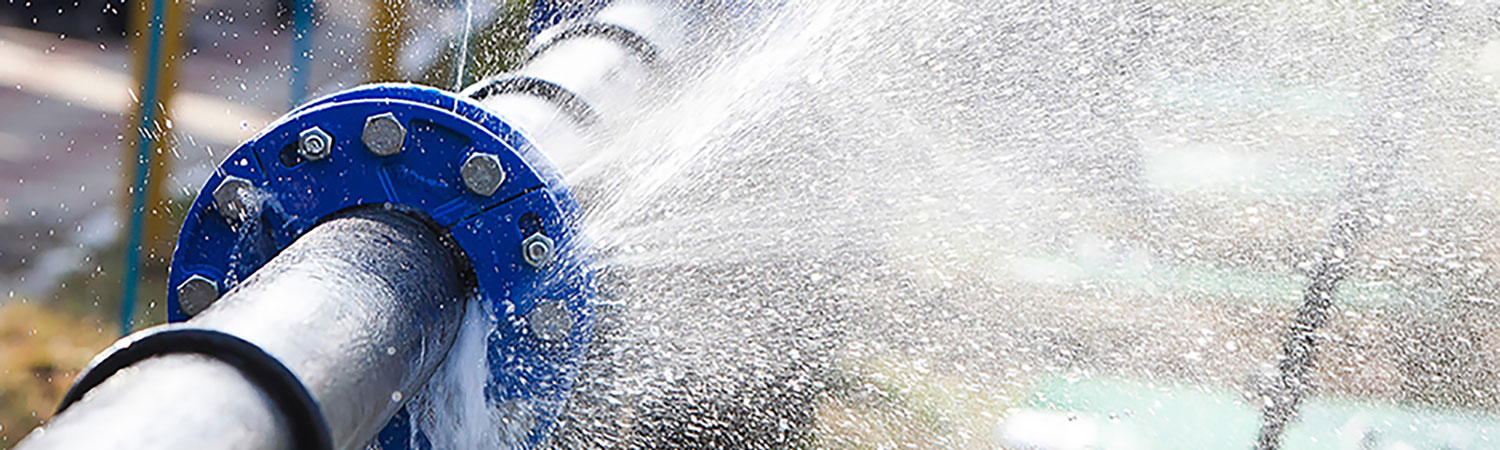
Why is the gasket leaking? This is a question that is asked time and time again. To achieve an accurate answer, the big picture needs to be looked at. Gaskets are just one part of the bolted system. When trying to create an optimal seal with a gasket, many other factors need to be considered. The solution could be as simple as changing the gasket material or as complex as updating the bolted joint system.
Before discussing an optimal seal, define gaskets. A gasket is used for sealing applications to create and retain a static seal between flanges. The flanges themselves are attached to components such as pipes, valves or pumps for a piping system. These piping systems will contain various types of media, which can range from air to highly corrosive acids. When a gasket is installed, it will act like a barrier from the media and will prevent any leak paths from occurring—thus, creating an optimal seal.
To maintain the seal, it is important that the load on the gasket is enough to fill any irregularities and block any potential leak paths. Three forces are involved in the bolted joint: the bolt load (keeps everything together), hydrostatic end force (tries to push flanges apart and stretches the bolts leading to a lower gasket compression), and the blow-out force (tries to force the gasket out of the flange). To maintain an optimal seal, the bolt load minus the hydrostatic end force needs to be greater than the blow-out force.
In industry, there is no “one-for-all” gasket. There are many types of gaskets, and they are manufactured with a variety of materials. Not all gaskets can be used in all applications, and it is crucial to select the proper gasket for the application. There are different types of gaskets such as nonmetallic (soft), semimetallic and metallic. Soft gaskets may include compressed non-asbestos (CNA) or fiber, flexible graphite, and polytetrafluoroethylene (PTFE). Some examples of semimetallic gaskets are spiral-wound gaskets and corrugated metal and metallic such as ring type joints (RTJs).
Flanges are critical, but rarely will there be a perfect flange. Some examples of irregularities that can affect gasket selection can be pitting, corrosion or flange misalignment. Check out Appendix D and E in American Society of Mechanical Engineers (ASME) PCC-1 for more flange considerations such as flatness, surface and damage. When flange conditions are acceptable, the maximum sealing contact can be achieved, which allows for better gasket load distribution.
Even when selecting the proper gasket and having ideal flange conditions, it does not mean an optimal seal will be guaranteed. Installation is possibly the most understated component when trying to achieve proper loading on the gasket. It is important to have a qualified assembler (based on ASME requirements) that has the properly calibrated tools.
It is essential to use one gasket and to never reuse a gasket. When a gasket is reused, it will be unable to recover up to 100% of the original thickness and the recovery of the gasket will drastically decrease each time it is compressed.
It is important to always use lubrication during installation. If lubrication is not used at all or the proper amount is not used, it can take away what theoretically is being applied to the gasket. The components of the bolted joint to lubricate are the bolt threads, nut threads, nut flange facing and both sides of the washers. Lubrication should never be applied to the gasket or any surface that the gasket will meet. If lubrication or grease is applied to the gasket or gasket surface, it can cause the gasket to become chemically attacked and can, ultimately, lubricate the sealing surface and allow the gasket to be pushed out easily by the system pressure. The gasket should be compressing enough to fill the flange serrations, which will allow the flange serrations to bite into the gasket and resist being pushed out from the system pressure.
Proper bolting should always be used in the bolt joint system, and it is important to ensure bolting (40% to 70% of the yield range) will be high enough to achieve a proper seal. For example, an A-193 Grade B8M has a yield of 30,000 pounds per square inch (psi), where SAE Grade 8 bolts have a yield of 130,000 psi. The clamping capability of a bolt is determined by its elasticity. This elasticity is the ability of the bolt to return to its original shape after being deformed. It is always recommended to use washers because they allow for the load to be distributed evenly and will prevent the nut from embedding into the flange, which can cause further friction issues.
The torque used for installation is important to prevent leaks. The maximum bolt torque is typically based on the maximum permissible bolt load. This allows a buffer from variations due to inaccuracy of installation, losses due to creep relaxation, losses to internal pressure and external loading and losses due to thermal loading. In some scenarios, the torque based on the maximum permissible bolt load cannot be achieved. In some instances, the maximum gasket stress for the material will max out before the maximum permissible bolt load can be achieved. Installation is a crucial part of the assembly process, and it is important to follow the guidelines set out by ASME PCC-1 to ensure appropriately qualified personnel from a qualified organization are doing the installation and conducting any training.
Many factors need to be considered when trying to achieve an optimal seal. When these factors are considered in the gasket selection and installation, they can help reduce costs from downtime and fines, prevent safety issues and stop fugitive emissions. If there are concerns on proper installation, it is important to contact the gasket manufacturer for selection help and refer to ASME PCC-1-2019 for installation guidance.
We invite your suggestions for article topics as well as questions on sealing issues so we can better respond to the needs of the industry. Please direct your suggestions and questions to sealingsensequestions@fluidsealing.com.