Vertical turbine and horizontal split pumps control pressure, overcome height obstacles.
Xylem Inc.
05/15/2018
The $1.35 billion Wilshire Grand Center opened in 2017 to international acclaim for its sophistication and luxury, a skyline-changing icon of modern design and a catalyst for the economic renaissance of downtown Los Angeles. Built entirely in the footprint of the former 1950s-era Wilshire Grand hotel—itself a cultural icon—the 73-story glass and steel skyscraper with its distinctive rooftop spire is the tallest building west of Chicago.
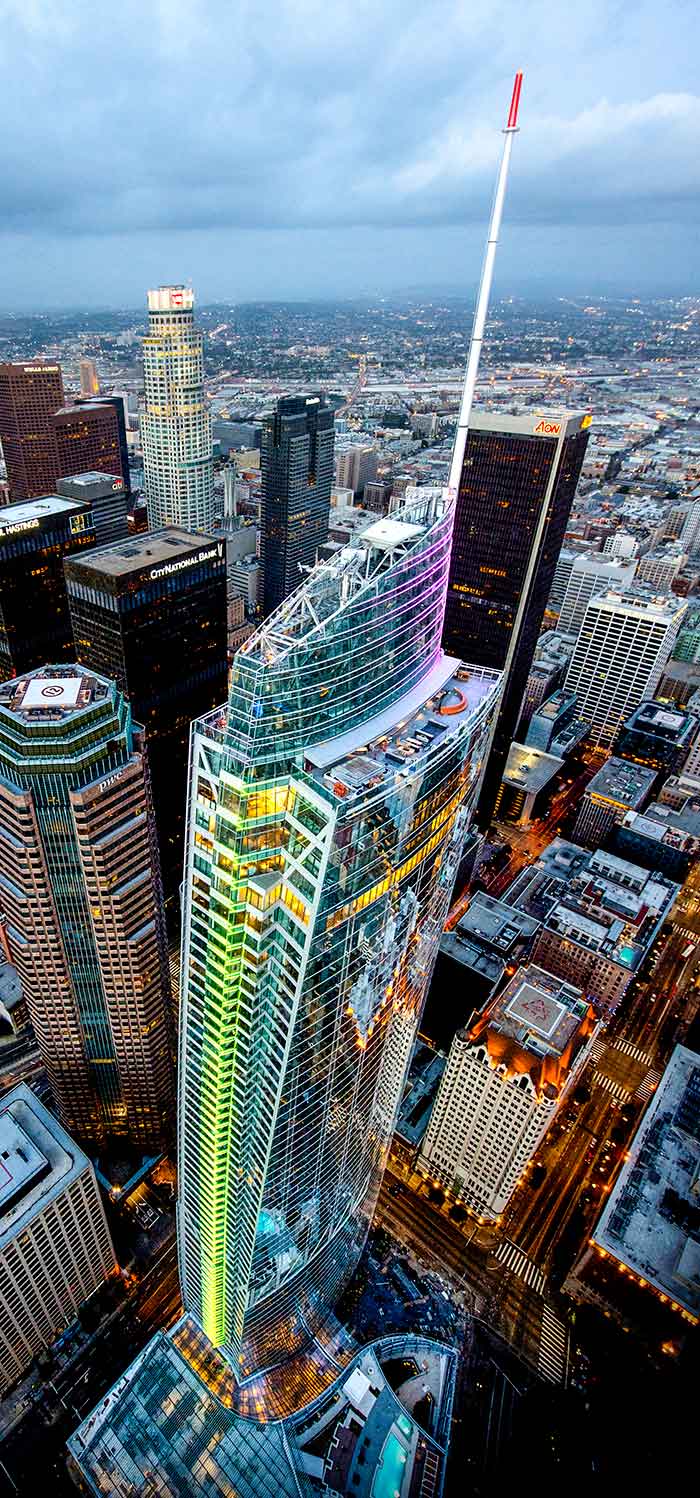