Vibration changes can indicate cracks in pump rotating components, which can cause severe malfunction and failure.
03/13/2014
Crack-related catastrophic pump failures have been reported worldwide. Cracks are often reported in rotating components. A propagating crack in a pump shaft or a rotor assembly can affect pump vibration. These cracks are primarily detected based on the changes in 1X, 2X and sometimes 3X vibrations. Many mechanical or thermal causes can initiate a crack. Afterward, the crack growth could be driven by a combination of thermal and mechanical loads, particularly those causing alternate cyclic stress in the shaft. A crack is often influenced by mechanical stresses (particularly bending stresses), thermal stress fields and liquid pressure in the cracked area.
Crack Causes
For many pumps, high mechanical and high thermal stresses can arise in the geometric transition zone. Thermal fatigue is the reason for many crack initiations. Some cracks originate from surface micro-cracks, which can be caused by manufacturing or operational processes. On the shaft surface—especially where the shaft or sleeve contacts the liquid—the maximum stress can be expected because of the maximum thermal gradient and/or the maximum bending effect. Even if a shaft sleeve is used, high stress could still occur on the shaft surface. The location of the thermal boundary zone in a shaft is critical. If the thermal boundary is located above the crack, the tensile stresses develop in correspondence with the crack and can further its opening. If the thermal boundary is below the crack, the compressive stresses can generate forces that could close the crack.A Cracked Shaft
A cracked shaft represents a severe malfunction in a pump and should always be considered dangerous. A cracked shaft may result in:- A stiffness reduction, resulting in rotor anisotropy
- A shift of the elasticity axis (the rotor bows), which affects the balance state
1X, 2X & 3X Vibrations
A propagating crack generally produces a bow, which can be magnified by mechanical or thermal stresses and also by the liquid pressure penetrating the two crack faces if the cracks contact the pumped liquid. This bow can generate high amplitude 1X vibrations. The 1X vibration components are generated by the crack-related bow and by the mechanical, thermal and hydraulic unbalances. The 1X vibration increases consistently when the unbalance is in phase with the bow. This situation is most likely to occur because the crack usually originates from micro-cracks in which the maximum stresses are developed.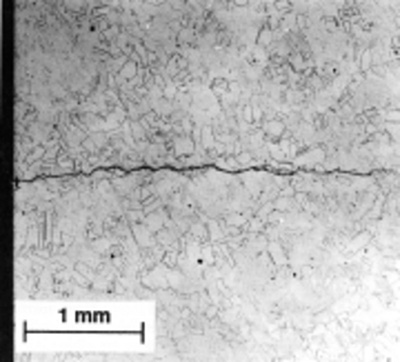
Crack Detection
The dynamic load, the stiffness and the damping of the pump bearing and seal can show a high sensitivity to small differences in the design, manufacturing details and tolerances, assembly (assembling tolerances), and operational effects (such as degradation). The dynamic responses and vibration measurements of similar pumps can differ because of these effects. A theoretical prediction of the exact vibration behavior, such as the vibration amplitude, of a cracked shaft would not be suitable or possible for crack detection. Trending can be the best tool for this purpose. Increases of 1X, 2X and 3X vibration measurement amplitudes from their acceptable regions can help detect a crack. Many other vibration indications, which can be monitored, also exist. For example, the vibration measurements can be useful at transient conditions. The starting and the run-down transients of pumps are often too fast to allow the collection of significant data. However, high 1X and 2X amplitudes (compared to normal levels) could be the most significant indicators of a crack. The vibration measurements can be positioned far from the crack. The vibration amplitudes will increase in all locations of a shaft. Usually, the vibrations in different parts of a shaft may be at least 15 percent of its maximum (located close to the excitation).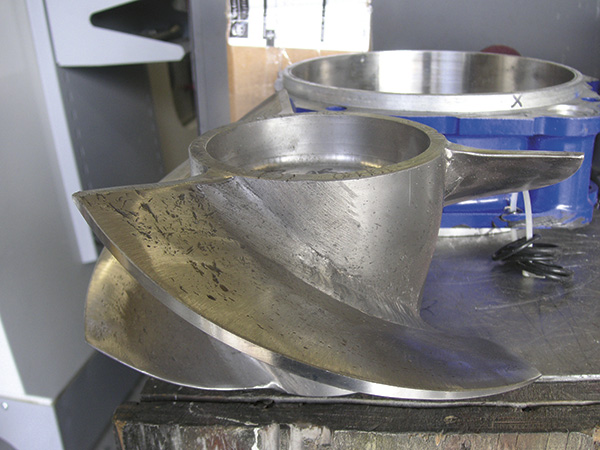