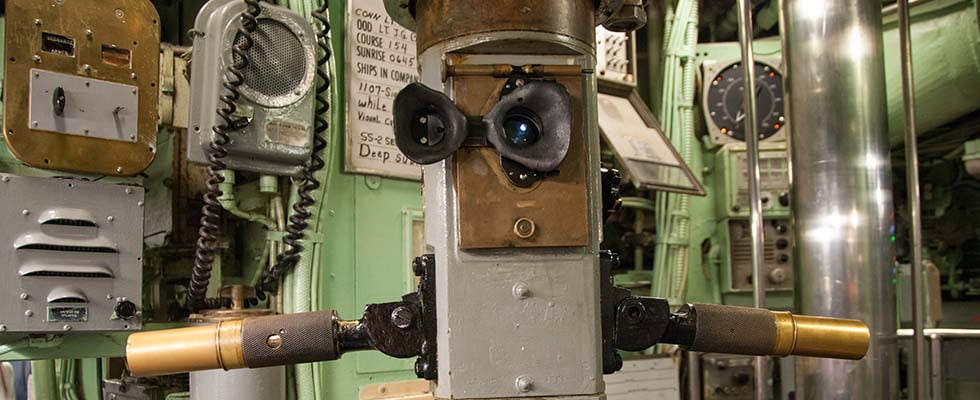
Friction has long been a hidden challenge, causing inefficiencies and problems across industries and even history. Whether in modern industrial control valves or submarine periscopes during World War I, managing friction is critical. Add to this the complexities of sealing different types of media, and the importance of reducing friction becomes even clearer. Let’s explore these parallels and how advanced sealing solutions can address these issues.
Control valves are essential for regulating the flow of fluids in industrial plants. However, they often face challenges from friction—especially stiction, or high static friction. This makes it harder for the valve stem to move smoothly, requiring more force from the actuator. When friction levels exceed the actuator’s capacity, it can cause pressure cycling, inefficiency and even equipment failures.
The issue is even more critical in emissions control applications. Valves in low-emission (LowE) service must seal volatile or hazardous media effectively while maintaining low friction to avoid actuator strain. Packing that delivers both tight sealing and reduced friction is essential in these environments. Advanced packing solutions help minimize stiction while providing reliable sealing, reducing energy use and extending equipment life.
Another challenge is undersized actuators, which are common in older systems. When actuators lack the power to overcome friction, valve performance suffers. Operators may attempt to compensate with frequent adjustments, but this often leads to more wear and tear. Properly designed low-friction packing reduces the demand on actuators, helping even older systems operate more effectively.
High friction is not just a modern problem. During World War I, German U-boats faced similar challenges with their periscopes. These devices used packing to prevent water ingress, but this often created significant friction. Moving the periscope became difficult, slowing down decision-making and reducing accuracy.
The sinking of the Lusitania in 1915 is one of history’s most infamous examples. The German U-20, under Kapitänleutnant Walther Schwieger, successfully torpedoed the British ocean liner while it was crossing the Atlantic from New York to Liverpool. The ship sank in 18 minutes, killing almost 1,200 of the 1,960 people on board, including 128 American citizens. The sinking caused international outrage and helped turn public opinion against Germany.
Early design U-boat crews frequently struggled with periscope maneuverability due to friction issues because German U-boats relied on periscopes to identify and target enemy ships. The packing used to seal these periscopes, though essential for preventing leaks, often caused significant friction. This made periscopes difficult to rotate, delaying critical decisions during combat. These delays could have jeopardized missions or led to missed opportunities in other engagements, demonstrating how friction, even in seemingly minor systems, could impact wartime outcomes.
Sealing different types of media adds another layer of complexity. Control valves may handle gases, liquids or hazardous chemicals, each with unique requirements. For emissions control, maintaining a tight seal is critical to preventing leaks, but it must be done without creating excessive friction that could overload actuators or disrupt operations.
Low-friction packings are designed to address these challenges. By balancing sealing performance with reduced friction, they ensure smooth valve operation even in demanding conditions. This is especially important for applications where emissions compliance, safety and efficiency are non-negotiable.
Both industrial control valves and submarine periscopes show how friction can undermine performance. In industrial settings, it can reduce safety and reliability, while in submarines, it could mean life or death. In both cases, managing friction is key to achieving the desired outcomes.
For industries, reducing friction is not just about efficiency: it is about meeting the demands of increasingly complex systems and regulations. By adopting advanced sealing solutions, operators can improve system reliability, reduce maintenance and extend equipment life.
Reducing friction while maintaining effective sealing is one of the biggest challenges in sealing technology. As systems become more complex and regulations tighten, the need for innovative solutions will only grow. Whether inspired by lessons from history or the demands of today, finding better ways to manage friction is essential for both safety and success.
We invite your suggestions for article topics as well as questions on sealing issues so we can better respond to the needs of the industry. Please direct your suggestions and questions to sealingsensequestions@fluidsealing.com.