First of Two Parts According to the U.S. Energy Information Agency, growth in power generation is expected to increase 8 percent while demand for electricity is expected to grow 8 to 9 percent from 2011 through 2020. Compounding this growth are aging plants with critical equipment at the end of its life—increasing demands for reliability—and an aging workforce reaching retirement in the next few years. All these factors exponentially increase the need for effective and automatic knowledge transfer, training and new approaches to the maintenance of power generation assets. Today, the process of condition monitoring is largely conducted manually, meaning technicians and operators monitor equipment on their walking rounds or tours within a plant (Figure 1). This includes capturing data logs, inspections and assessments, performance testing, maintenance, and capturing history and events. In addition, this provides limited access to equipment condition monitoring.
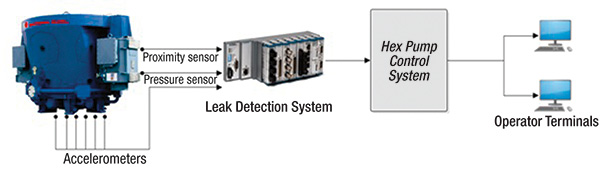
Asset Monitoring
To optimize machine maintenance and, therefore, machine reliability and use, monitoring health indicators such as mechanical vibration, temperature and power factor is a widely accepted practice. However, the cost of cabling the sensor and data acquisition hardware to the control room has impeded the use of monitoring for reliability and usage improvements. Today, with the use of wireless vibration and power monitoring devices, reliability engineers can overcome historical cost barriers. Power generation providers are taking advantage of the cost effectiveness of wireless devices to add low-cost sensors to equipment. Without the need to connect wires to transfer data, reliability engineers can expand instrumentation beyond critical assets and communicate condition monitoring data for many assets across systems. The Electrical Power Research Institute (EPRI) has calculated comparative maintenance costs in U.S. dollars per horsepower for each maintenance strategy. According to the research, a scheduled maintenance strategy is the most expensive to conduct at $24 per horsepower. A reactive maintenance strategy is the second most costly at $17 per horsepower and includes the additional costs of safety being compromised. A predictive maintenance strategy is the most cost-effective at only $9 per horsepower, and it nearly eliminates the risks of secondary damage from catastrophic failures. Conversely, one of the consequences of the development of advanced maintenance strategies, such as predictive maintenance, is the increased need for efficient information/data management methods. As an example, advanced predictive maintenance strategies require significantly larger data sets to monitor assets and effectively determine the actual state of the asset being monitored. These data sets include machine parameters, measuring points, failure modes to be detected, the relationship between faults and symptoms, and real-time math calculations. As a result, acquiring, analyzing and managing this massive amount of data, efficiently and timely and communicating operations knowledge throughout the organization becomes a complex task.Types of Asset Monitoring
Each of the five main types of machine condition monitoring serves a different role. These five are described below:- Route-based monitoring involves a technician recording data intermittently with a handheld instrument.
- Portable machine diagnostics uses portable equipment to monitor the health of machinery from sensors that are typically permanently attached to a machine.
- Online machine monitoring monitors equipment as it runs. Data are acquired by an embedded device and are transmitted to a main server for data analysis and maintenance scheduling.
- Online machine protection actively monitors equipment as it runs. Data are acquired and analyzed by an embedded device. Limit settings can then be used to control turning the machinery on and off.
Sensors and Signals
The following types of sensors dominate machine condition monitoring:- Accelerometers are used to monitor the vibrations of a machine.
- Proximity probes monitor the movement of a shaft and detect imperfections, such as faulty bearings or other external factors preventing perfect rotation.
- Tachometers determine the equipment’s rotational speed and phase information, so engineers can match frequency components to shaft speed and position.
Asset Monitoring Benefits
Implementing an asset monitoring system provides other advantages in addition to cost savings. For example, organizations can plan replacement parts inventory to meet maintenance demands by ensuring that the correct parts are available at the right location as needed, ensuring better fleet management. Also, with a longer maintenance cycle based on machine health, a longer equipment life span can be expected. Another benefit is the production assurance that an asset monitoring system provides. The system can identify developing faults with enough lead time to properly schedule maintenance during planned downtimes, avoiding unnecessary and expensive site shutdowns. Most important, by monitoring the machine and its performance parameters, the condition monitoring system can signal a system shutdown before serious injury or other harm occurs.Future-Ready Asset Monitoring Instrumentation
With the advent of advanced maintenance methods, industrial machinery and asset monitoring systems continue to become more sophisticated. As a result, the requirements for such systems are constantly evolving, which creates new challenges for selecting the appropriate instrumentation for asset monitoring. Stand-alone traditional instruments—such as temperature loggers, power quality meters, vibration analyzers and bearing checkers—that are robust, standards-based and embedded are currently available. However, they are also expensive and designed to perform one or more specific or fixed tasks defined by the vendor. Alternatively, the rapid adoption of the PC during the last 30 years catalyzed a revolution in instrumentation for test, measurement and control/automation markets. Computers are powerful, open source, input/output, expandable and programmable. Virtual instrumentation is the foundation for future-ready devices because it bridges traditional instrumentation and computers to offer the best of both worlds—a customizable, programmable system with measurement quality and embedded processing power that is capable of future expansion.Distributed Intelligence
In power plants, for example, plant operations personnel access the business network of the plant using mobile devices such as tablets and cell phone technologies. With an industrial wireless network available within the plant, personnel can access email, internal documents and drawings, and other resources that they may need while performing operations in the field. Incorporating Wi-Fi access points with process plants, including power generation and oil and gas plants, offers a clear business benefit beyond condition monitoring. However, transmission of vibration time waveforms may use all the available bandwidth even with an 802.11n implementation. To mitigate bandwidth issues with Wi-Fi, or any other radio technologies, a report featuring exception or decision-based data recording with store and forward capabilities is most appropriate (see Figure 2). Decision-based data recording devices are often referred to as a Data Acquisition and Analysis Node (DAAN). When the DAAN can evaluate all sensor values for exception and log sensor values locally, two main benefits are achieved. First, when reporting by exception sensory, data are filtered for changes, exceptions or required periodic reports. Second, recording sensor data and condition indicators is possible even when the wireless communications network is not available or experiences bandwidth degradation.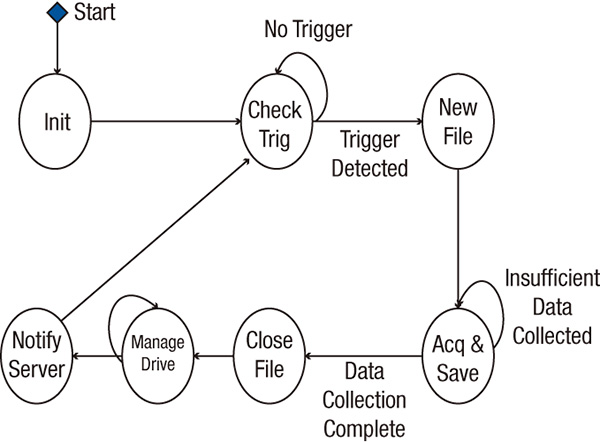