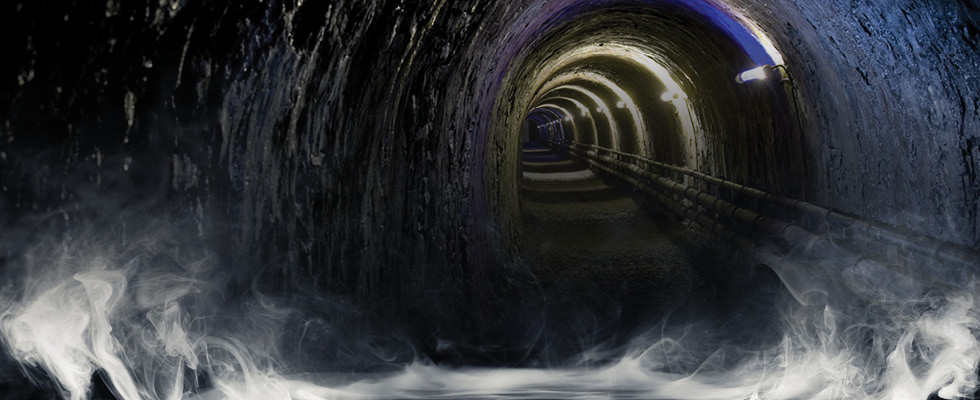
Steam tunnels are an essential element of modern infrastructure, functioning as protected passageways for steam distribution and utility conduits. These tunnels, often built beneath urban landscapes, allow centralized steam systems to deliver heat, energy and other utilities to facilities while safeguarding the network from external damage caused by weather, construction or environmental factors. Steam distribution is a cost-effective and energy-efficient method for meeting heating, sterilization and industrial processing needs, making steam tunnels indispensable in large campuses, industrial plants and dense metropolitan areas.
Steam tunnels provide physical protection and a controlled environment that facilitates routine inspections, repairs and upgrades of utility systems. They eliminate the need for disruptive excavation or exposed piping, ensuring uninterrupted utility services. However, the operating conditions within these tunnels are harsh. Temperatures often exceed 180 F due to the thermal energy transferred from steam pipes, and humidity levels hover near 100%, making the environment extremely steamy and corrosive. Condensation from pipes, combined with occasional leaks, can lead to water accumulation, forming hot, chemically reactive pools that threaten the longevity of the infrastructure.
This harsh environment poses significant challenges for equipment and maintenance. Materials exposed to these conditions must resist thermal degradation, corrosion and physical wear. Over time, without effective drainage, water can flood the tunnels, weaken structural integrity and endanger the safety of maintenance personnel. The inclusion of specialized drainage systems, particularly high-temperature submersible pumps, ensures the tunnels remain functional and safe, even under extreme conditions. These pumps play a critical role in managing corrosive and high-temperature water, maintaining the efficiency of steam systems while protecting infrastructure.
The Role of High-Temperature Submersible Pumps
To address the challenges of steam tunnel environments, high-temperature submersible pumps are essential. These pumps are engineered to operate reliably under high heat, extreme humidity and in the presence of corrosive and solids-laden water. Unlike standard pumps, which often fail under such conditions due to overheating, seal degradation or clogging, high-temperature submersible pumps are designed with specialized materials and components to ensure durability and consistent performance.
Corrosion in steam tunnels is a significant issue that arises when metallic components deteriorate due to harsh environmental conditions and chemical interactions, compounded by exposure to high temperatures and heat. A common cause is the accumulation of moisture and condensate, where steam condenses into water that combines with impurities like dissolved oxygen or carbon dioxide, creating acidic or oxygen-rich environments. High temperatures further accelerate these reactions, leading to faster material degradation. Dissolved gases, especially oxygen and carbon dioxide, contribute to oxygen pitting and the formation of carbonic acid, which reduces pH and intensifies corrosion. These specialized pumps are constructed with 316 stainless steel—a material specifically selected for its superior resistance to low-pH and corrosive environments, making it well-suited to endure the harsh chemical and thermal stresses of steam tunnels. The presence of salt in the steam significantly accelerates corrosion, leading to bolt failures caused by vibration-induced shearing. To address this issue, pumps are equipped with brass hardware, which offers superior resistance to corrosion in such demanding environments.
Traditional high temperature pumps are equipped with double mechanical seals made of silicon carbide, carbon ceramic and fluoroelastomers (FKM) capable of handling temperatures up to 200 F (98 C). For more demanding scenarios where ambient temperatures range from 200 F to 375 F (98 C to 190 C), pumps can be upgraded with perfluoroelastomer (FFKM) seals to provide enhanced durability and reliability. Another critical consideration is preventing the motor from overheating due to the high temperature of the pumped media. The motors are equipped with R-class insulation capable of withstanding thermal stress up to 300 F (150 C), while the stator windings are coated with a specialized varnish to ensure reliable operation under elevated temperatures. The motors are oil-filled to enhance heat regulation and dissipation, effectively prolonging the insulation’s life span and delivering consistent performance in demanding and high-temperature environments. Additionally, the cable used in these pumps is a proprietary fluoropolymer insulated cable that can operate in these harsh conditions and is rated up to 392 F (200 C).
High-temperature submersible pumps are indispensable in steam tunnel management, ensuring the reliability, safety and efficiency of centralized utility systems. By effectively removing hot, corrosive wastewater, these pumps prevent water accumulation that could compromise the structural integrity of the tunnels and the systems they house. Their robust construction not only minimizes equipment stress but also reduces the frequency of repairs and replacements, delivering long-term cost savings. These pumps play a critical role in maintaining uninterrupted heating and utility services in vital facilities such as hospitals, universities and industrial complexes. Their combination of durability, reliability and cost-effectiveness makes them a cornerstone of modern infrastructure, safeguarding essential services and enhancing the safety of maintenance operations in challenging environments.