Arc-resistant switchgear has been available since the early 1990s, first seen in Europe and Canada and later specified with increasing frequency in the United States. At first, no American National Standards Institute/National Electrical Manufacturers Association (ANSI/NEMA) standards existed to define the test procedures that the switchgear sold in the U.S. had to undergo. In 2001, the Institute of Electrical and Electronics Engineers (IEEE) created the C37.20.7 “Guide for Testing Medium-Voltage Metal-Enclosed Switchgear for Internal Arcing Faults.” This guide was updated in 2007 and is now called the “Guide for Testing Metal-Enclosed Switchgear Rated Up to 38 kV for Internal Arcing Faults.” As safety has become a top priority in the industry, and acceptance of arc-resistant technology has increased, arc-resistant testing has expanded to include medium-voltage metal clad switchgear, low- and medium-voltage motor control, and recently medium-voltage adjustable frequency drives.
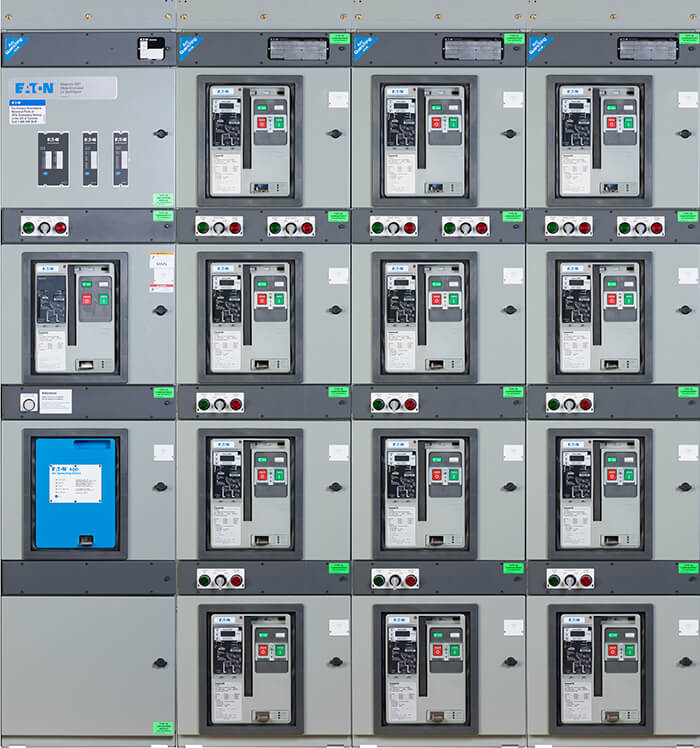
- Properly latched or secured doors, covers and so on do not open.
- No fragmentation of the enclosure occurs within the time specified for the test.
- That arcing does not cause holes in the freely accessible front, sides and rear of the enclosure (Type 2).
- No indicators ignite as a result of escaping gases (cotton indicators are placed 4 inches from the sides of the equipment being tested to simulate cotton clothing worn by an operator).
- All the grounding connections remain effective.