Pumping Prescriptions
Pumping Machinery LLC
10/18/2016
The objective of this month’s column is to show end users how to hydraulically evaluate their pump systems and determine the power required for the drivers to move the desired flow through the piping/process. A process designer usually begins a project by determining how much flow must be pumped from point A to point B. The details of the piping, required pumps, coolers, filters and instrumentation are determined based on the flow.
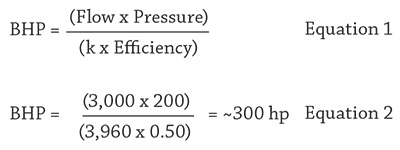
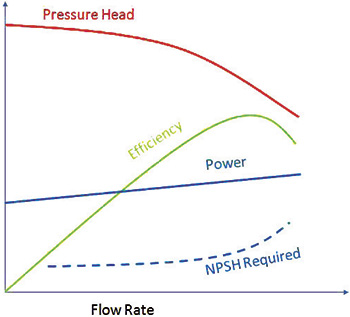
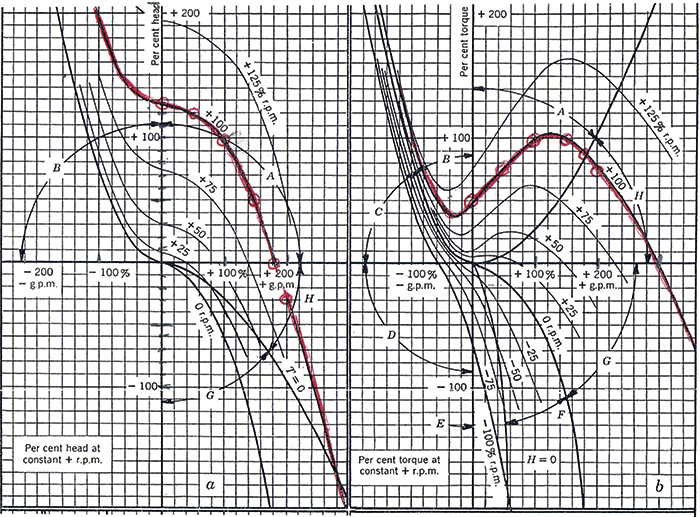
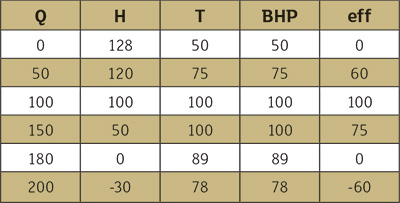
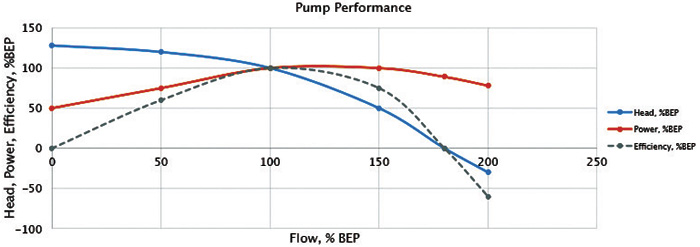
To read more Pumping Prescriptions columns, click here.