The drive for operational efficiency, optimization of assets and adherence to the International Standards Organization (ISO) 14001 Standard for environmental management systems and ISO-50001 standard for energy management systems must always be balanced against the bottom line. However, it is fair to say in some cases this can lead to short-sightedness when it comes to selecting sealing solutions, with lower cost at point of purchase taking precedence over total cost of ownership. Mechanical seals have been on the market for around 80 years, and while pump design has remained largely unaltered, sealing technology has evolved over time. This has resulted in advances in reliability, operational efficiency and environmental sustainability.
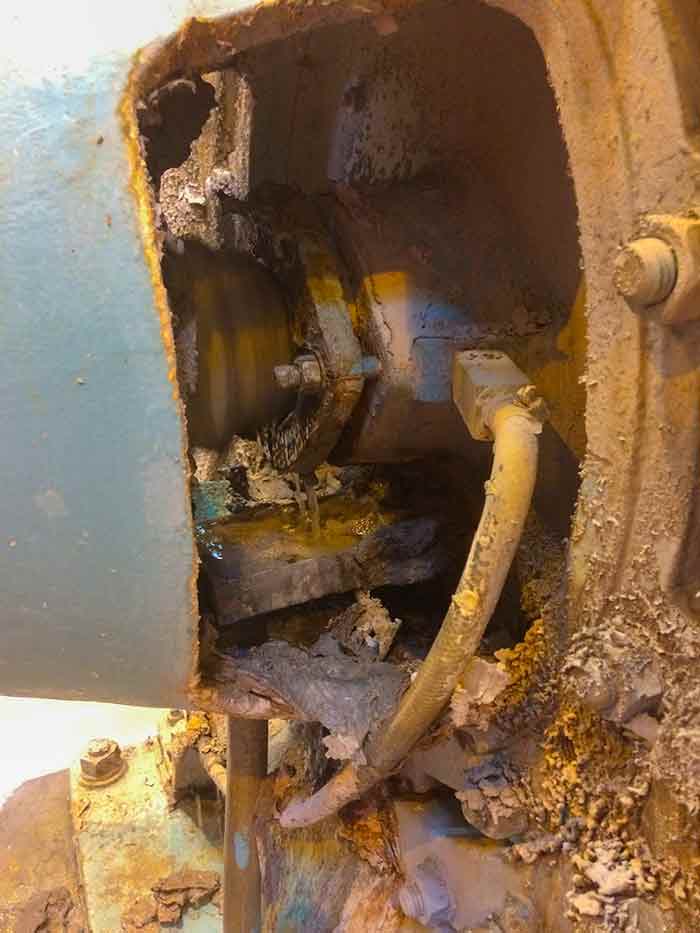
Excessive Wear
Leakage, product loss and bearing contamination that leads to premature failure are three common issues with traditional seals. There is no reason why bearings should not last for their full predicted lifespan, which is typically calculated at roughly 15,250 operational hours. Leakage caused by inefficient sealing is the simple reason why they do not last. With research showing that water contamination of just 0.002 percent—a single drop—in a bearings chamber can reduce bearing life by almost half, it is easy to see why bearing failure is one of the most frequent causes of pump malfunction. The cost of regularly replacing damaged seals and bearings accumulates over time and can escalate if the pump shaft suffers wear damage and must be repaired or replaced. Another key cost, which is often overlooked, is the number of hours demanded to maintain, repair and replace these components.Guaranteed ROI
A shrewd purchaser wishing to guarantee a good return on investment (ROI) compares different types of seals to determine what is best for their system and application. Dual mechanical seals are one choice. Mechanical seals operate best with a seal support system, which recycles the flush water required to keep seal faces cool and lubricated via a continuous loop system. The initial outlay will be higher but this will be offset by a number of cost-saving benefits:- No direct contact with the pump shaft means it is not exposed to possible damage. Leakage beyond accepted industry norms is virtually eliminated and so is the premature seal failure that leads to product loss, bearing contamination, equipment breakdown and repeat repurchasing of parts.
- Mean time between failure (MTBF) is improved and unscheduled downtime is less likely.
- Dual mechanical seals can be retrofitted onto assets and require virtually no ongoing maintenance.
Environmental & Cost Advantages
The pressure on companies to reduce the impact of their operations on the environment has never been greater. The advantages of including a seal support system that recycles flush water are significant both financially and environmentally. Most seals require cool, clean liquid to provide lubrication and prevent overheating and dry running. This is often injected from an external source, and the majority of it can go to waste, either flowing down the drain or evaporating off at the end of the cycle. In a typical application, where water is measured for one minute, around 1.6 to 3.17 gallons of flush water is required. In continuous operation, that amounts to roughly 0.8 to 1.6 million gallons per year for each seal (or pump). Add up the number of pumps involved to calculate the scale of waste.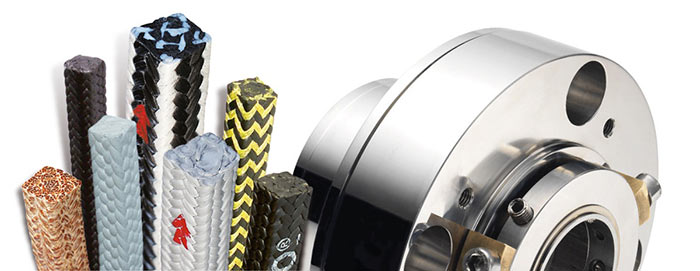