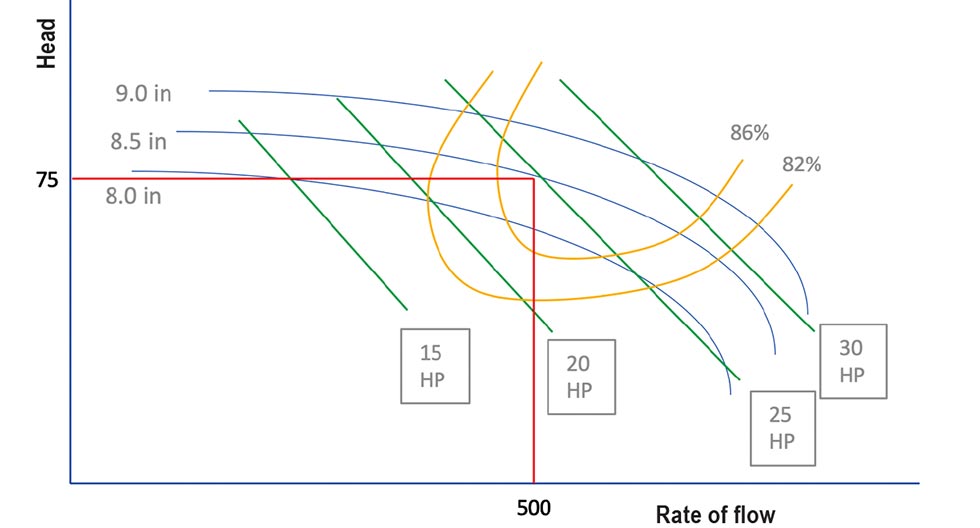
All successful pump deployments begin with flow and head requirements. Using pump curves enables the right pump design, motor horsepower (hp) and impeller size to be selected. Once properly specified and designed, well-maintained pump systems can provide efficient production for decades of useful life.
Years into the future, however, the pump manager’s challenge is to determine whether the original design is still appropriate for current demands. Keeping an eye on when efficiency has declined, or replacement is warranted, is also important. Using the initially installed power sensors to protect the pump can be a key to unlocking these insights.
What Does Pump Power Sensor Implementation Look Like?
Power sensors, or load controls, are typically installed to protect pumps and their motors. A large global manufacturer of chlorine and caustic soda implemented a reliable solution to its pumping concerns by installing power sensors on 60 pumps. The sensors were installed in a motor control cabinet, away from environmental hazards, and include two trip points, a low trip indicating impeller breakage and a high trip set for motor jam occurrences. The solution, which measures motor hp, proved to be accurate in detecting impeller breakage. This sensitivity is key to ensure ongoing safety and efficiency for this manufacturer.
Finding the New Location on the Pump Curve
There are benefits beyond safety and motor protection for these sensors. Image 1 is an example of a pump curve. For the required flow of 500 gallons per minute (gpm) and head of 75 feet, it shows that a best efficiency point (BEP) with corresponding recommended motor hp can be located on the curve. In this example, the BEP would dictate a 25-hp motor.
By leveraging the power sensor data already captured, the pump manager can compare the original hp demand expectations with the measured, or actual, hp requirements. The difference between the original theoretical value and the measured hp value offers insight into process improvement.
In the case where the actual hp measured is much less than the specified hp of the motor, it may be oversized. This may be due to several factors including:
- addition of new pumps in parallel functions or improvements in piping efficiency
- business or process changes that reduce operating head or flow requirements or overall demand
- cautious or conservative initial sizing during the planning process
- changes in operating temperature or viscosity
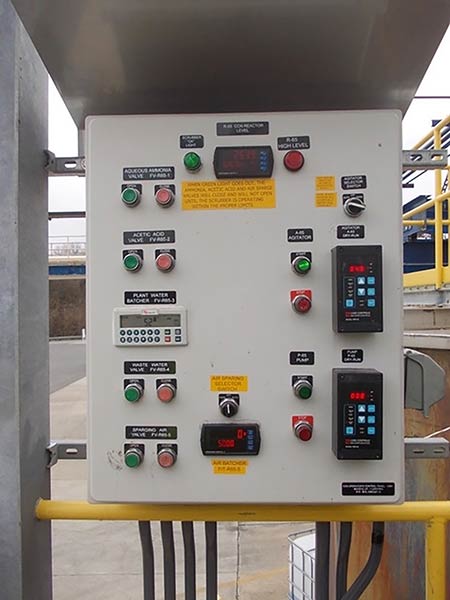
Conversely, the motor may be undersized, as indicated by the measured hp at or above specified motor hp. This may be due to changes over time such as:
- business or process changes that increased operating head or flow requirements or overall business demand
- changes in operating temperature or viscosity
- overly aggressive cost-savings approach when initially sizing the pump motor
- increased wear or impending maintenance needs
- spikes from seasonally high demand that were not originally forecasted
Leveraging Data to Increase Efficiency
With industrial pumps accounting for as much as 25% of the world’s energy consumption, the potential for impact and savings by highlighting oversized motors is sizable. Industry analysts estimate that up to 75% of installed pumps may be oversized, many by as much as 20%.
It is common to see a few large, oversized pump motors contributing to this expense issue. Replacing them with more properly sized motors can offer a payback in a few months. Scheduling this type of motor swap in lieu of needed maintenance can be a smart alternative.
The reduced life of an underconfigured pump motor can also be a problem. Overheating, excessive wear and potential failure can cause expensive downtime and maintenance headaches. Outages, whether planned or unplanned, can cost valuable productivity and missed revenue. System failure can also lead to substantial cleanup costs and potential safety risks in the event of a catastrophic event.
Pump operating costs can account for up to 25% of a process manufacturer’s expense budget. Wringing all the efficiency out of this system is vital to expense management and process efficiency. By using the data already available from pump power monitors or load controls, smart pump managers can address this efficiency challenge while improving their manufacturing process and reducing risk. A forward-thinking pump management program should leverage the data already captured by pump power sensors and pump curves to determine ideal motor sizing and cost savings potential.