Over-tightening, excessive speed and improper installation can cause a system to falter.
Garlock Sealing Technologies
10/16/2018
In many respects, troubleshooting and failure analysis of packing materials is similar to the investigation of a crime scene. A good investigator knows how to gather clues from many different sources and put them together to understand what has happened. A good troubleshooter uses the same information gathering method, familiarizing themselves with the sealing materials, the process equipment and the systems where they are used.
Start by Interviewing Witnesses
The troubleshooter should seek information from the people who work with the equipment on a regular basis. Seal installers, maintenance personnel, operators, process engineers and others can all shed light on potential causes of failure. Some key questions should be:- How is failure defined? Some examples include excessive leakage, overheating, high rate of flush water consumption, excessive friction load and blowout.
- Is this application the source of chronic seal failures, or was this an unexpected event?
- Were there any changes to the seal material, the equipment or the overall process that preceded the failure?
- Were there any system upsets or cleaning cycles that preceded the failure?
- Can you describe the installation procedure?
Gather Information About the Victim
Knowing the limitations of the sealing product is a key step. The acronym “STAMPS” will help remember the key elements to ensure the right packing is selected for the application.- S: Size. Is the correct packing cross-section being used? Are the rings cut or formed to the correct length?
- T: Temperature. Check the system temperature against the packing manufacturer’s established temperature ratings for the product.
- A: Application. Some packings are made specifically for rotary equipment while others are intended for valves or static seals. Check to make sure the packing is suitable for the equipment where it is being used.
- M: Media. This refers to the fluid being sealed. Check with the manufacturer or with compatibility charts to be sure the seal material is compatible with the media. If the media is slurry, abrasion-resistant materials may need to be specified. If the media is toxic, explosive or required to be contained within certain maximum allowable leakage requirements, then a packing must also be selected on the basis of its ability to seal at low leakage levels.
- P: Pressure. Check the system pressure against the packing manufacturer’s established pressure ratings for the product.
- S: Speed. Check the equipment speed against the packing manufacturer’s established surface speed ratings for the product. Surface speed is expressed in feet per minute or meters per second and not revolutions per minute.
Investigate the Crime Scene
When possible, observe the equipment while it is running. Can you see, hear, feel, smell or use a sensor to make observations? Smoke, vibration, grinding noises, the scent of burning fibers and system pressure fluctuations are only a few of the clues that can be noticed or measured while the equipment is up and running. Examine the condition of the equipment. Most packings are robust seals that can handle less than perfect equipment condition, but there are limits to the amount of degradation they can withstand. Valve stems and pump shafts or sleeves should be checked for scratches, corrosion pitting and general surface roughness. Rough surfaces can damage the sealing surface and result in excessive leakage and quick wear of the seal.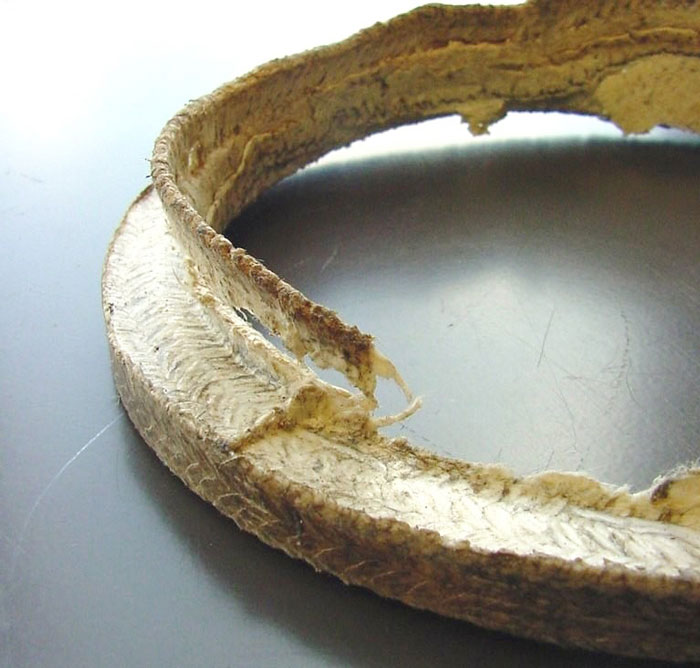
Perform Forensic Analysis
Contrary to the belief that “dead men tell no tales,” the examination of expired packing can tell a great deal about the cause of failure and the action that may need to be taken to correct the problem. Ideally, the whole packing set should be removed, and the pieces should be arranged in the same order they were taken out. The set can then be reconstructed outside of the stuffing box and examined for clues. If the entire set of packing cannot be retrieved, then pieces or photos of the remains may still prove helpful.Examine Common Causes of Failure
The lineup below gives some of the most common causes of packing failure. By looking at the failed packing, recognize some of the telltale signs that are left by these common modes of failure. Once they are detected, action can be taken to make sure their threat is reduced or eliminated.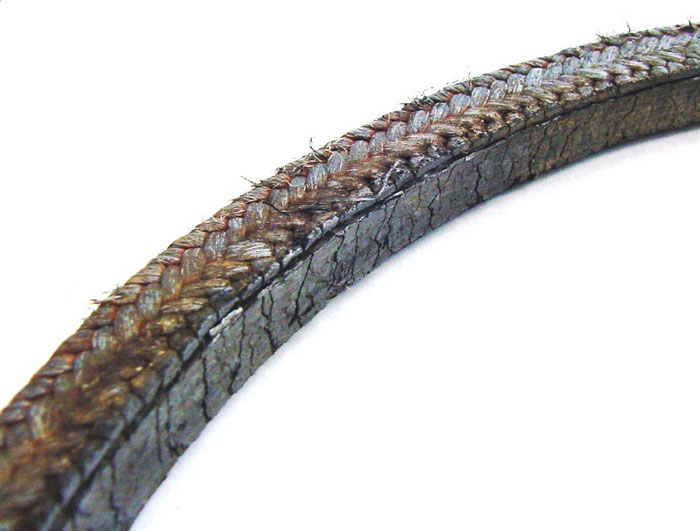
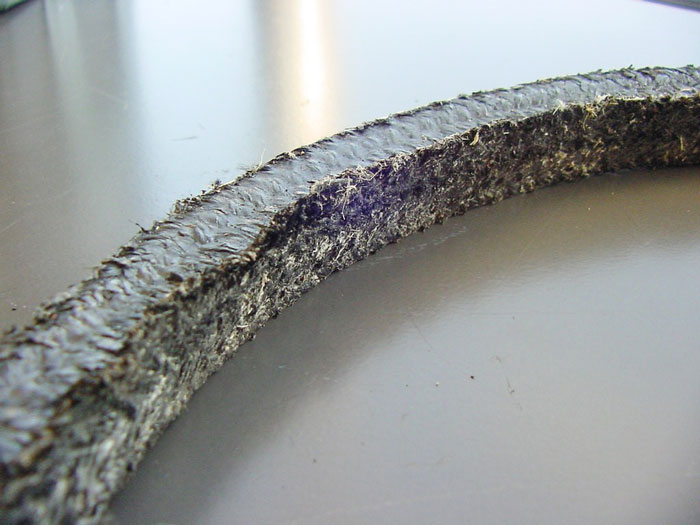
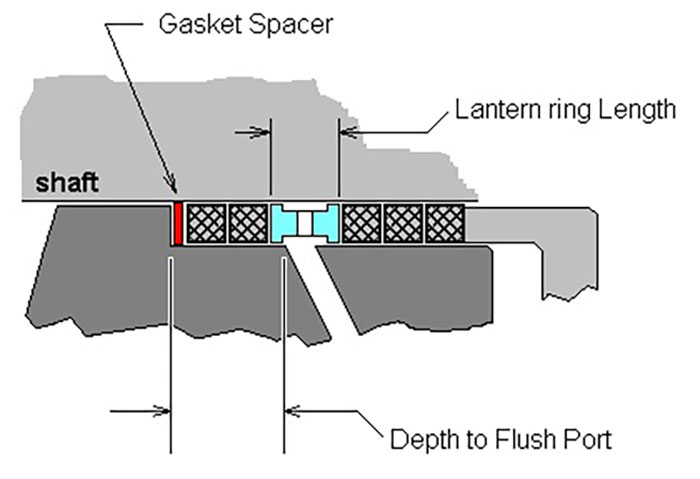