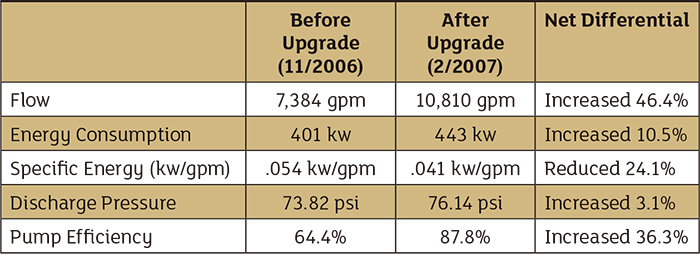