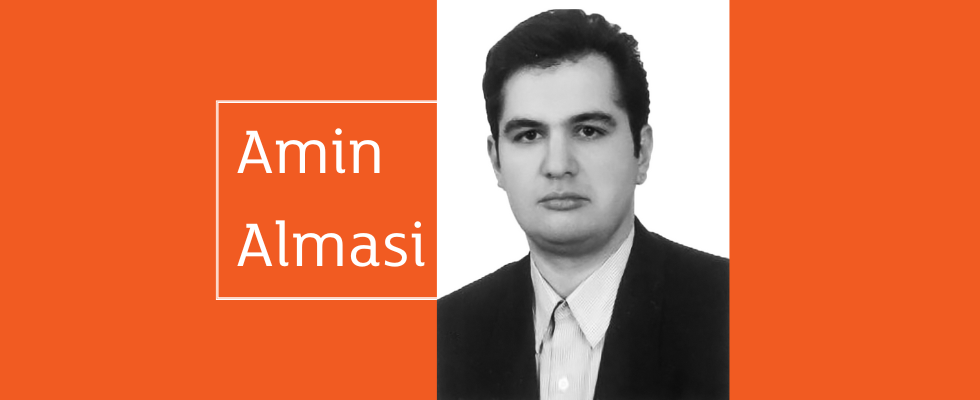
There has been extensive feedback regarding improvements needed for lubrication systems. Many failures and issues are traced back to the lubrication system, lubrication oil, grease feed or bearings. Proposals for improvements in lubrication systems, such as using modern and better lubrication methods or a high-performance lubrication oil, could be considered for the improvement.
The pump subassemblies and their components should often be redesigned for the serviceability limit stated by limiting deflection, fatigue, vibration, bolt slip, corrosion, etc. Feedback from actual operations is important for such assessments, improvements and redesigns. Fatigue, crack developments and fractures have often been the root causes of failures in pumps. Fatigue cracks usually develop at points of high stress concentration. These points may be caused by or associated with holes, bolt connections, welds (including stray arc fusions), defects in materials and local and general changes in geometry of parts and members. The cracks usually propagate if loading (cyclic/dynamic/repeated loads) is continued. Sudden changes of shape of a member or a component, especially in regions of tensile stress or local secondary bending, should be avoided.
One recommendation is to target infinite fatigue life for parts and pieces under cyclic or dynamic loads. This is particularly applicable for the redesign and redevelopment of parts and components of pumps failed by fatigue or cracking, or those that have suffered damages or problems while in operation. As a rough indication, for commonly used carbon steels and low alloy steels, infinite fatigue life refers to cyclic stresses (endurance limit) of below 25 to 45 MegaPascals (Mpa)(typical range). As cyclic loads and associated stresses are increased, the expected fatigue life is reduced rapidly. For instance, in a pump stand, when the cyclic stresses are increased 14%, 31% and 51% from the original optimum value by considering thinner and weaker sections and parts, the fatigue life is reduced from infinite life (considered optimum value) to 20 years, 10 years and five years of expected fatigue life respectively. By reducing cyclic stress only 31%, the expected fatigue life increases from 10 years to infinite life.
A major risk is these are just theoretical values with simplifications and assumptions. In practice, a pump part with a nominal fatigue life of 10 years might fail in a few months. The author’s recommendation is to stay in the heavy-duty, infinite-fatigue-life range as much as possible, unless the redesign would be expensive or excessively bulky.
Usually, small bits and pieces, such as small lines, auxiliary piping, vents or drains have been designed quickly with minimum attention paid to the details in the original design of a pump system. Too often, several complaints, or even failures, are associated with them, and they need to be redesigned for the next version or generation of the pump system. Sometimes thicker pipes and fittings (higher schedules) should be used or a better material selection may be needed, as corrosion is a major issue in those small sizes. Also, any impact or accident during installation, commissioning or operation might be detrimental to small sizes of piping and small parts.
Typically, any piece of equipment, even auxiliary ones, have different small details and complications. Consequently, the function of each should be considered if any change or improvement is planned. For instance, in a gearbox of a pump package, there was a complaint about ineffectiveness of the cap and O-ring of the breather, which needed to be redesigned. The gearbox had a breather located on its top. This breather allowed the release of internal pressure due to changes in the oil temperature. The O-ring and cap were used to prevent oil leakage during shipment. The original O-ring used was problematic, and it was replaced with a new one to improve the pump. The new O-ring is made up of two-piece rings connected by a strip to form a figure 8 shape. This case study shows the complexity and level of detail associated with the smallest parts of a pump.
Pumps are often designed with one or two sets of standards and codes but are intended to be sold in different markets worldwide. Those pumps ideally should have been slightly overdesigned for strength, fatigue, ultimate loads, maximum operating limits, etc. Pumps from major manufacturers are expected to be installed in different parts of the world and in different services with maximum commonality in parts and subsystems. This means the same pump will be assessed by different standards and codes in different operational and environmental conditions (fatigue assessments, operations, wind, seismic). Also, there might be different interpretations of standards. Third parties may impose conservative interpretations of the applicable standards and codes on those pumps.
The commonality of parts and pieces is extremely important. The point is, if a piece or subassembly is initially designed with some margins (slightly over-designed), say 8% or 12% (as rough figures) over original codes and standards, then the universal/common designs would likely pass all the above-mentioned predictable and unpredictable requirements and interpretations worldwide. The optimization and cost savings are important. However, the cost associated with slightly overdesigning some pieces and parts would be small compared to costs associated with disputes, risk of noncompliance and other potential problems. Excessive overdesign is not appropriate and not suggested. The case here is about slight overdesign compared to current design procedures based on codes and standards in the manufacturing location.
There have been cases where pumps were damaged during transport for relocation, repair or maintenance. Operators are keen to buy metallic transport baskets, skids or frames that would be a universal fit for different sizes and models of the same family of pump packages. There have been different designs of such transport baskets and boxes for different pumps. However, proper solutions need to be developed for many other pumps. These baskets, boxes and skids need improvements, as the design was often either not sufficiently thought through or not suitable.
Pump packages come in wooden boxes and temporary crates that get disposed. The next major step is to replace all disposable material with reusable metallic transport baskets and boxes, which would be operationally and environmentally beneficial. Operational data and process input from the client or purchaser side for the sizing and selection of the most appropriate pump are always necessary. Proper process and operational inputs from clients and consumers are required by vendors. Feedback from clients and their operations are important to improve pumps. Vendors and manufacturers need this feedback to improve and redesign pumps and solve reliability and operational problems. However, mandates from clients and third parties on matters which are essentially the vendor’s business are not often appropriate or productive.