Harsh conditions vary from industry to industry. Severely corrosive chemicals might be considered harsh, or incredibly abrasive mediums might be considered harsh. External environments may be harsh to equipment from the outside. The atmosphere may be corrosive or just physically demanding. Facilities using dense phase systems also understand the abrasive nature of something seemingly as simple as baby powder being pneumatically conveyed. Almost any solid material conveyed by air or gas is extremely abrasive. Industries that possess some of the harshest environments are mining, pulp and paper mills, and steel mills. In mining, crushing rock and then moving it in a slurry is definitely abrasive. Pulp and paper mills combine cooking acids, steam and wood chips. The environment is chemically corrosive, and parts of the mill have scaling and abrasion. Steel mills require 35,000 gallons of water to produce one ton of steel. This water picks up steel scale, slag and many impurities, which plays havoc on pumps, valves and all types of equipment. The water within a steel mill is recycled and reused numerous times. There are harsh conditions found in almost every type of processing facility. In many process facilities, there is a goal for standardization to minimize training requirements, reduce material stocking costs and use the best products for the processes. When the majority of the process is not harsh, standard products can be used with effectiveness. The dilemma occurs when standard pumps and valves are used in these harsh environments. In a majority of the cases, these products will not have the survivability and reliability desired by the user. An example would be a chemical manufacturer using ball valves and butterfly valves for shut-off and control of a clean chemical process. If this manufacturer uses lime slurry for pH control, then these standard products would not be ideal and would likely lead to high maintenance costs and frequent repair. Ball valves, for instance, can be adapted to have better survivability in slurries by adding hard coatings, changing Teflon seating to metal scraping seats, adding body cavity fillers and flushing ports. But by the time all of these modifications are made, the valve is no longer a standardized product, and the cost of the valve may be 10 or 20 times the cost of a standard ball valve. A better solution may be to look for valves and pumps that have been specifically manufactured to handle abrasives and are known for their ability to survive in these conditions. By no means does this suggest that ball valves or butterfly valves are poor products. They are fantastic products in the right applications.
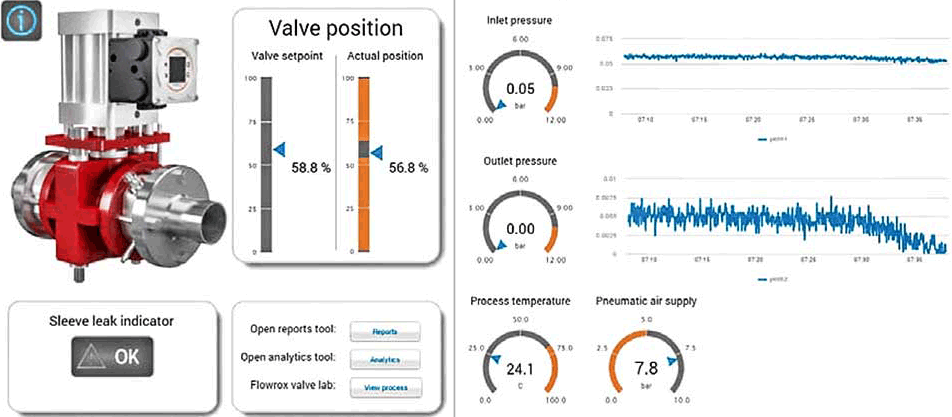
Material Selection for Abrasives
When dealing with abrasive mediums or mediums that scale, there are some ideal characteristics to focus on when selecting the correct valve or pump for the application. If it is a valve, it should be full port. Avoid any type of valve that creates a restriction and introduces additional velocity. Increased velocities will increase wear to valves, pumps and piping. When selecting either a valve or a pump, select a product that minimizes void areas, pockets or cavities. These areas are collection points for scaling and solidification of solids. Also, valves and pumps that have self-cleaning properties may be beneficial, such as a peristaltic pump. These pumps employ a rubber hose that is compressed to push the materials forward. Since the rubber hose is constantly being flexed, it helps to break any scale or buildup on the inner layer of the hose. In addition, this style of pump has no areas for solids to accumulate and cause future issues or problems. In mining, slurry concentrations may reach up to 85 percent solids. When moving a slurry this thick, special care must be taken to ensure the medium keeps moving. By creating too much velocity, almost all components in the flow stream will show signs of increased wear. However, if the process does not create enough velocity to keep solids in suspension, blockages will occur. Often in pumping circuits, the piping design is at fault for causing problems. At one mine in Mexico, a peristaltic pump was moving an 82 percent slurry flow from the bottom of the thickener and was having issues. A pump manufacturer sent a service team on-site to diagnose the issues. On the discharge side of the pump, the piping travelled approximately 20 feet and then the piping made a 90-degree turn through an elbow. In high solid slurries, sharp turns should be avoided. Changes in piping direction should occur with wide sweeping turns and be more gradual. Another instance happened in South Africa where the piping that came out of the thickener was 6 inches in diameter, then reduced to 4 inches before going into the pump. With the head from the thickener into the 6-inch piping and the flow rates required, the piping was too large to keep enough velocity to move the material to the pump. When the flow velocity decreased in the 6-inch piping, the solids began to settle out and made blockages in the piping. Diluted water had to be introduced to a thickened slurry to get product moving again. A pump manufacturer recommended that the piping be reduced to a 4-inch diameter to keep enough velocity and keep the slurry in suspension. There are two directions that can be taken in material selection for valves and pumps in abrasive slurries. One is to add hardened coatings to the inner parts in contact with the fluid. Commonly used coatings are stellite and tungsten carbide. Even ceramic materials can be effective to deal with abrasion. The other, less expensive option is to use rubber or polyurethane materials. In this case, the abrasive particles bounce off the rubber and cause minimal damage. Due to the wide range of rubber materials, rubber can sometimes be more effective for the combination of corrosive and abrasive slurries. For instance, an ethylene propylene diene monomer (EPDM) material can withstand many chemicals and has good abrasion resistance as well. Two of the most effective materials when dealing with abrasion are natural rubber and styrene butadiene. Centrifugal, progressive cavity and diaphragm pumps all use rubber elements such as rubber wear linings, diaphragms and stators to combat abrasive wear.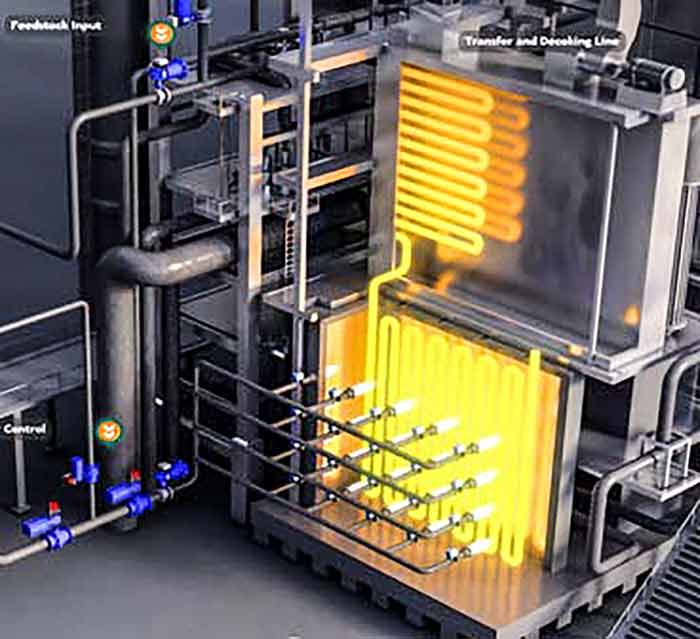
IIoT Connecitivity & Predictive Analytics
Today with Industrial Internet of Things (IIoT) connectivity, it is possible to add digital outputs to almost any piece of equipment including pumps and valves to track all types of information. Machine learning tracks new condition readings and begins to report anomalies observed from the digital or analog inputs that are trending outside the new condition readings. There are significant upsides to using IIoT monitoring systems equipped with predictive analytics to reduce operating costs and improve productivity. Some companies are reporting that they are gaining as much as an additional month of production per year. Companies employing IIoT equipment monitoring often perform in the top 25 percent when compared to their peers. A simple example of monitoring pump condition is vibration monitoring of both the motor condition and main bearing condition. Vibration monitoring can pick up minute vibrations that may be indicating the beginning of bearing failure. If not caught and addressed, the complete bearing failure can damage the entire pump casing leading to significant repairs, costs and downtime. But repairing a simple inexpensive bearing early helps to reduce costs and downtime. Pumps are vital to almost all operations globally, and they are often the most under-analyzed and least connected devices in production operations. The ability to capture this type of information allows maintenance teams to transform from reactive maintenance to proactive maintenance. A sizeable production facility can save millions in maintenance costs and show healthy gains in productivity. A means to further improve IIoT capabilities can be the use of digital twin imagery that can be accessed by smartphones, tablets and PCs anywhere. This allows personnel to access necessary data at a moment’s notice without needing to travel to a central control room. Personnel can be standing in front of a piece of equipment and see all the readings from that machinery.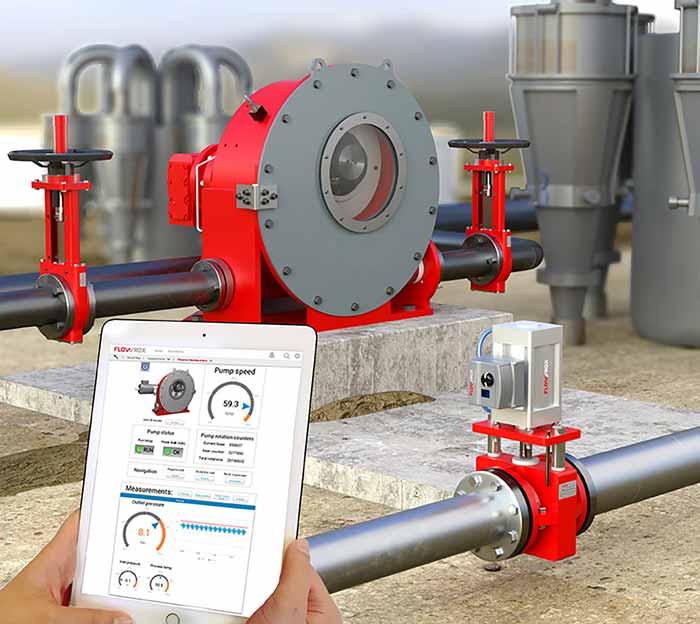