HI Pump FAQs
Hydraulic Institute
02/22/2017
What are key factors in selecting either a rotodynamic or positive displacement (PD) pump for a system?
Rotodynamic and PD pump technologies are different in method of pressure development as well as operational characteristics. Simply stated, a rotodynamic pump uses a rotating impeller to increase velocity of a liquid and its stationary components’ direct discharge flow to convert velocity to increased pressure. A PD pump moves a set volume of liquid, and pressure is obtained as the liquid is forced through the discharge into the system. Rotodynamic pumps are most broadly applied because they ideally handle the world’s most abundant liquids and serve a board range of flow rates. They are typically used on water and thin liquids at low to moderate pressures, while PD pumps are used across a wide range of viscosities and pressures. At constant speed, rotodynamic pumps deliver a variable volume of liquid while PD pumps deliver a constant volume. Table 1 shows a benefits and limitations comparison chart for rotodynamic pumps and a specific PD pump type (rotary).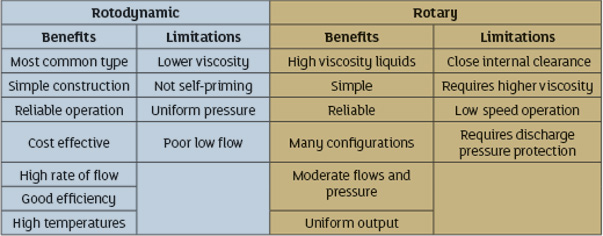
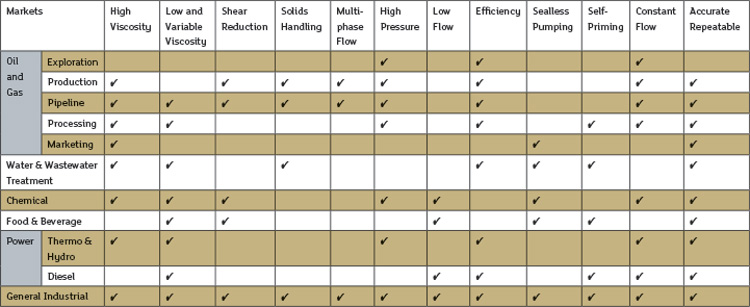
What implementations have been sought in the pumping system industry to accommodate for energy savings demand?
In today’s global economy, environmental concerns such as climate change and an industry’s carbon footprint are at the forefront of many industrial business models. The U.S. Environmental Protection Agency (EPA) and the U.S. Department of Energy (DOE) have recently implemented regulations that focus on energy efficiency. According to the DOE 2014-05 Technical Support Document for Electric Motors (Final Rule), nearly 70 percent of industrial electricity demand is used by industrial motor systems, with a majority of these being rotodynamic pumping systems. DOE regulations for the electrical motor industry and pumping industry strongly indicate that increased energy efficiency will have a major impact on our economic growth for the foreseeable future. The Energy Conservation Standard for Pumps (10 CFR 431 Subpart Y) published in January 2016 recognizes that pumps and motors equipped with variable speed drives can save significant energy and the DOE metrics for the regulation measures these savings. When properly applied, variable frequency drives (VFDs) play a major role in energy conservation by reducing the electricity demand and increasing the life of pumping systems. A VFD is an electronic device used primarily for controlling the rotational speed of an alternating-current (AC) electric motor by controlling the frequency of the electrical power supplied to the motor. VFDs have been used to control the speed of electric motors for more than 40 years. However, many pump end users were initially slow to adopt this technology. In recent years, innovative steps have been taken to improve the efficiency and reliability and reduce the cost of VFDs, making them a more attractive solution to motor speed control. These innovations have been met with a rapid adoption of VFD systems across the pumping industry. As with any rapid technological surge, there is a steep associated learning curve. VFDs have a special set of requirements that must be considered during system and application selection, installation, operation and troubleshooting. It is difficult to find objective literature that has information directed toward these special requirements with an emphasis on the pumping industry. Throughout the years, various white papers regarding VFDs have been circulated through the pump industry. As a result, HI developed a comprehensive guidebook that combined these considerations with recommendations from industry experts. Variable Frequency Drives: Guidelines for Application, Installation, and Troubleshooting assists VFD end users and system integrators in the proper selection, specification, installation and operation of VFD-driven equipment. This guide details basic troubleshooting information to help diagnose common issues with VFD-driven systems. The goal of this guidebook is to educate the pumping industry and to ensure the safe, reliable and efficient operation of the pumping equipment we all depend on every day. HI guidebooks are written by industry experts on topics vital to those who design, operate, or maintain pumps and pumping systems. For a full list of guidebooks, visit estore.pumps.org/Guidebooks.aspx.
See other HI Pump FAQs articles here.