Elastomeric polymer materials provide mechanical strength and self-lubricating properties required in challenging settings.
Thordon Bearings Inc.
11/06/2018
When faced with the harsh conditions found in mining, users often expect some wear and tear on seals. But one machine shop found a way to extend the life of seals for pneumatic air cylinders used on unloading mining dump wagons.
Case Study
RMH Industries in Quebec, Canada, is a machine shop that specializes in chrome plating, metallization and hydraulic repairs for heavy equipment such as crushers, gear boxes, telescopic hydraulic cylinders, hydroelectric main guide bearings, head covers and servomotors. The shop recently replaced rubber seals on 28 pneumatic cylinders with seals made of an elastomeric polymer material.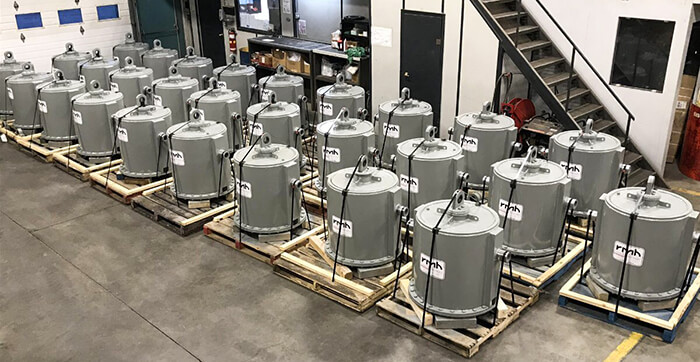
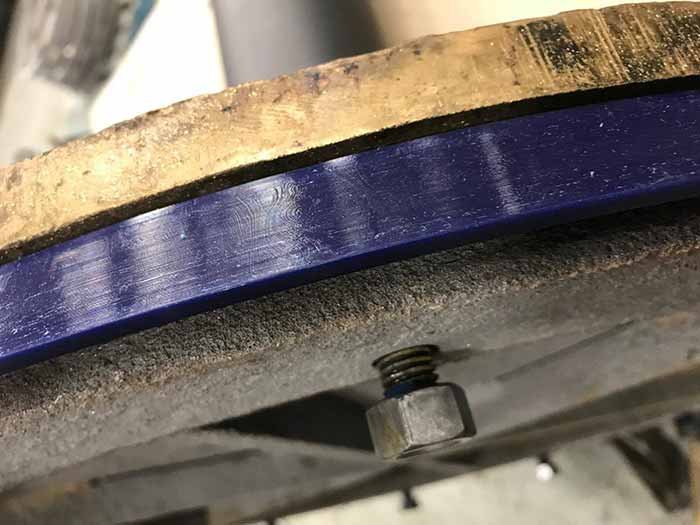