This column is about the most common mistakes pump end users make daily. It is also about how to avoid these mistakes and how to fix them. I learned these lessons the hard way. When I entered the pump industry four decades ago, I wish someone had given me a list of common mistakes to avoid. Hopefully, I can impart some pertinent knowledge, practical tips and rules of thumb that will help the next generation of pump engineers, technicians, mechanics, operators, buyers and salespeople. This column is not based on scientific, industry or government studies. It will be an ongoing compilation based solely on my personal pump industry experience throughout the last 43 years. My experience is not with all pumps, in all industries or in all applications. However, I believe there is much to learn for anyone who works with pumps. My goal is simple. If I can prevent one person from destroying expensive equipment and—more important—causing an injury, then my mission will be complete.
Ignoring the IOM
The most common pumping mistake is not reading or following the instructions. For every field problem on which I have been asked to consult, the problem could have easily been avoided if the end user read the instruction and operating manual (IOM). Actually, many of the top 20 mistakes could easily be avoided by simply reading and following the IOM before installing and starting the pump. Listing this as the top mistake may seem silly. Many professionals in our industry think reading the instructions makes them look uninformed. I still highly recommend reading the IOM, even if other personnel do not.Operating the Pump Backward
The second most common mistake is operating the pump in reverse rotation—basically, running it backward. This occurs when a pump should operate clockwise (CW) but it operates counterclockwise (CCW) or vice versa. I see this occur at least once per month. For pumps with no way to prevent the impeller from backing off—such as American National Standards Institute (ANSI) pumps with threaded shafts and impellers—this is a major issue.ANSI Pumps
By design, ANSI pumps have no key, nut or pin to prevent the impeller from unscrewing from the shaft when rotated in the wrong direction. Between a nanosecond and a millisecond after the motor is started, the impeller will begin to unthread. It will back off the shaft threads, consequently making the rotating element longer. Then it will drive itself into the casing. The impeller backs off because of the principles of inertia and momentum. With apologies to my hero Isaac Newton for oversimplification of his first law of motion, the basic principle is that a mass at rest tends to stay at rest. The shaft turns, but the impeller will offer some initial resistance or inertia, which starts the unthreading process. In the best case scenario, the driver—usually an electric motor—trips on overload in about one second but not before the impeller is irreparably damaged (see Image 1). When this occurs, the impeller—an expensive and intricate casting that was dynamically balanced to International Organization for Standardization (ISO) G 2.5 standards and specifications—friction welds parts of itself into the casing. The precise curvature and geometry of the vanes that would have yielded hydraulic efficiency are destroyed. The balance will be out of tolerance, and the runout measurements on the vane tips will be totally out of specification. The vane height will also be heavily compromised. At least once because the driver did not trip out, I have seen a pump torn from the foundation, and the schedule 40 steel discharge and suction piping ripped apart.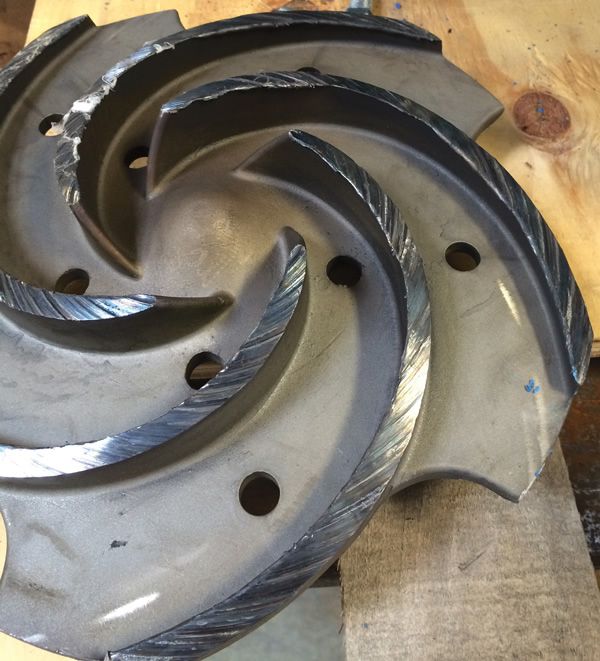
- Check directional rotation
- Complete final check of the impeller clearance setting
- Conduct the field alignment from driver to pump
- Set the cartridge mechanical seal