Analytics software that works with existing wastewater equipment.
Aquasight
10/15/2018
The heartbeat of U.S. water and wastewater infrastructure is the millions of pump systems that move water through networks of underground pipes to the points of use. Pumps are the critical operational equipment in this delivery, and their health and efficiency are important to all utility personnel including management, operations and maintenance. Limited resources and a lack of technological solutions have hindered the ability of many utilities to manage pump systems. But this is changing in ways that will yield great benefits for utilities as well as the wider economy and environment.
Pump Health & Efficiency Management
Pump health management is a must. Pump failures can lead to the discharge of raw sewage into waterways, flood neighborhood streets and homes, negatively impact fire protection services, and cause main breaks and loss of water pressure to residents. Such failures have occurred in communities around the country—like the one in New Orleans, Louisiana—and have cost tens of millions of dollars to recover from or repair. Improving pump efficiency also makes sense from a business perspective. U.S. water utilities spend $5 billion annually on energy. A full 70 percent of energy costs are related to pumps and blowers, many of which operate at poor efficiency. In addition, 80 percent of pumps have maintenance deferred, leading to higher energy costs. Running pump systems efficiently reduces operating costs and minimizes their carbon footprint while extending the equipment life.Technology Breakthrough
How can utilities better manage pump system health and efficiency? Many utilities have hundreds of pump systems, with many designed generations ago. Fifty-year-old systems are not uncommon. Skeleton staffs, shoestring budgets and limited monitoring capabilities are also challenges. To overcome these challenges, utilities need a low-cost technology that can serve as a reliable 24/7 digital employee. The good news is that with the advent of the Internet of Things (IoT) and artificial intelligence (AI), such platforms exist. The most significant breakthrough in the marketplace is in cost, effectively applying the IoT to existing pump systems, new or old, without capital outlay or additional hardware. Most utilities have telemetry in place that is underleveraged because it is mainly used for process control and not for pump system health and efficiency management. By intelligently mining real-time data, the technology platform can provide capabilities for utilities that they currently do not possess.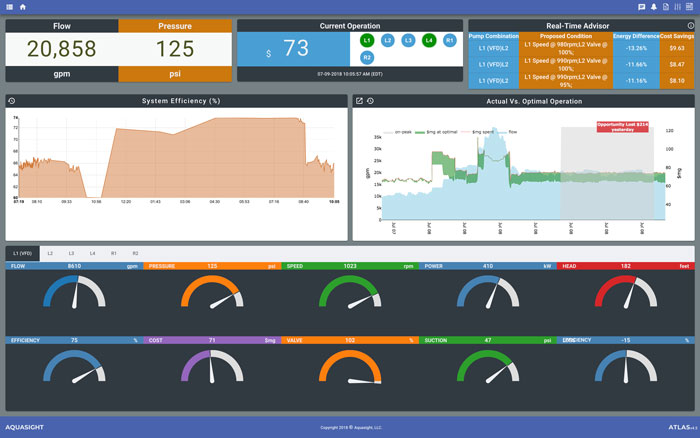
Case Study
A water booster station pumps between seven and 50 million gallons per day (mgd) of drinking water with an average discharge pressure of 120 pounds per square inch (psi). The station has six pumps, each rated at 18 mgd generating between 190 to 350 total dynamic head (TDH). One pump operates on a variable frequency drive (VFD), and the rest are throttle controlled. A real-time AI platform was deployed to manage the health and efficiency of the station. The platform featured a dashboard with a built-in AI advisor that displayed pump station performance and issued real-time advice on the most efficient operation based on live, on-the-ground conditions, equipment performance and availability (see Image 1). Based on the real-time advice, the operator saw an annual energy savings of 15.4 percent. The best part is that implementation required no capital investment. While the facility described above was automated, the technology platform functions regardless of automated or manual system control. In addition, the platform has built-in motor and digital pump health check capability (see Image 2). It visually displays where a pump is operating on its pump curve and creates a new curve that may be different than the original factory curve. This was found to be very useful to trigger maintenance that is based on real-time asset intelligence rather than a fixed preventive maintenance schedule. At this station, three out of six pumps were operating off their curve either due to degradation or system design, resulting in an additional $72,000 per year of operating costs.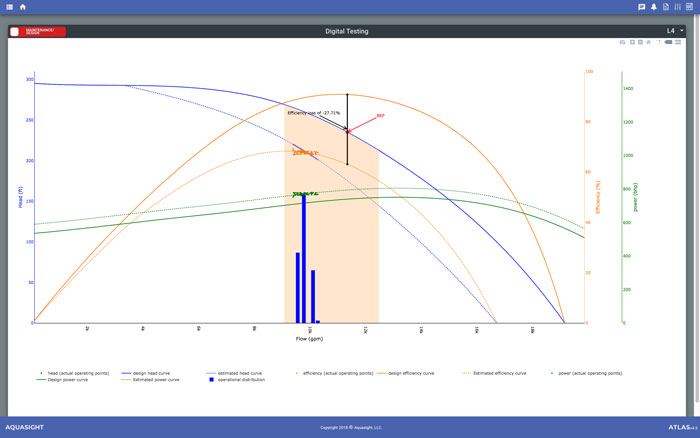