Metallics and plastics offer advantages for different applications.
03/17/2015
Choosing the right pump material to handle aggressive fluids is critical to the success of any processing operation. Aggressive fluids are those that either corrode or abrade the pumps used to handle them, including acids, caustics, reagent grade chemicals and unknown wastewater effluents. Selecting the appropriate material for handling these aggressive liquids requires careful analysis to avoid incurring the cost of premature pump replacement and downtime. Metal and plastic are the two major types of materials used for pumping harsh liquids. Pump users must consider multiple factors to select the optimal material for their specific requirements.
Metallics
Historically, exotic metal alloy pumps were the tried and true solution for the proper handling of harsh fluids. These materials were so ubiquitous among processing professionals that corrosion-related pump failure was considered both predictable and anticipated by independent sources. Examples of such sources are Compass and Schweitzer, compendia that detail the expected service life of materials in a given corrosive fluid. The shortcoming of these measurements, however, is that they are taken in a static condition. When these materials must perform at high speeds, their life expectancy is curtailed even further. When dealing with metals, users must be aware of the four types of metallic corrosion.- General Corrosion - The formation of a passive film on a metal's surface is what prevents it from degrading.
- Galvanic Corrosion - This phenomenon occurs when two or more disparate metals come in contact with one another or when metals with the same analysis have different surface conditions and an electrolyte is present, which forms an electrolytic cell.
- Stress Corrosion Cracking - Since all metals have residual or applied stress, they are prone to stress corrosion cracking, which is affected by extreme thermal changes, excessive vibrations, and expansion or contraction.
- Intergranular Corrosion - This type occurs only at the grain boundaries of carbon-containing austenitic stainless steels. If the steel is heated above 1,000 F, the carbon is released at the grain boundaries, causing the area to become more susceptible to corrosive attack.
Plastics
How does a user select the right plastic for handling a specific harsh liquid? The first step is to recognize that choosing the ideal plastic pump is not a cure-all for every pumping application. In high-temperature or high-pressure applications, metallic pumps perform better (see Table 1). In applications in which chemical compatibility is a primary consideration, however, plastics are considered the material of choice.
Thermosets
Thermosetting plastics are composites, not homogeneous materials. Commonly referred to as fiber reinforced plastics (FRP) or glass reinforced plastics (GRP) materials, thermosets are constructed of vinyl ester or epoxy resin reinforced by glass fibers. The strength of FRP and GRP materials is influenced by variations in its composition.For this reason FRP/GRP pumps are commonly referred to by their trade names, which provide specific analyses of the materials made by their manufacturer. FRP/GRP's rigid properties (their tensile strength, for example) more closely match those of metallics than thermoplastics. Their resistance to corrosives increases as vinyl is added to their formulation, while their resistance to solvents is enhanced by their epoxy content. Thermosets can be custom-formulated to meet specific service conditions, because different formulations of their components (glass fiber/epoxy) can impart different values to the composite material. For this reason, standard corrosion charts are not always helpful. Instead, performance characteristics should be determined by the manufacturer's and the user's prior experience. Because of the specificity of this type of material, users should employ careful consideration when selecting thermoset pumps for applications in which the fluid is unknown. Thermoset pumps will resist most chemicals and can reliably be used in applications in which the fluid reaches 300 F or higher. Users should be cautious, however, when using thermoset pumps to handle solids-containing liquids. In these applications, the pump's resin surface may be abraded, exposing the reinforcing fibers. This may expose glass fibers beneath the surface, which could result in severe damage and even pump failure. Since FRP/GRP pumps are formulated to handle a narrow and specific type of caustic liquid, they are limited in the range of harsh liquids they can handle effectively.
Thermoplastics
Thermosets and thermoplastics are much lighter than metallics, providing ease of installation and maintenance. Unlike thermosets, thermoplastics are engineered materials, giving them unique properties including a broad range of chemical compatibility and resistance to impact, abrasion and heat. Typical thermoplastic materials used in pumps for handling harsh liquids include:- Polypropylene (PP)
- Polyvinyl chloride (PVC)
- Chlorinated polyvinyl chloride (CPVC)
- Polyethylene (PE)
- Polyvinylidene fluoride (PVDF)
- Ethylene chlorotrifluoroethylene (ECTFE)
- Polytetrrafluoroetheylene (PTFE)

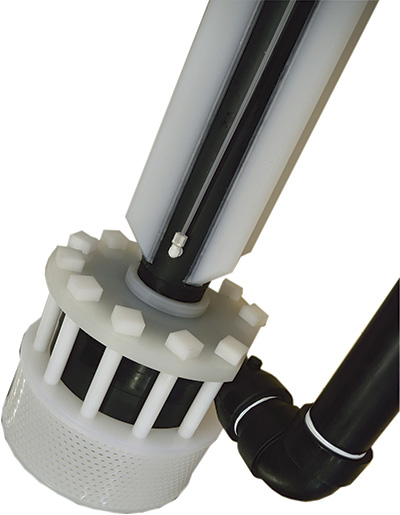
Conclusion
Selecting the ideal material for pumping harsh liquids is a matter of weighing performance and cost. The pump's purchase price should not be the sole determining factor. Users should also consider the cost of replacement parts and downtime. When planning a new system or replacing an existing pump, thorough analysis is necessary for selecting the most favorable material and ensuring long-term, dependable performance. When selecting the basic construction material for a pump that will handle aggressive fluids, users should first take into account the fluid being pumped, the operating temperature of the fluid and the pressure of the application. If the temperature is 300 F or higher, a metallic pump is probably the ideal solution. When the fluid being pumped is 250-300 F, materials such as fluoropolymers (PVDF, ECTFE or PTFE) will prove most effective. If the temperature of the pumped liquid is below 250 F, however, an FRP and a thermoplastic should be considered. If product purity is paramount, natural, unpigmented PP or PVDF will perform best.Advantages of Thermoplastic Pumps over Fiberglass Reinforced Plastic (FRP) Pumps
- No interbatch product contamination
- Solid homogeneous thermoplastics do not wick or absorb by capillary action
- Superior resistance to abrasion compared with thermoset composites
- Greater chemical resistance coverage over the full pH range
Advantages of Thermoplastic Pumps over Metal Pumps
- No galvanic corrosion or rusting
- Superior resistance to abrasion
- Greater chemical resistance over the full pH range compared with metals
- No ionization/metallic contamination of the fluid
- No galling problems
- Significantly lighter in weight, facilitating installation and maintenance