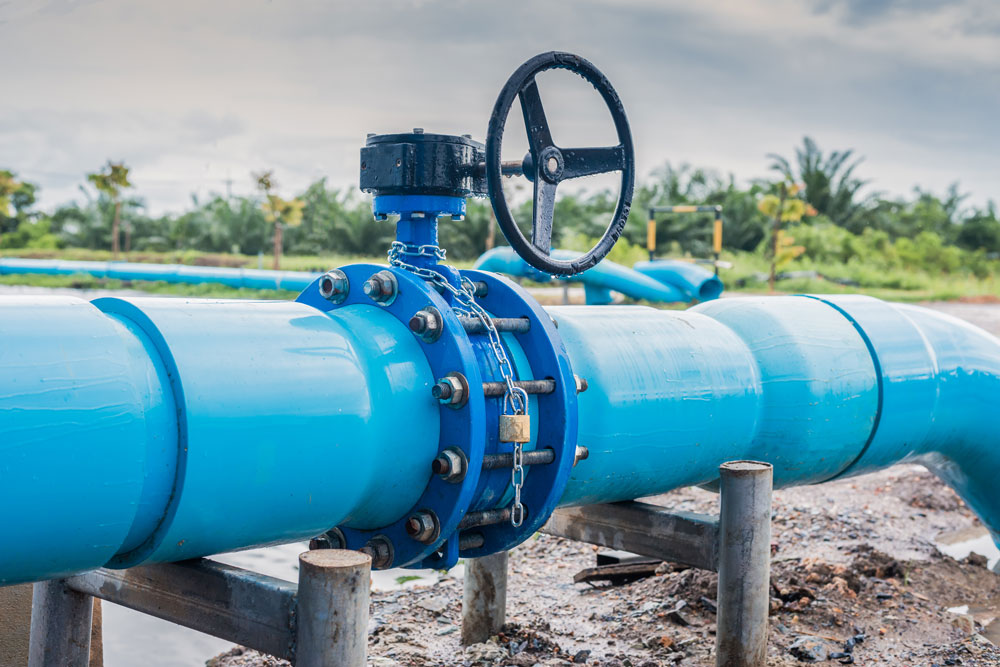
Butterfly valves are quarter-turn flow control devices that utilize a metallic disc that rotates around a fixed stem axis. They are quick-action flow control valves that allow rotations through 90 degrees to move from fully opened to a closed position.
When the disc is perpendicular to the centerline of the pipe, the valve is at a closed position. The valve will be fully open (permit maximum fluid flow) when the disc lies parallel to the centerline of the pipe. The flow control mechanism (disc) has an approximately equal size to the internal diameter of the adjoining pipe.
These valves are available in different sizes and designs that dictate their performance in industrial processing applications; sanitary valve applications; fire protection services; heating, ventilation and air conditioning (HVAC) systems; and slurries. In broad terms, butterfly valves are vital for flow regulation and flow isolation.
Flow Regulation
The movement of the disc initiates, slows down or stops the flow of fluid. Applications that demand high levels of accuracy rely on actuated butterfly valves that monitor pipeline conditions, opening or closing valves whenever necessary to maintain uniform flow rates. Butterfly valves used for flow regulation depict one of the following flow characteristics:
• Near linear—Flow rates are proportional to the angular movement of the disc. For instance, when the disc is 40% open, the flow rate is 40% of the maximum. This flow characteristic is common with high-performance butterfly valves.
• Quick opening—This flow characteristic manifests when using resilient-seated butterfly valves. Fluid flow rates are highest when the disc begins traveling from a closed position. The flow rates diminish steadily, with minimal changes as the valve nears the fully open position.
• Flow isolation—Butterfly valves can offer on/off fluid service. Flow isolation is necessary whenever sections of the piping system require maintenance.
Advantages of Butterfly Valves
Butterfly valves are suitable for different applications because of their lightweight design and quick operation. Soft-seated butterfly valves are ideal for low-temperature, low-pressure applications, while metal-seated butterfly valves offer good sealing capabilities when dealing with severe fluid service. Such processes operate at high temperatures and pressure, conveying viscous or corrosive fluids. The advantages of butterfly valves include:
• Lightweight and compact construction—Butterfly valves use thin metallic discs as flow control mechanisms. The disc is small and occupies little space, yet is strong enough to regulate the flow of fluids. These valves have compact bodies, making them suitable for piping systems in confined locations. Pipes with large diameters require bulkier valves that use more manufacturing material, increasing their cost. A butterfly valve will be cheaper than a ball valve of the same size as it consumes fewer manufacturing materials.
• Quick and efficient seals—Butterfly valves provide quick sealing upon actuation, making them ideal for high precision flow applications. The sealing characteristics of butterfly valves depend on the type of disc offset and the nature of seat materials. Zero offset butterfly valves will provide sufficient sealing for low-pressure—up to 250 pounds per square inch (psi) applications. Double offset valves provide superior sealing for processes with pressure that reaches 1,440 psi. Triple offset valves provide sealing for flow applications with pressure that exceeds 1,440 psi.
• Low pressure drop and high pressure recovery—Although the disc is always present in the flow, a butterfly valve experiences a low pressure drop. Low pressure drop is essential for managing the system’s pumping and energy needs. The design of a butterfly valve is such that it allows the fluids to recover energy quickly after it leaves the valve.
• Low maintenance requirements—Butterfly valves have fewer internal components. They do not have pockets that may trap fluids or debris, therefore, they require minimal maintenance interventions. Their installation is equally simple, as they require clamping between adjacent pipe flanges. There is no need for welding and other complicated installation processes.
• Simple operation—Due to their compact and lightweight construction, butterfly valves require relatively low torque to operate. The thin metallic disc utilizes a small amount of force to overcome the frictional resistance of the fluid. Butterfly valves are easier to automate, as small actuators can deliver sufficient torque for their operation. This translates to a lower cost of operation—small actuators consume less power and cost less to add to a valve.
Disadvantages of Butterfly Valves
• Butterfly valves are susceptible to cavitation and choked flow—At the open position, the valve does not provide a full port. The disc’s presence in the path of flowing fluids escalates debris accumulation around the valve, increasing the probability of cavitation. Ball valves are an alternative for fluid applications requiring a full port.
• Rapid corrosion in viscous fluid service—Fluids scour against the discs of butterfly valves as they move past them. With time, the disc deteriorates and can no longer provide sealing. The rate of corrosion is higher if dealing with viscous fluid service. Gate valves and ball valves have better corrosion resistance than butterfly valves.
• Unsuitable for high-pressure throttling—The valves can be used for throttling in low-pressure applications only, with the opening restricted to between 30 degrees and 80 degrees. Globe valves have better throttling capabilities than butterfly valves.
The presence of a disc at a fully open position impedes the cleaning of a system and makes lines containing butterfly valves non-piggable.
Guidelines for the Installation of Butterfly Valves
The installation position of butterfly valves is usually between flanges. Butterfly valves should be installed at least four to six pipe diameters away from discharge nozzles, elbows or branches to minimize the impacts of turbulent flow.
Before installation, clean the pipeline and check the smoothness/flatness of the flanges. Ensure that the pipes align. When installing the valve, keep the disc in a partially open position. It may be necessary to spread the flanges to avoid damages to the seat faces. Use locating holes or a sling around the body when lifting or moving the valve. Avoid lifting the valve at the actuator or its operator.
Align the valve with the adjacent pipe’s insert bolts. Tighten the bolts by hand and then by a torque wrench and slowly tighten the bolts evenly to estimate clearances between them and the flanges. Turn the valve to a fully open position and check the bolts by tightening them using a torque wrench for uniform tensioning.
Maintenance of Industrial Butterfly Valves
Maintenance of valves involves the lubrication of mechanical components, inspection and repair of actuators. Valves with requirements for regular lubrication contain fittings from where grease is applied. Sufficient lithium-based grease should be applied at recommended intervals to minimize rusting and corrosion.
Inspection of the actuators at regular intervals to identify any signs of wear or loose electrical, pneumatic or hydraulic connections that may affect valve operation is also important.
In addition, users should clean all parts of the butterfly valve using a silicon-based lubricant. The valve seats should be inspected for any signs of wear and replaced whenever necessary. The discs of butterfly valves used for dry applications like compressed air service need to be lubricated. Butterfly valves that are not frequently cycled should be operated at least once monthly.
Additional Considerations When Selecting a Butterfly Valve
Valve selection may seem like a pick-and-plug activity, however there are several technical specifications to consider. The first involves understanding the type of fluid control required and the type of service fluid. Corrosive fluid service requires valves made from stainless steel, a nickel-chrome-based superalloy or other resistant materials.
Users need to consider the capacity of the piping system, pressure and temperature variation and the desired levels of automation. While actuated butterfly valves provide precise flow control, they are more expensive than their manually operated counterparts. Butterfly valves are not pigabble and cannot offer a full port.
If a user is unsure of the process’s chemical compatibility or actuation selection, a qualified valve company can assist to ensure correct selection.