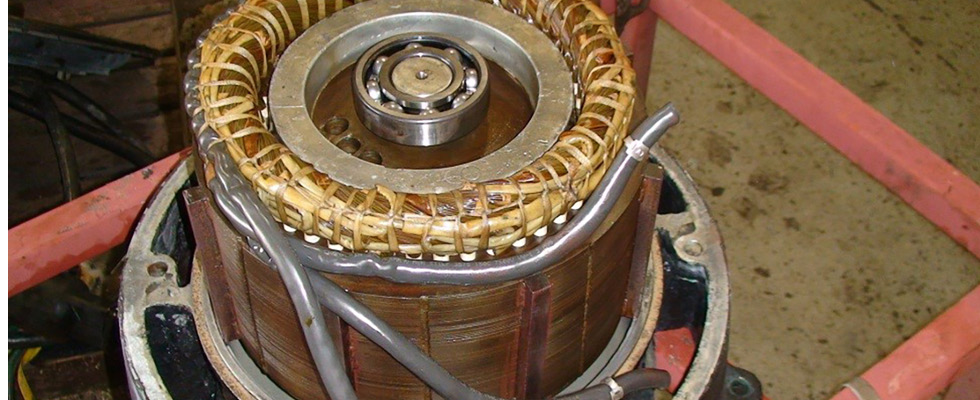
Most submersible pumps have a dual seal arrangement with seal oil in the cavity between the seals. The seal oil should be selected to meet the manufacturer’s requirements. Some submersible pumps also have an oil-filled stator cavity.
The oil in the stator cavity efficiently transfers heat from the stator winding and core, and especially from the rotor, to the pump casing where convection carries it to the pumpage in which the pump is submerged. While the specifications for seal oil are fairly flexible, stator cavity oil has more constraints.
A primary constraint on oil filling any stator is its ability to resist the flow of electrical current, known as dielectric strength. Obviously, it is preferred for oil in the stator to have high dielectric strength. Because this is its primary characteristic (due to refining-enhanced naphthenic vs. paraffinic content and moisture elimination), transformer oil is recommended for use in most stators. In addition, some types of transformer oil (Type II) include antioxidation additives.
These are helpful in transformers that breathe with heat cycles, pulling in external air and oxygen. A third characteristic of transformer oil is low viscosity, typically in the range of 8-10 centistokes (cSt) at 40 C, which enhances thermodynamic circulation induced in transformers. However, the characteristics of submersible pump stators and transformers are different. Submersible pump stators do not breathe. They are sealed and submerged, so oxidation is not a concern. The dielectric strength requirements also are much lower on a low-voltage stator than on a medium- or high-voltage transformer.
As a result, the following questions sometimes arise: Is transformer oil the best choice for submersible pump stators? Could turbine oil be substituted? The answer is both yes and no. Yes, there may be special circumstances where turbine oil could work, but no, it is not a recommended practice.
If a turbine oil had the proper viscosity, it could certainly cool the stator and rotor. But the most common turbine oil in service centers is International Organization for Standardization (ISO) 32—too viscous for use in stators. Another concern for submersible pumps, especially those in sewage applications, is explosion-proof ratings. Many sewage pumps have factory mutual (FM) explosion-proof ratings. Since FM certifies the machine design, not specific machines, these pumps can be repaired in service centers if the design is not changed. That often requires OEM replacement parts, and off-spec oil in the stator would be a design change. Underwriters Laboratories (UL) certified pumps have more stringent repair restrictions.
An additional concern is the compatibility of the oil with the insulation and sealing components of the submersible pump. Electrical insulation vendors can provide compatibility information when rewinding a submersible pump stator. But those materials in an existing winding would not be known. The consequences of an oil leak into the pumpage should also be considered. Some applications require food-grade cooling and lubricating fluids.
For a non-Ex-rated pump, the proper viscosity turbine oil could be substituted for transformer oil in an emergency. But it is not a recommended practice. The recommendation is to use the oil specified by the machine manufacturer.