At its location in the UAE, Dredge Yard engineers develops and supplies dredging and mining equipment such as dredge pumps, ball joints, cutter heads and complete dredgers. The dredge pump is a dredger's main component and is critical to achieving production. Dredge pumps also consume the most power during operation, so efforts to reduce the pump's power needs through smarter design are critical. Dredge pumps involve more complex engineering challenges than water pumps. They must carry water filled with a diverse, dense mixture of solids, including mud, fine sand, coarse sand, gravel, stones and other debris. The pumped water does not behave like a homogenous fluid because of the different viscosities. The soil tends to settle down and slide on the pipe bed, depending on the flow speed. Another challenge is that pump parts wear quickly. Clogged impellers and breaking vanes also pose risks to pump performance. Equipment replacement can eat away at operational efficiency and increase the dredger's overall lifetime costs.
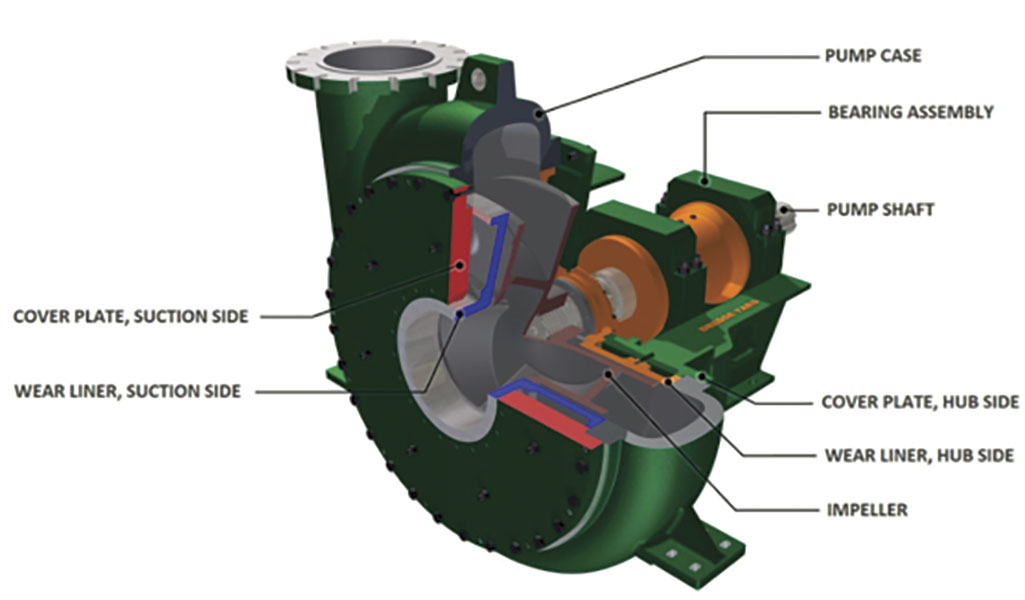

Designing the Industry's Largest Pumps
In 2012, Dredge Yard began developing new dredge pumps ranging from 200 to 1,400 millimeters (mm)— the largest size in the dredging industry. These pumps are designed to counter wear problems inherent to dredge pumps. Impellers are designed in multiple categories of three, four and five vanes. To resist wear, the pump parts are made from high-chromium iron with a hardness of 60 HRC. These materials unfortunately have high elongation properties and do not resist impact. For this reason, some dredge pumps are built with an outer casing—called the double-walled pumps. The large pumps are connected in series, reaching a final pressure of 30 bar by the third pump. The pumps often weigh more than 100 tons for one complete assembly, including wet parts, outer casing, plates, shaft, bearing assembly and pedestal. Size, weight and component resistance, among other factors, create an imposing challenge for dredge pump designers.
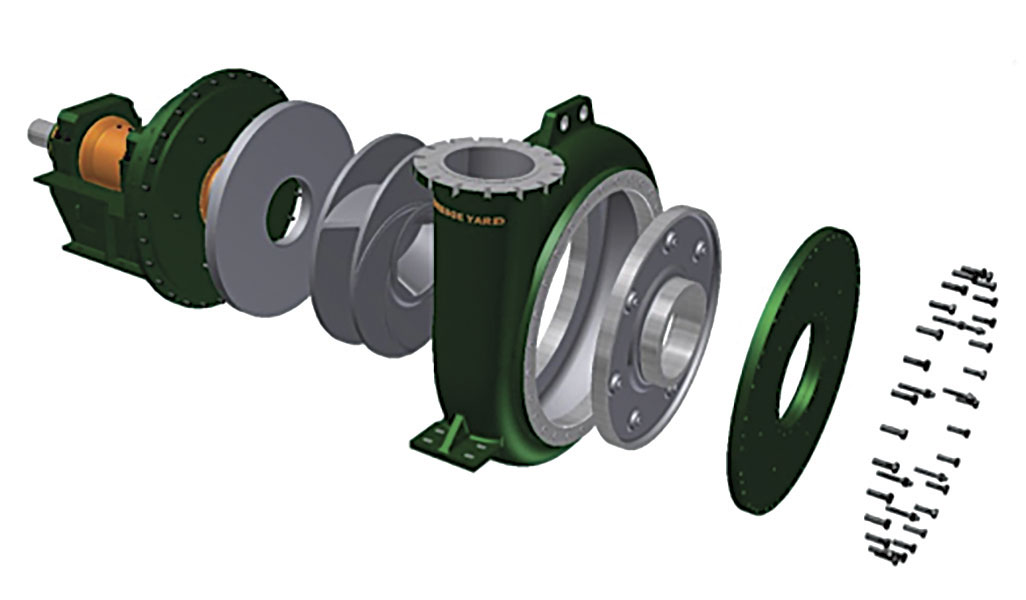