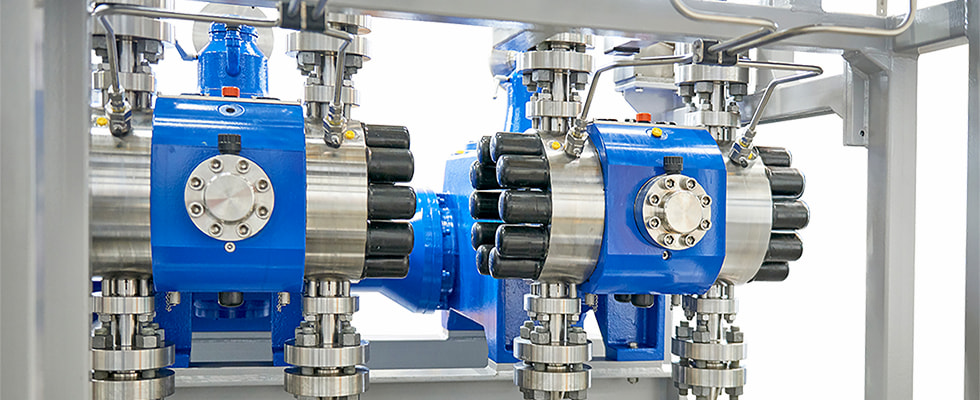
How big is it and how much does it weigh? Those are some of the questions oil and gas industry leaders have when selecting equipment, particularly those for offshore rigs. And for pumps, which are integral to so much of the process for upstream and downstream applications, space and weight constraints are critical.
Many users—not just in oil and gas operations but also in chemicals or synthetic processes—use multiple pumps to ensure the flow rate they need. The duplex pump head pump has been a traditional choice for many oil and gas companies. However, they may be compromising on efficiency, space and weight.
By choosing double-acting double diaphragm pumps (DADD) instead, operators can realize the benefits of a smaller footprint, lighter load and higher flow rate. Some DADD pumps have a double-acting hydraulically actuated pump head designed to accommodate applications such as glycol, methanol, polymer and hydrocarbon condensate up to 500 bar and 150 C.
The pump head allows users to double the flow capacity of a single traditional diaphragm head. In addition, only one motor and gear box module are required to drive the equivalent of two pump heads.
Cost & Space
Operators can gain multiple benefits by swapping out for a double-headed pump or using one from the beginning in new builds or expansions.
Whether investing in a DADD from the get-go or updating a current system, oil and gas applications can ultimately save costs over the total life cycle of the system while getting the same or higher flow rate than two pumps.
Of course, there are initial cost savings for buying only one pump instead of two or more. However, when taking maintenance and the service equipment required into account, the total cost of ownership over the product’s life cycle also provides savings, especially given the pump’s long life span.
A sole pump also means less maintenance with more uptime. Using the proper, genuine parts can extend product life and ensure the highest performance efficiency. In many instances, a new double-headed pump can fit into an existing setup with no need to overhaul a system to reap the benefits of a more efficient pump. Instead, end users can upgrade one component at a time when the timing and investment works best for them.
Using hydraulically actuated double diaphragms without sealing gaps provides no risk of the pumped liquid leaking, thereby eliminating the associated safety risk. In addition, wear on the plungers is minimized, reducing wear-induced leakage.
The costs associated with the DADD can ultimately save money, both directly and indirectly with increased uptime.
The challenges of oil and gas equipment mean considering the limitations, including space, when designing components. More compact pumps mean better space usage, particularly in deeper water and higher-pressure environments.
For existing setups, having a smaller unit allows for more options without having to reroute the system. These are often metal-based, making it more difficult to change the pipework to accommodate different products, let alone need more than one.
In addition to space, there are weight considerations when it comes to equipment. A single double-headed pump weighs less than two single-headed pumps combined or the traditional duplex pump head pump. This gives operators a similar flow rate but with less weight overall.
Space and weight considerations are top concerns for oil and gas operators, and there are now options on the market to save with both, along with other factors like energy efficiency.
Durability & Safety
If well-maintained, the double-headed pumps have a long life, with some known to still be running after 40 years.
Offshore oil and gas platforms must endure harsh and extreme conditions—from massive storms, temperature swings and more—without missing a beat. They must be built with high-quality materials and reliability to ensure a long life.
Top-quality DADDs can run 24/7 requiring minimal operator interaction. The absence of sealing gaps removes the possibility of pumped fluid leaking, increasing operation and operator safety.
The diaphragm technology is designed to provide hermetically sealed handling of hazardous and dangerous chemicals. The inherent accuracy of diaphragm technology also reduces raw material costs and increases pumping efficiency in high-flow, high-pressure applications.
Quality and reliability pave the way for longevity and security. With the proper upgrades and maintenance, these components can last for decades, in turn reducing waste and cost overall.