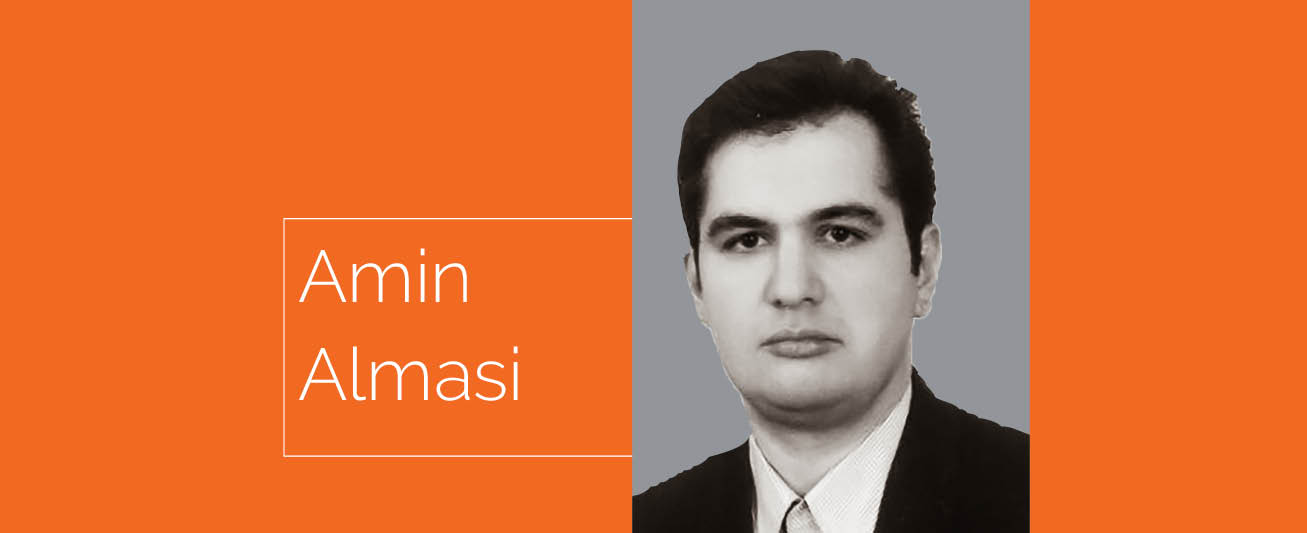
Fire Water Pump Considerations
A centrifugal pump suitable for fire water applications should have a relatively flat performance curve. Such a pump is sized for the greatest single demand for a vast fire in the plant. This usually translates to a large-scale fire in the largest unit of the plant. This is defined by the rated capacity and rated head of the pump set. In addition, a fire water pump should demonstrate the capability of flow rate larger than 150% of its rated capacity with more than 65% of its rated head (discharge pressure). In practice, selected fire water pumps exceed aforementioned values. There have been many properly selected fire water pumps with relatively flat curves which could provide more than 180% (or even 200%) of the rated capacity at the head and more than 70% of the total rated head.
Two to four fire water tanks should be provided where the primary supply source of fire water is located. A similar rule is applicable for pumps. Two to four fire water pumps should be provided. A common arrangement is:
- two electrical motor-driven fire water pumps (one operating and one standby)
- two diesel engine driven fire water pumps (one operating and one standby)
One challenge is that fire water pumps may not operate for a long time. However, during a fire, each should be immediately started and continue operation until the fire is extinguished. Therefore, certain provisions are needed, and each pump should be tested periodically to ensure a fast start and reliable operation.
Horizontal Pumps vs. Vertical Pumps
Horizontal centrifugal pumps are many operators’ preferred type of fire water pump. One reason for this is the relatively high vibration and the potentially vulnerable mechanical structure of large vertical pumps. However, vertical pumps, particularly vertical-shaft turbine-type pumps, are sometimes used as fire water pumps. In instances where the water supply is located below the discharge flange centerline, and the pressure is insufficient for getting the water to the fire water pump, a vertical-shaft turbine-type pump set might be used. This is specifically applicable when water from lakes, ponds, wells, or the ocean would be used as fire water (as the main source or as the backup).
For vertical pumps, the submergence of the pump bowls is the ideal configuration for reliable operation of the fire water pump. The suction side of the vertical pump should be positioned deep in the water, and the submergence of the second impeller from the bottom of the pump bowl should be more than 3 meters when the pump is operated at its maximum possible flow rate. Obviously, this is an idealized configuration, and final details and submergence should be defined case by case, after consultations with the pump manufacturer, local fire authorities and other stakeholders.
There have been several cases of high vibrations in large vertical fire water pumps. Therefore, careful dynamic studies and verifications are necessary. This should be done for all aspects of dynamic behaviors.
Piping of Fire Water Systems
Generally, the suction piping should be arranged and configured to minimize the likelihood of turbulent water flow entering the pump. Improper suction piping and turbulence at suction decrease overall performance and can increase risk of cavitation or even failure. Equipment that would stop or restrict the suction flow should not be installed at the suction piping. The piping size is influenced by many factors, such as net positive suction head (NPSH) requirements, velocity limits (sometimes 1.2 meters per second [m/sec], 1.5 m/sec or 1.7 m/sec) and code specific terms and conditions. The smaller the piping, the faster the water flow. Therefore, increased turbulent flow and pressure drop will occur. Increasing the pipe size lowers the flow velocity and pressure drop and reduces turbulence. Suction piping should be roughly one or two sizes larger than the suction nozzle/flange. Hydraulic and NPSH calculations should be used to verify sizing and details.
NPSH-margin (NPSH available minus NPSH required) should be carefully checked for all possible operating situations. NPSH-margin for the end-of-curve (approximately more than 150% of rated flow) should also be checked, as this is usually the most critical case. An NPSH-margin of more than 1.5 meters is preferred for the entire curve.
There are less restrictions and concerns regarding discharge piping. There is usually enough pressure available and less concern for pressure drops. Small turbulences or flow imbalances may not cause a concern in the discharge, and typically, discharge piping is smaller in size than suction piping.
An isolation valve should be installed so that the fire water pump can be isolated for testing, service and repairs. A check valve should also be installed on the discharge piping between the pump and the discharge valve. The pressure rating of discharge components should be adequate for the maximum total discharge pressure with the pump operating at shut-off conditions at the rated/maximum speed. Bypass to the suction tank is nearly always needed. This should be located at a point far from the pump suction to avoid turbulence.