Make sense of manufacturer materials and the sales process.
Iwaki America
06/07/2018
There are multiple reasons that facility managers, process engineers and maintenance personnel choose air operated double diaphragm (AODD) pumps for their facilities and processes. A few include the pump’s ability to improve downtime due to issues such as leaks or diaphragm ruptures, which cause more maintenance intervention and increase the overall total cost of ownership. Some of the main reasons for AODD selection include:
- Low total cost of ownership: From initial acquisition cost to service and repair, AODD pumps are often lower cost.
- Portability: As long as there is an air-line drop and an inlet and outlet hose, an AODD pump can be used most anywhere in a facility or within a specific process.
- Shear sensitivity: The pump usually will not shear or separate the fluid being pumped.
- Submergibility: The pump can be fully immersed as long as the exhaust is piped above the liquid line.
- Deadhead and run dry capability: If the discharge outlet is blocked or stopped or if the supply of fluid is empty, the pump is designed to continue cycling without damaging the pump or the product being transferred.
- Sealless design: There are no seals to replace due to excess heat or if the pump were to run dry.
- Self-priming: The pump will draw fluids into the pump in either a dry (unprimed) or wet (primed) application.
- Variable flow control: Because AODD pumps are considered 1:1 ratio pumps, the amount of the air inlet pressure going into the pump is directly related to the fluid pressure at the discharge outlet of the pump.
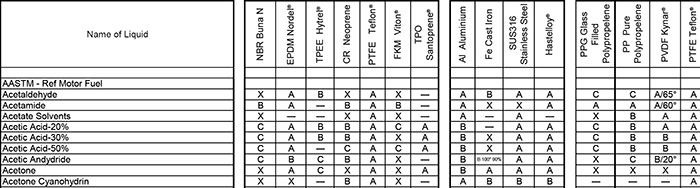