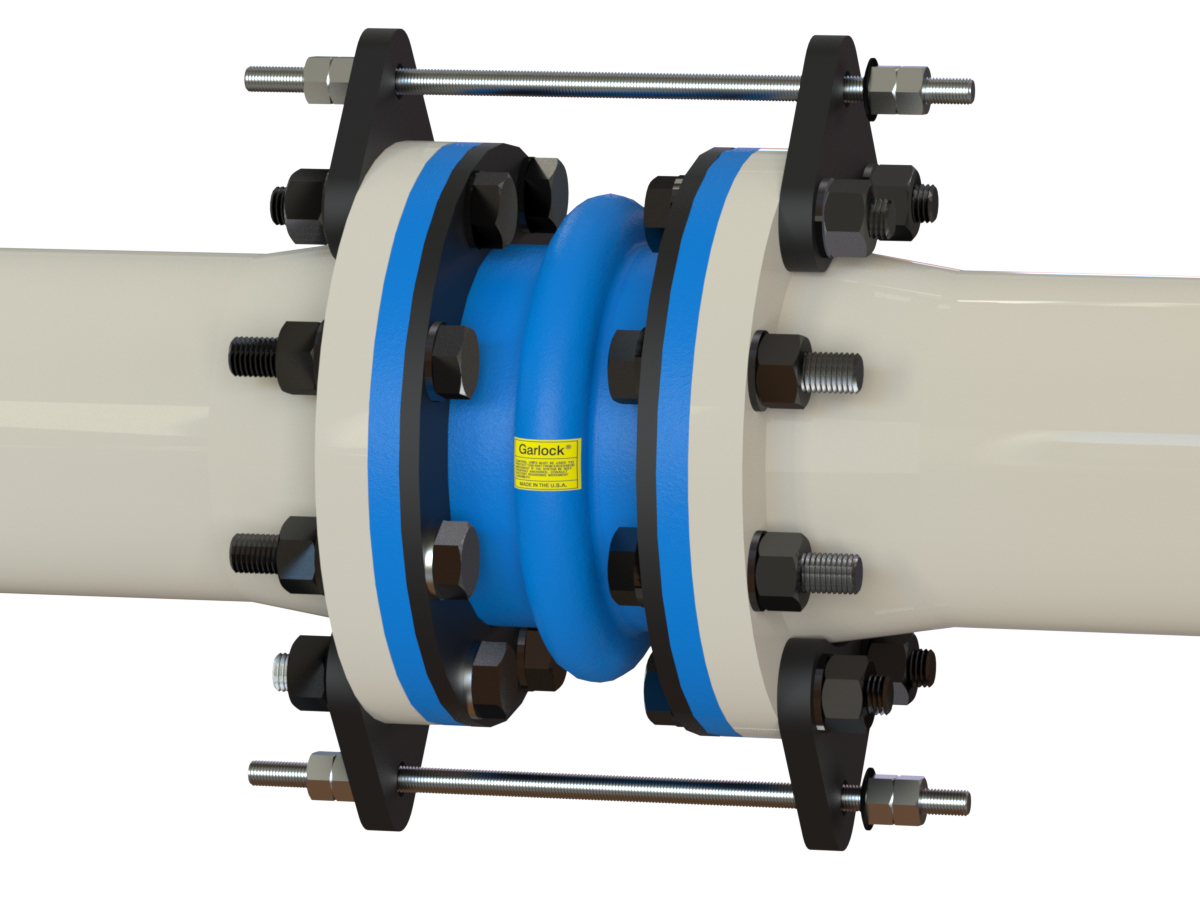
Flue gas desulfurization (FGD) is an efficient process commonly used in coal-fired power stations to remove sulfur dioxide, an environmentally harmful byproduct of burning coal, from flue gas. Because of component operational stresses and unplanned outage concerns, FGD system maintenance can be challenging. Due to the operational cycle length expected in coal-fired plants, regularly scheduled maintenance coupled with optimal component selection is essential to minimizing downtime.
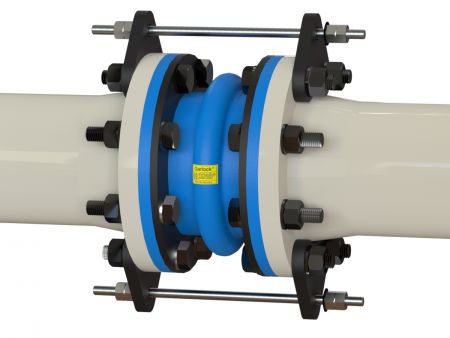
Various types of FGD systems are in operation, with the most common being wet and dry types that use a lime or limestone slurry reagent. Pumping harsh slurry mixtures in a constant recycle loop imposes unrelenting wear on the piping components, creating the potential for unexpected failures. Expansion joints can be used to absorb the movement and vibration in piping systems, thereby preventing leaks or more serious damage.
Expansion joints are critical to the limestone slurry recirculating pumps in the gas desulfurization scrubber system. Identifying the correct expansion joints to use is not an easy task considering the vast number of products in the market and their varied uses. However, diligent product selection in lieu of a quick and easy replacement could mean the difference between uninterrupted operation and unplanned downtime.
Expansion Joint Styles
The first step in product selection is determining whether a metallic or nonmetallic expansion joint is best suited to the application. Metal expansion joint construction consists of thin-gauge steel configured into multiple bellows or convolutions. This configuration is best suited to high-temperature, high-pressure applications. Because component life is defined by a set number of cycles, metal fatigue can play a troubling role in the service life of metal expansion joints. Fatiguing the metal long enough to fulfill its cycle count will likely result in an abrupt failure.
By contrast, rubber expansion joints (Image 1) are constructed from layers of natural or synthetic rubber and fabric. This composite is resistant to abrupt cycle fatigue failures; instead, it deteriorates slowly over time. Rubber decay is gradual depending on the temperature and environment, but visual cues indicative of potential problems will typically present themselves long before a failure occurs. Other advantages of rubber expansion joints are noise/vibration dampening, greater pipe movement and improved abrasion resistance.
Because of the highly abrasive nature of the limestone slurries employed in FGD systems, most expansion joints are made of rubber. Solid particulates from the slurry can get trapped in the corrugations of a metal joint, mechanically restricting it as it attempts to absorb pipe movement. To avoid this, a rubber expansion joint can be configured with a filled arch to present a smooth bore (Image 2). Because the arch is filled with a flexible rubber compound, the overall design remains flexible enough to absorb the thermal expansion/contraction in the piping while also allowing the slurry to flow without interruption over the smooth bore.
Materials
In FGD systems, the two most important factors when selecting expansion joint materials are abrasion and temperature resistance. Natural rubber is the material most commonly selected for abrasion resistance, but the performance of the elastomer itself can vary from one manufacturer to another depending on the elastomer blend used. Taking advantage of standardized testing to measure abrasion resistance of the elastomer is a pragmatic approach to maximize service life through material selection.
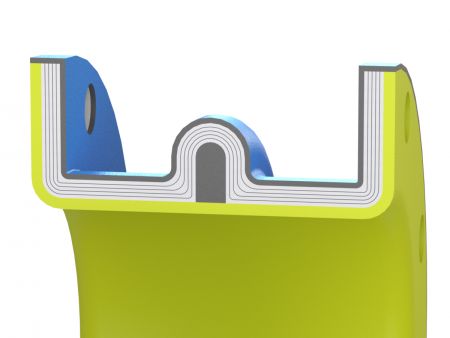
Making an informed decision on materials can be accomplished by requesting test data from the expansion joint manufacturer. The American Society for Testing and Materials (ASTM) D2228 Pico Abrasion Index is an industry-standard test that quantifies the wear resistance of elastomers when subjected to a force by a sharp blade. Another popular test is the European standard DIN 53516 method which abrades the rubber specimen by constant contact with a rotating drum of coarse sandpaper. Higher percentages of material wearing away during the test indicates poorer performance of the elastomer.
Results from these tests can translate into longer life expectancy and improved overall system reliability.
For example, millable polyurethane (Image 2) is a new material used in expansion joints that provides wear resistance properties in applications with high solids content, such as limestone slurries. Polyurethane scores two to three times higher in resistance to abrasion compared to natural rubber on the Pico Abrasion Index.
The second critical factor to consider is the temperature resistance of the materials used in the expansion joint. Air aging tests are an accepted methodology in the rubber industry, which consists of subjecting the elastomer to an elevated temperature for a specified time. Heat resistance is gauged by the change in physical properties such as hardness, tensile strength and elongation percentage. Large variances from nominal are indicative of poor heat resistance.
While manufacturers set temperature ratings based on the results of these heat-aging tests, there is a lack of continuity in the allowable decline of the referenced physical properties. Two distinct natural rubber blends could share the same temperature rating, but the rate of physical decay could be different depending on how the two compounds are cured, the grade of the polymer or other formulation variances.
These variables are why it is important to request heat resistance test data from expansion joint providers. This ensures a like-for-like comparison of materials. The Fluid Sealing Association (FSA) provides industry standards for sealing products, including expansion joints, which can be referenced for elastomer specific heat resistance test parameters.
Intermittent temperature spikes can unknowingly play a significant role in the deterioration of expansion joints. For example, it is inadvisable to use natural rubber in an application when temperatures above 180 F are known to occur. It is common in FGD systems to source ethylene propylene diene monomer (EPDM) as an alternative because EPDM is generally rated up to 300 F. However, using EPDM as a liner material to withstand higher temperatures comes at the cost of the rubber’s overall abrasion resistance.
Hydrogenated nitrile butadiene rubber (HNBR) is an optimal liner material for wear resistance at elevated temperatures. Like EPDM, the recommended service temperature is typically up to 300 F, but HNBR has roughly 50 percent greater resistance to abrasion, according to the DIN 53516 test method.
Flow Liners
Abrasive flow in piping is often accompanied by substantial flow velocity, particularly in the small diameter piping seen in absorber bleed pump systems. A flow liner can be used to reduce turbulence and eliminate concentrated wear point areas of the expansion joint lining. In general, contact between the rubber itself and abrasive media is limited without sacrificing the range of movement the expansion joint provides. Protecting the rubber lining is critical because, if compromised, the expansion joint will fail in just a matter of time.
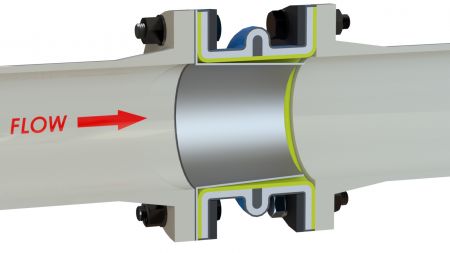
Flow direction is the only consideration required for use of a flow liner. Flow must be traveling into the leading edge of the flow liner (Image 3), otherwise solid particulates in the slurry mixture will collect behind the flow liner impacting the movement capabilities of the expansion joint over time.
The use of flow liners in vertical pipe runs requires flow direction to follow natural gravity. In most FGD systems, the recycle pumps for slurry recovery discharge vertically up the scrubber wall to the spray nozzles. With the flow opposing gravity, once the system turns off, any remaining slurry will fall and build up behind the flow liner. It is more effective to use the flow liner in horizontal piping, such as the suction side of the recycle pump or absorber bleed pump discharge lines.
Preventative Maintenance & Reliability Services
Reliability engineers have the important responsibility of accounting for every system component, no matter how small, to ensure the station maintains uninterrupted operation. It is unrealistic, however, to expect reliability engineers, maintenance crew/contractors or other component buyers to be experts on every part in the system. Preventative maintenance and reliability (PMR) partnerships between the plant and an expansion joint manufacturer can lift some of that burden from plant personnel.
Permanent distortion of piping resulting from years of thermal movement, foundation settlement or installation of rebuilt pumps can all result in misalignment issues. If there is excessive misalignment between a pump and related piping, a custom-sized expansion joint can be used to bridge the deformed gap. Failure of expansion joints in highly abrasive applications are exacerbated by unnecessary stresses caused by twisting, bending and stretching an expansion joint to fit a malformed pipe gap. Not only will the expansion joint be under stress at startup, but there will be resultant loads on the pump casing as well.
One solution is to ask the expansion joint manufacturer to measure and document the piping misalignment and recommend a custom-crafted expansion joint to fit the gap. These services also include recommendations on existing part conditions, so components can be replaced at the optimal time. Using manufacturers’ PMR services can help remove some of the guesswork from selecting the correct expansion joint, as well as help ensure maximum service life.
The life cycle duration of expansion joints in highly abrasive piping applications can be extended through careful product selection. Styles, materials, flow liners and manufacturer services are key areas of consideration when implementing expansion joints into FGD systems.