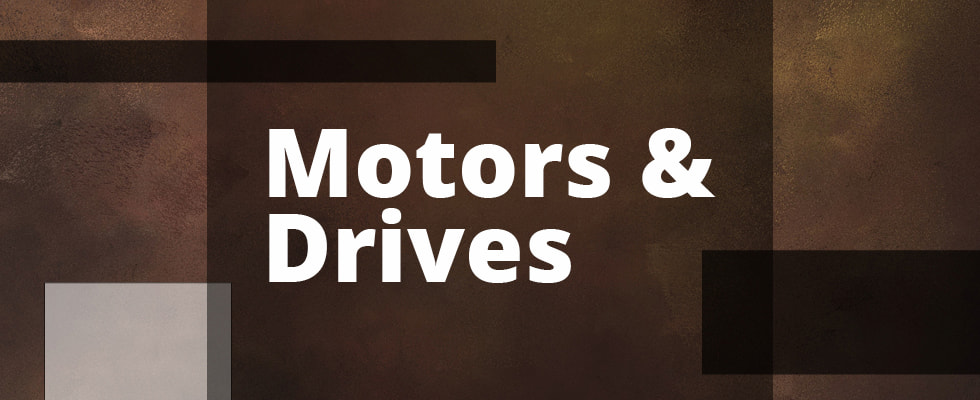
Variable frequency drives (VFDs) are mechanical drive systems used to control alternating current (AC) motor speed and torque by varying motor input frequency and voltage.
VFDs are commonly referred to as adjustable speed drives, adjustable frequency drives, AC drives, microdrives and inverters. A typical VFD has six diodes to direct the flow of electric current.
VFDs have certain benefits over regular speed drives. For example, VFDs allow adjustment of the power supplied to the machine to match the system requirement of the driven element.
This ability to precisely adjust and match power to the system requirements can result in other benefits including greater process control, energy conservation, improved efficiency, lowered noise levels, reduced stress on machines and extended machine life. VFDs are able to customize the frequency and voltage based on the motor’s load. Because of this, as the motor speed requirements fluctuate, so can the power from the VFD.
Power is input into the VFD at 60 hertz (Hz), which is the standard cycle frequency in the United States. The VFD can then adjust the speed of the motor downstream. The VFD acts as a kind of middleman between an upstream power source and the actual motor.
Determining the rpm of a VFD is critical to adjusting the power to match the system requirement, which can result in process control and energy savings.
The actual frequency divided by the potential frequency = X divided by the rpm on the machine nameplate
Plugging in example numbers, the equation might look like this:
50/60 = X/1,800
Equation 1
Calculate the RPM of a VFD
In order to calculate the rpm, locate the 1X frequency on the spectrum. Equation 1 shows how to calculate this.
It is also important to remember that the rpm on the machine nameplate—although likely a rough gauge of the machine’s rpm on a regular speed drive—will likely be incorrect for a VFD, which is why this equation is important.
Elaborating on this further, in the above equation, the 50 is the power on the VFD’s control panel. The 60 is the standard cycle frequency, and the 1,800 is the rpm on the motor nameplate. Solving for this equation will give you 1X or the rpm of your VFD.
Because we must know the relationship of the frequencies to the 1X frequency of the machine, it is essential that we correctly identify 1X. If 1X is not correct, your machine diagnosis will also suffer.
Synchronous vs. Asynchronous Motors
To calculate the rpm of a VFD, you will also need to know the difference between synchronous and asynchronous motors.
It is important to know that asynchronous motors (also referred to as induction motors) have “slip,” so the above formula only provides a ballpark speed used to precisely locate 1X in the vibration data. Slip refers to the discrepancy between the rotational speed of the stator field and the somewhat slower speed of the rotor. The amount of slip can vary, depending on the load the motor drives, as well as the resistance of the rotor circuit. A typical percentage of slip is between 0.5 percent and 5 percent. Although asynchronous motors have slip, they are less expensive to manufacture, which is one of their benefits.
Synchronous motors, on the other hand, have a special rotor construction that allows them to rotate at the same speed—thus, in synchronization—with the stator field. There are two basic types of synchronous motors:
self-excited or switched-reluctance directly excited
The rotor in a synchronous motor may still receive current, but it will generally not be by induction. Additionally, the more poles a synchronous motor has, the slower the motor will turn, which makes it a more expensive motor to manufacture. Some benefits of synchronous motors, however, are their ability to achieve precise timing as well as greater energy efficiency.
To reiterate, to calculate the rpm of a VFD, the following is required:
- the number on the VFD’s control panel
- the standard cycle frequency
- the rpm on the motor nameplate
With these three numbers, a user will be able to find 1X and, thus, the rpm of the VFD.
Read more motors & drives content on Pumps & Systems by clicking here.