Making a correct braided pump packing selection can be a confusing and daunting task. Every manufacturer has its own engineering specifications and features that the user must consider when making these decisions. What criteria should the end users include when making this choice, and how can they get the maximum performance from their packing?
Product Selection
To make the best selection and have the best chance of extended performance, the first criterion is to choose packing made from a yarn that is capable of withstanding the highest shaft speed attainable for the application. Shaft speed capability for the packing is published in the manufacturer’s information as a tangential velocity (feet/minute or meters/second) at the sleeve diameter.
The next consideration is the pH range of the packing. Specifying a product with a 0 to 14 pH range is always best. This pH operating range ensures that no chemical attack of the packing yarn will occur. Remember, many braided packings can be exposed to acid or caustic cleaning process during their service life. Proper consideration of the pH range of the entire process is important to extend the products’ overall reliability.
Equipment Condition
When evaluating the rotating equipment’s condition to determine the style and type of braided packing required for the application, end users must weigh several variables. These include mechanical issues and an awareness that these may change during the service life of the equipment. The mechanical issue that is most scrutinized is sleeve wear, but the user must also consider the stuffing box, packing gland and lantern ring to ensure maximum service life of their braided packing.
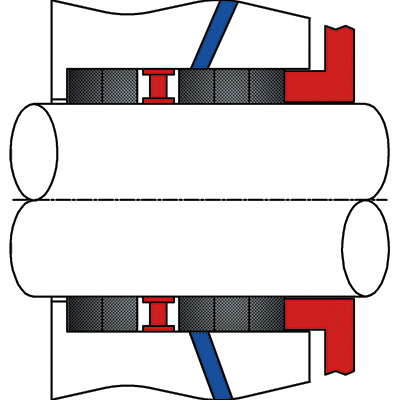
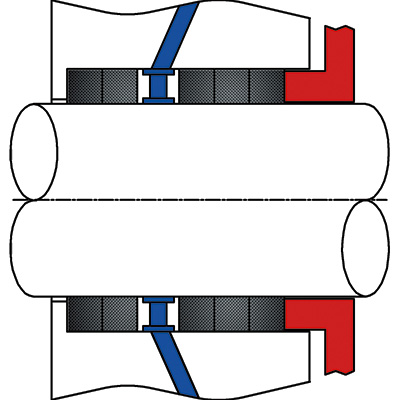
The condition of the stuffing box should be inspected, and the following questions should be asked:
- Is wear or corrosion present?
- What is the condition of the stuffing box throat or throat bushing?
- Has the stuffing box been bored during a rebuild?
- Is the stuffing box concentric with the shaft?
The packing gland’s and lantern ring’s conditions should be inspected, and the following questions should be asked:
- Does the packing gland and or lantern ring show signs of wear?
- Do they properly fit the stuffing box bore and packing sleeve?
As a general rule, if any of these deficiencies exist, properly seating and loading the set of packing will be impossible. These conditions will cause excessive pumped product and/or flush water leakage. In some cases, the end users can specify some type or style changes to assist with overcoming these equipment deficiencies, but in most cases braided packing will not remedy sealing issues with worn equipment in the long term.
Installation
Once the braided packing style or styles have been chosen based on the operating parameters of the application and the condition of the equipment to be serviced, the next consideration is proper installation. The assumption is that each packing ring has been cut and/or die formed to properly fit the shaft size and the cross section of the stuffing box, as determined by subtracting the shaft sleeve diameter from the stuffing box bore dimension and dividing the difference by two. If using an external flush, determining the proper location of the lantern (flush) ring in the set of packing prior to installation is useful (see Figures 1a and 1b).
Upon installation, each ring of packing must be lubricated with a water-soluble lubricant recommended by the packing manufacturer. Install and properly seat each ring squarely in the stuffing box. Each ring must be compressed not only to affect a proper seal and control external leakage but also to reduce product dilution.
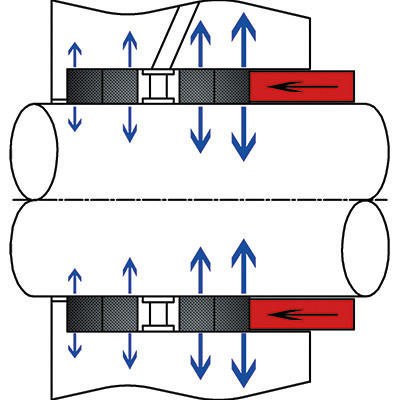
After installing and seating each ring individually, end users should tighten the packing gland finger tight and then one flat of the gland bolt or nut. During the break in the process while the equipment is operating, they should allow the packing to leak until it has experienced some thermal growth and then tighten the gland nuts, one flat at a time, until the leakage is controlled to 10 to 12 drops per minute per inch of shaft size.
Proper Flush Water Use
The proper use of flush water has become one of the most controversial subjects for braided packing users in recent history. Users tend to try to apply any new technology or ideas to eliminate water use. However, if one simple rule is applied—all slurry applications require the use of flush water—end users will see that the most complex solution is not always the most reliable. The primary factor in deciding if flush water is required is to determine if the media being pumped is clean, cool and non-abrasive.
If the pumped media meets these criteria, flushing is not needed. If the pumped media is abrasive, the proper application of flush water is required to maximize braided packing service life and performance. One common mistake made that results in increased water use and minimized performance is maintaining high flush water flow rates and not maintaining the flush pressure at 15 to 20 psi (1 to 1.4 bar) over the stuffing box pressure. Proper packing performance in slurry applications depends on maintained pressures—not flow rates.
Packing Flush Water Usage Rate
A common misconception is that packing uses excessively large volumes of water. Braided packing does, as a general rule, use more water than mechanical seals. However, in most abrasive and slurry applications, the packing and mechanical seals both require the use of a flush or barrier fluid to protect the sealing surfaces. The standard recommended external leak rate for braided packing in rotating equipment is 10 to 12 drops per minute per inch of shaft size. Based on this leak rate, what is the accumulated annual leakage for a 3-inch (75-millimeter) shaft? According to the U.S. Geological Society Water Science School’s leak rate calculator, this drip rate equates to 1,100 gallons of external leakage and roughly 500 gallons of product dilution annually if the packing rings are installed and seated correctly. This is a total of 1,600 gallons annually.
The next common question regarding flush water use is cost. After extensive surveys of facilities in the U.S., a general consensus is that water cost is approximately $0.45 per 1,000 gallons ($0.12 per cubic meter). Not only will reliability be greatly increased by the use of flush water in abrasive and slurry applications, but the water cost is relatively insignificant.
Summary
What is the secret to reliable packing life in rotating equipment? How do end users economically seal their stuffing boxes without breaking their budgets? No shortcuts are available to reliable packing performance. However, if users follow some basic guidelines, reliability and longer life can be expected. These guidelines are:
- The correct specifications for the braided packing must be chosen with an emphasis on the chemical and thermal properties of the yarns.
- The user must establish some basic installation and equipment maintenance/ inspection guidelines with operational care practices.
- End users should partner with a pump manufacturer and a local fluid sealing representative that understands their equipment service requirements to aid in simplifying the selection process and training employees on installation and basic care procedures.
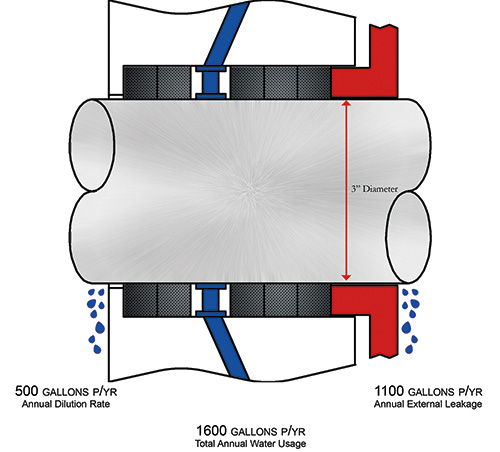
What results can the user expect for a properly managed packing program? As a general rule, history has shown that achieving an average packing life of up to three years is possible.
The following members of the Compression Packing division sponsored this “Sealing Sense”:
American Braiding & Mfg. ChemStar Mechanical Packing, Inc. A. W. Chesterton Co. Daikin America, Inc. EGC Enterprises, Inc. Empak Spirotallic Mexicana SA de CV GFL Americas – Gujarat Fluorochemicals W.L. Gore & Associates, Inc. GrafTech International Holdings, Inc. John Crane Lenzing Plastics GmbH New England Braiding Co., Inc. Nippon Pillar Corporation of America Palmetto, Inc. SEPCO - Sealing Equipment Products Co. SGL Technic Polycarbon Division Slade, Inc. Teadit International Teijin Aramid USA, Inc. YMT/Inertech, Inc.