Waiting to replace packing in centrifugal pump service can lead to downtime and safety issues.
05/22/2015
Compression packing has been around since the beginning of the industrial revolution and is still used extensively in types of equipment in which a stuffing box seal is required to prevent loss of process fluids to the environment. While advanced sealing solutions for rotary applications, such as mechanical seals, emerged over time, compression remains an important industrial tool.
Gland Pressure
A compression packing seal is established by installing the packing ring set into the stuffing box (see Figure 1). Then, the gland on the back of the stuffing box is tightened to compress the packing between the shaft and stuffing box wall. Once compressed, the packing expands, exerting a radial force to the sides of the stuffing box and against the shaft.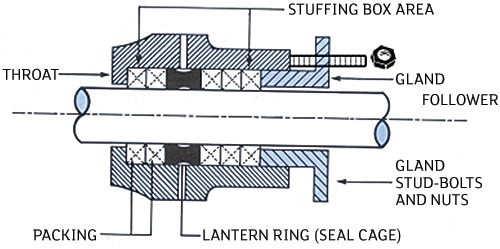
Packing Material
The choice of packing material affects the operating costs of centrifugal pumps, but little is known about the relationship. The Fluid Sealing Association (FSA) and European Sealing Association (ESA) began to address this lack of data by developing industry standard test methods to shed light on how packing behaves. The acronym "STAMPS" can be used to remember key considerations that can determine which packing material and construction should be selected: S Size – What are the stuffing box dimensions? T Temperature – What is the temperature of the medium? A Application – What type of equipment is it? M Media – What medium is being sealed? P Pressure – What is the internal pressure being sealed? S Shaft speed – What is the surface speed of the shaft?Compression Packing Failure
One common mistake is the tendency to maximize the packing's time in service to a perceived point of failure before replacing it. Defining failure is more a matter of opinion than science. Signs that the packing has failed include increased leakage, smoke at the stuffing box or uncontrolled leakage at the gland. Safety-conscious operators service the pump and replace the packing at regular intervals. However no common criteria for determining the replacement frequency or relating it to the packing material are available. An acceptable replacement cycle time is heavily dependent on the application, the equipment and the packing. The confusion occurs because of the forgiving nature of compression packing. Pump operation is not impaired until the packing fails. It should be replaced long before this occurs. For any type of packing, operating costs are relatively fixed when it is functioning correctly. As performance deteriorates, operating cost increases are much larger than the initial cost of the packing ring set. Based on the way packing works, three factors affect costs:- Power loss, shaft/sleeve abrasion and material wear caused by friction
- External flush fluid leak rate from the stuffing box to dissipate heat caused by friction
- Labor to adjust gland pressure to maintain minimal leak rate from the stuffing box
Signs of Failure
After the pump and auxiliary systems have achieved a steady state, measure the temperature at the stuffing box and record the difference from the ambient temperature. For example, if ambient is 65 F and the stuffing box is 110 F, the operating baseline differential is 45 F.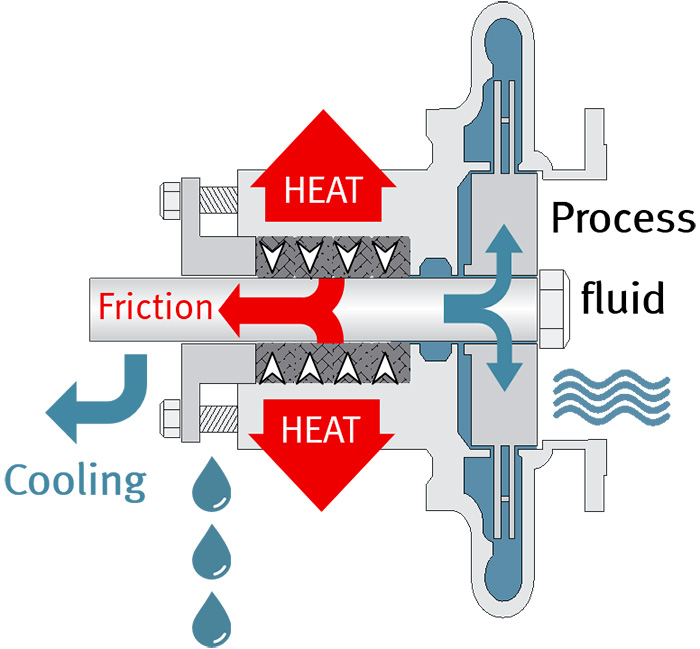
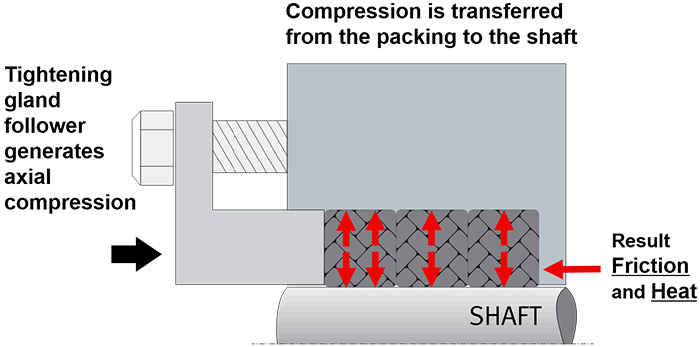
- The baseline drip rate can no longer be controlled through normal gland follower adjustments.
- The stuffing box/ambient temperature differential increases dramatically relative to the baseline reading taken when the packing was first installed (+25 percent).
- The packing is extruding from the back of the pump.
- The pump is shut down for maintenance, and the packing shows signs that the material is becoming hard or brittle.