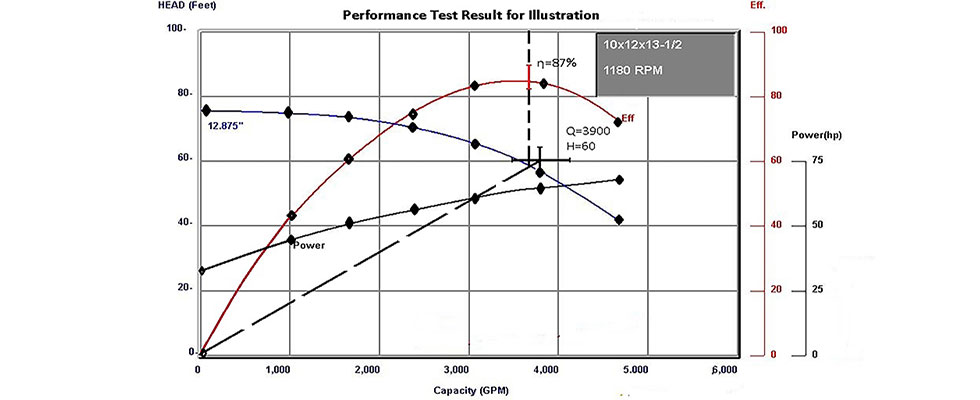
In a world filled with so many choices, it is not surprising that the decision on how to maximize energy savings on a new project or retrofit is not an easy one.
There are important considerations when evaluating published pump performance and different testing options to achieve performance levels acceptable for an application. Guarantee point efficiency, part-load efficiencies, motor efficiencies, drive efficiencies and control strategies all come into play when determining the energy required to operate a system from a pumping standpoint.
Just like the materials of construction, the seal type and the impeller trim have an impact on pump performance. Even if a performance test is requested in accordance with Hydraulic Institute/American National Standards Institute (HI/ANSI) 14.6 for a specified guarantee point, if the actual test grade is not specified in the order/quote, the manufacturer will likely apply the default test grade for the intended service. It is important to review the current revision of HI/ANSI 14.6 to understand the default acceptance grades per application and shaft power along with the current grades and their associated test bands. It will be easier and more economical for the manufacturer to comply with requests that align with published standards as opposed to a custom specification developed for a specific project or user.
Pump Performance vs. Published Curve
A reasonable assumption is that a pump would perform closely to its currently published curve. But many curves, whether published in a booklet or displayed on selection software, do not specify the intended service or what grade they would certify to. Why is this important? Many factors influence how close to the published curve a pump will actually perform.
According to HI, variations in hydraulic performance are the result of manufacturing tolerances, testing instrument fluctuations and accuracy, driver (motor) variation, and the inherent instabilities in the pumped media near the pump suction and discharge. The magnitude of these variations will vary directly with the degree of precision applied to manufacturing processes, the test equipment and test procedures. The higher the precision used in manufacturing and testing, the smaller the expected variations in test results. The published curve will likely represent an average of the historical performance of similar units.
If a pump is specified as requiring compliance to a grade higher than what the manufacturer assumed in its published curve, a quote from the manufacturer may come with a trim that is different from the published curve used to make the original selection. In fact, if the specified duty point falls on the maximum trim for a pump, the manufacturer’s quote may come with a different pump or motor than originally specified in order to achieve the guarantee point at the tighter performance tolerance. This is different from a scenario where no performance tolerance was specified, and the pump was either not tested or was tested to a general standard in the case that the manufacturer was not specifically informed about the type of application and, therefore, standard to apply.
Even if a performance test and grade are specified, it should be noted that many only ensure testing of head and flow to that grade at the specified guarantee point. The testing standard is specific and should be consulted to understand what will be included in a normal test and what must be additionally specified. Power or efficiency may not be guaranteed without being additionally specified. Another consideration is that some grades may have a bilateral (positive and negative) tolerance or a unilateral (positive only) tolerance for head and flow.
It is important to understand what aspects of pump performance will be most critical for the application and match requirements accordingly. Will the pump be operated with a variable speed drive (VSD)? Is maximum pressure or maximum horsepower a concern? Is the net positive suction head available (NPSHa) a concern?
Ensuring Application Requirements Are Met
The good news is that there are steps that can be taken to ensure future pumps satisfy requirements. While every project cannot justify the additional cost of a certified performance test to the tightest tolerance band on pump flow, head and efficiency, it does not mean that users cannot ensure that the application requirements are met.
When creating a pump specification, make sure to include that the pump must perform to a specified grade at a minimum and all submittals should include a curve to meet that grade. If the order contains a certified test requirement, be explicit in the test specification for head, flow and/or efficiency. It is up to users as the specifiers to include this information in the specification. As an alternative, a tighter tolerance for head and flow can be specified, with a lower tolerance for efficiency.
If users are concerned about overloading the motor, consider specifying a maximum horsepower and flow range to be evaluated. If users are going to be operating the pump with a VSD, the duty point may be achieved at other than the typical motor test speed. Remember to either specify the reduced test speed or provide a guarantee point that will fall on the constant speed curve of the pump.
These are all important agreements to have upfront. It will be difficult to start adding or changing criteria once there is a completed test report and the manufacturer is waiting for approval to ship.
A tighter performance specification or additional test requirements typically equate to additional costs for the pump. It can also extend lead times as the manufacturer takes additional steps to ensure compliance and schedule the testing. Balance these short-term issues with the longer-term issues of pump performance. Understand exactly what is needed to make the project successful and then specify the requirements precisely.
A good specification maximizes project outcome and provides clear guidance on expectations to the manufacturer. A cut and paste of old specifications risks disappointment and a last-minute scramble to make system adjustments at commissioning.