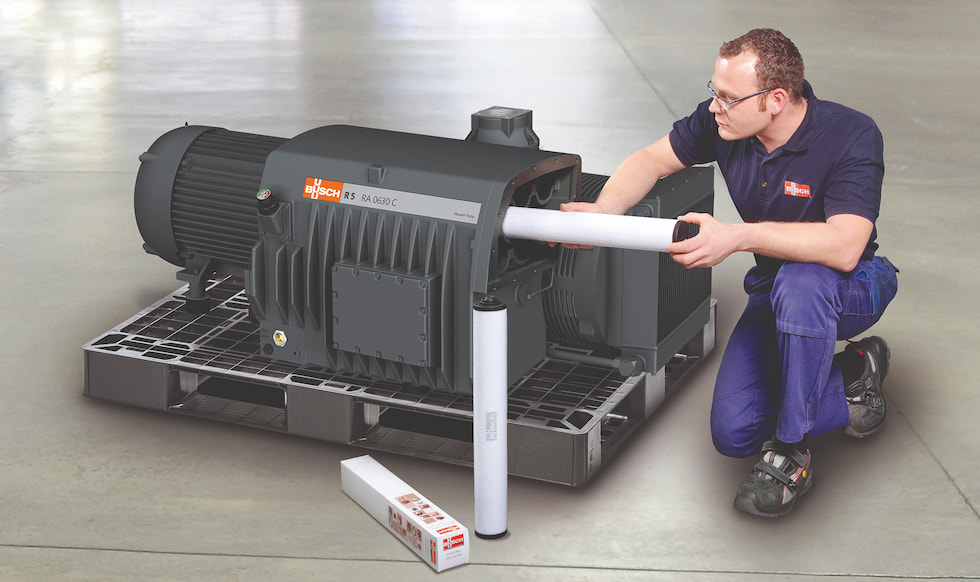
Oil-lubricated rotary vane vacuum pumps are vacuum generators frequently used in food packaging, health care, woodworking and chemical applications. An internal oil circuit allows for high operational reliability, high vacuum levels (0.1 mbar = 99.99%), high water vapor tolerance and a self-cleaning effect (Image 1). These advantages are counterbalanced by the need for regular servicing and a limited speed control range.
Operating Principle
The oil-lubricated rotary vacuum pump works on the rotary vane principle (Image 2). The oil seals the gaps, lubricates the vanes and removes the heat of compression. When an oil-lubricated rotary vane vacuum pump is operational, air is being pulled through the inlet into a cylindrical housing. Inside the cylinder, a rotor with several vanes is mounted eccentrically. Due to centrifugal force, these vanes slide in and out of the rotor, creating chambers between themselves and the housing. Air is trapped inside these chambers, and as they rotate, their volume is constantly reduced.
This compresses the air and transports it to the exhaust box, where it then goes through one or more exhaust filters. These filters act as a coalescer (separating vapors, soluble particles or oil) but allow air to flow through the media from inside to outside the filter element. Any air that flows through the exhaust filter will eventually be displaced out the exhaust port area. Oil and water droplets collect on the filter fibers. As they become heavier, gravity forces them to drop down to the bottom of the exhaust box. The oil helps seal gaps, reduces heat and lubricates the vanes. This oil is then recirculated back through the oil return line and the process starts over.
Changing the oil and exhaust filters on a routine basis are essential and can be done following the manufacturer’s instruction or by a service technician. The filters can only be efficient and effective when proper maintenance is completed.
Internal Component Maintenance
Maintenance intervals depend on the individual operating conditions and should be shortened or extended as appropriate. Particularly harsh applications or heavy-duty operations, such as high dust loads in the environment or in the process gas, other contamination or ingress of process material, can make it necessary to shorten the maintenance intervals. The vacuum pump’s internal components contribute to the pump’s reliability and need to be well maintained to ensure energy efficiency and prevention of downtime.
One key component is the vacuum pump’s exhaust filter. Changing the exhaust filter ensures the optimum performance of the vacuum pump. It is important to use an exhaust filter with an ultra-fine medium and a tight mesh for better filtration performance.
More oil is retained, and therefore less oil needs to be refilled. Oil emissions in the ambient air are reduced to an absolute minimum using a quality exhaust filter. Check with the manufacturer to ensure their filters comply with emissions standards. At the same time, the energy consumption is lower thanks to minimized flow resistance. An electrically conductive design prevents the risk of ignition through electrostatic discharge and ensures safe operation.
When is it time to change the exhaust filter? First, measure the filter pressure. If it exceeds 0.6 bar and the needle is in the red zone, filters must be changed. Also, if smoke is coming out of the exhaust, it is time for a filter change. With normal one-shift operation, filters should be changed at least annually. It is best to use the manufacturer’s genuine exhaust filters, filter fleece and O-ring to complete the maintenance work.
Another set of critical internal components are the vacuum pump’s rotary vanes. Compared to vanes manufactured from other materials, vanes made from carbon composite material increases reliability and operational performance of the vacuum pump. When used in applications that produce condensates, vanes manufactured from aluminum or unbound glass fiber compounds often result in cylinder damage (i.e., wash-boarding).
Oil
The role of oil in an oil-lubricated rotary vane vacuum pump is twofold: a smooth rotation cycle, allowing the vanes to slide freely, and an efficient sealing of the compression chamber.
During operation, the vacuum pump’s oil is exposed to various sources of contamination (chemicals, acids, dusts, aerosols) depending on the application. This may cause the oil to lose viscosity over time along with some of its beneficial characteristics.
Running a vacuum pump with degraded inferior oil reduces the vacuum pump’s performance and shortens its life cycle. A regular oil change and the use of high-quality oils ensure the vacuum pump is performing at its optimum and continues to meet process requirements.
Many OEM’s original oils and lubricants for vacuum pumps and blowers have been developed and tested specifically for vacuum applications. These oils require a balance of heat stability, condensable vapor tolerance and viscosity-temperature performance to ensure safe and reliable operation. Operating a vacuum pump with an incorrect lubricant, even with an equivalent oil, may void the warranty in the event of damage.
When Is it Time to Change the Oil?
- according to the manufacturer’s scheduled recommendation
- when the vacuum pump is running too hot
- when there is oil discoloration, either darkening for hydrocarbon oils (from heat or other contaminants), or it is a creamy color (typically water vapor contamination)
- when there is degradation of the vacuum pump’s performance and ultimate pressure
A sophisticated and perfectly balanced oil formula is the secret to maintaining the initial viscosity and lubrication properties for as long as possible. Even dry vacuum pumps, blowers and compressors need oil for their gear boxes to prevent premature wear and to ensure smooth operation with low noise and vibration levels.
It is important to not only change the oil, but also the oil filters. Again, using the OEM’s genuine oil filters provides the best results. They have been specifically developed to perfectly match the intended pump.
Some operators may choose to change the oil and oil filter on their own instead of having a service technician change the oil. Here are five basic tips:
- Use an oil drain valve kit (Image 3).
- Do not leave oil inside the pump after draining. The oil drain valve kit will help with this step.
- Lubricate the oil filter gasket before its first use.
- After refilling the oil, run the pump for one or two minutes, then turn the pump off.
- Check and adjust the oil level once again.
Using an outside service technician can save time and has other benefits. A service call should include a pressure and leak check, vane check, a test run to factory standards and assurance that the equipment is running efficiently.
Calculating Total Costs
When purchasing vacuum technology, compare the investment and energy costs of different vacuum technologies along with different manufacturers. Look at the anticipated total costs over an extended period. Energy costs and operating costs can also vary greatly. It is important to consider maintenance work and the resulting downtime, costs for spare parts and the procurement and disposal of operating fluids.
Checking Availability of Service & Spare Parts
Process reliability normally depends directly on the operational safety of the vacuum pump or vacuum system. Therefore, it is important to pick a trustworthy provider who can offer swift, reliable services on-premise and deliver spare parts without delay.
Looking to the Future: Industry 4.0
Today’s vacuum pumps allow for maintenance with access to all service relevant parts. Many OEMs offer contractual services at a fixed rate and take responsibility for the operational safety of its vacuum pumps and vacuum systems. The operator is, thus, protected and does not need to have its own team of service technicians. Vacuum pumps are now available that feature intelligent sensors to inform the operator or service technician about pending maintenance work in real time. Also, retrofit kits are available to make existing vacuum pumps ready for Industry 4.0.