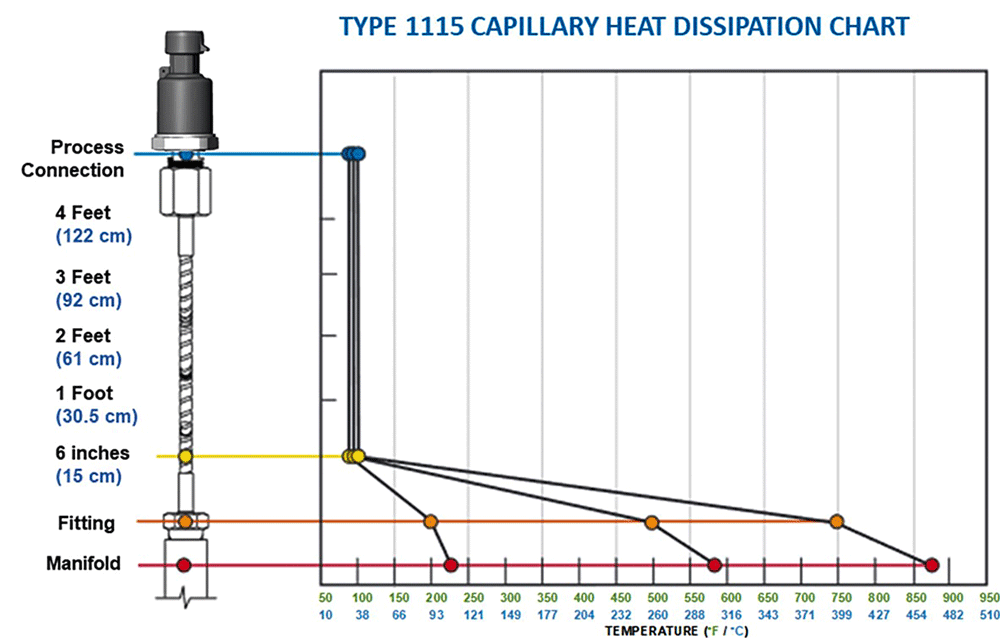
Pressure gauges are often used in challenging environments where they could be exposed to extreme temperatures that may damage them or impact their accuracy. These extreme temperatures can come from a variety of sources such as the surrounding environment (ambient temperature) or the temperature of the process media being measured (media temperature).
How does a user minimize the effects of temperature on the instrumentation and protect pressure gauges from damage?
This article will describe the effects that temperature can have on pressure gauges and their performance as well as how users can counteract those impacts. When the word instrument(s) is used, it refers to pressure switches and transducers.
Temperature Effects on Pressure Gauges
Pressure gauges are rated for use in a specific temperature range. Using gauges in temperatures outside of their range can lead to damage, depending on their design and construction.
Discoloration of the dial and hardening of the gasketing may occur as ambient or process temperatures exceed 150 F. Non-liquid-filled gauges with standard glass windows can withstand continuous operating temperatures up to 250 F (121 C).
Liquid-filled pressure gauges can withstand 200 F (93 C) but glycerin fill and acrylic window will tend to yellow. Gauges with welded joints will withstand 750 F
(400 C), 450 F (232 C) with silver brazed joints for short times without rupture, but other parts of the gauge can be destroyed, and calibration may be lost.
For continuous use and for process or ambient temperatures above 250 F
(121 C), a diaphragm seal, capillary or siphon is recommended. A standard dry gauge can experience slowed point response time in low temperatures.
Ambient temperature
Ambient temperature is the air temperature that is measured at the gauge or instrument. A gauge or instrument that is mounted alongside a heat source like an oven is a good example of where elevated ambient temperature can occur.
Alternatively, if an instrument is mounted outdoors in Siberia in the winter, the instrument can see temperatures down to -78 F (-61 C). Both extremes should be a call to action to protect the instrument.
Process temperature
This is the temperature of the media directly touching the wetted parts of the instrument. With a pressure gauge that includes the process connection, the sensing element and, in most cases, the bourdon tube and tip.
With an electronic product like a transducer, this usually involves the
process connection and the sensing element. Like ambient temperature extremes, temperatures beyond what is recommended by the supplier should be a cue to take action to protect
the instrument.
Storage temperature
Users should always adhere to manufacturer storage temperature recommendations. Most instruments should be stored indoors in a clean,
dry, well-ventilated area, avoiding condensation and humidity. Storage temperature limits can range from -40 F
to 250 F (-40 C to 121 C), depending on
the configuration.
Temperature Compensation
When high or low temperatures affect pressure instruments, manufacturers may use temperature compensation to counteract the effects. This process differs depending on the instrument used.
Mechanical pressure gauges
Solid front type gauges typically provide temperature compensation with a rear elastomeric flexible diaphragm or bladder. This allows internal case pressure to expand or contract within the gauge.
For solid front gauges with a temperature compensated diaphragm/bladder, accuracy at temperatures above or below the reference ambient temperature of 68 F (20 C) will be affected by approximately 0.4% per 25 F. When additional compensation is required, a temperature-compensated movement further reduces temperature error. The temperature compensator reduces errors caused by temperature to less than 0.005% per degree Fahrenheit of temperature change.
Electronic pressure instruments
The process of temperature compensation for electronic pressure instruments involves measuring the internal temperature and compensating the output signal to offset the effects of temperature.
In applications where temperature changes take a long time (hours, days) even if they are large, it is more likely that a consistent and equalized temperature profile is achieved and the temperature compensation is working well.
In applications with large changes in media temperature that happen quickly while the surrounding environment stays the same, a variety of solutions can mitigate the extreme temperature effects.
Mitigating Temperature Effects
There are a few common solutions for instrument problems stemming from high or low temperatures, including:
Mounting the instrument remotely
Users can install the instrument away from the process media or away from an ambient heat source with capillary to protect it from high or low temperatures. A gauge pipe mounting bracket is a convenient option when remotely mounting the gauge.
Capillary helps lower (or increase) the temperature of the media by minimizing the media volume while maximizing the surface area exposed to the surrounding (ambient) temperature. A few inches/centimeters can bring the media temperature back to a safe operating range.
Mounting the instrument directly
Finned siphons, coil or pigtail siphons, when attached to the instrument, can curtail temperature in steam applications. A pigtail siphon is used for vertical mounting whereas a coil siphon is used for horizontal mounting.
Prior to installation, the siphon loop needs to be filled with water. The water acts as a barrier to protect the instrument from the elevated temperature and the harmful effects of water hammer, which is typical with steam applications. Diaphragm seals or isolators, when required, can also dissipate process temperature.
Now that users understand the impact that media temperature can have on measurement instrumentation, they can research the solution that’s right for the application to help ensure the equipment is protected.