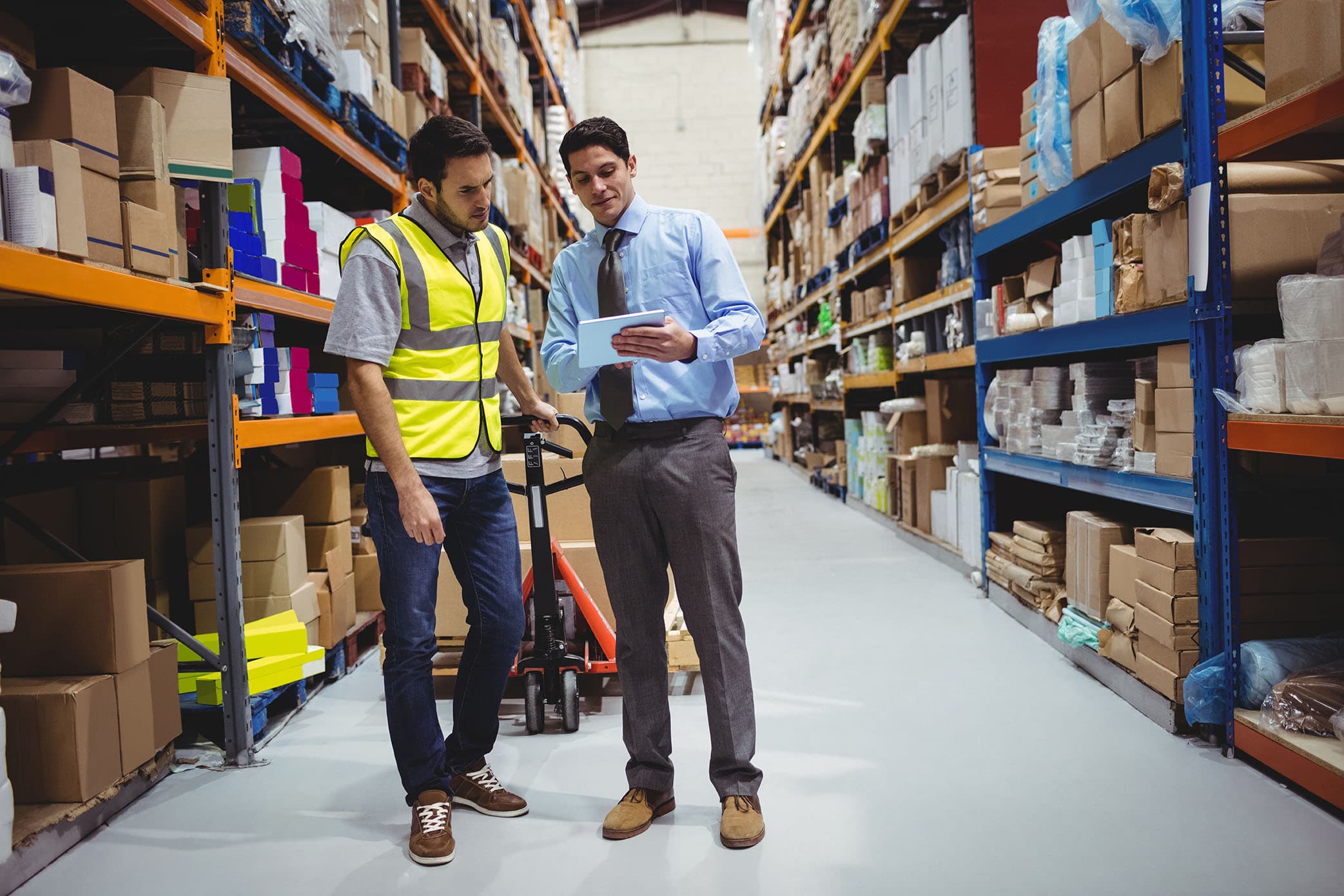
It’s no surprise that the coronavirus is impacting manufacturing, with production site shutdowns and travel and meeting restrictions. In fact, earlier this year, IHS Markit estimated that manufacturing was the third most impacted industry, behind wholesale and services.
This has hit manufacturers in various ways. Some companies, even those whose primary products or components are manufactured in the hardest hit regions, have seen little or no impact to their ability to meet customer demand.
On the other end of the spectrum, some companies or industries simply cannot get products or components, and many have already announced they will not meet customer or financial goals. Still others have actually explored new business opportunities because they are able to fill the gap and meet demand for production outside of hard-hit areas.
Even when all the production sites have come back up, we can expect supply chain disruptions as backlogs slowly clear.
Supply Chain Continuity
No matter how companies are affected, one thing is obvious: Nearly everyone is looking at the continuity of their own business, their supply chains, and their ability to meet customer demand now. They’re looking both at securing their own supply and making sure they fit into their customers’ supply chains going forward.
This focus on supply chain continuity makes sense for both the current situation and to better prepare for future supply chain disruption.
Manufacturers always have the risk that their supply chains will suddenly stop production, especially if they rely on one supplier or location. If they’re carrying low inventories, even a short shutdown can have a significant impact on their ability to do business.
On the other hand, if businesses are prepared and can fill the gap as customer needs change daily, they should be in a better position to continue operating and creating value when unexpected shutdowns occur.
Part of the Solution
So, what are some things manufacturers can do to secure their supply chains and the ability to operate during this crisis—and even help others with supply chain issues?
- Secure your ability to operate and communicate that to customers. As a manufacturer, you must first secure your own supply chain and then make sure customers understand how you fit into theirs. Check where your raw materials are coming from (and where your suppliers’ raw materials are coming from) and consider ahead of time how you would produce if your production was directly or indirectly impacted by the outbreak. Also recognize that customers are worried about it, and they may be out shopping for alternatives not knowing that you are able to supply. Many manufactures are being asked by their customers daily whether they are impacted by recent shutdowns. For every customer asking about a manufacturer’s ability to supply, there are likely others concerned but not asking…and that’s dangerous, because they may assume the worst and then go elsewhere without consulting you. Be proactive to let them know whether or not your ability to produce is impacted—and if there is an impact, work with them on contingency plans and timing.
- Plan how you will operate during and after a shutdown. With restrictions on gathering and workers calling in sick, are your HR policies prepared for the crisis? Many companies can adopt liberal leave or work-from-home policies, but manufacturing does not always have that option. If you need to retain people on production lines, how do you make sure they’re willing to stay home when needed—or stay with you afterward if they don’t get paid for time away from the site? The most prepared companies planned ahead and were ready with contingency procedures. They knew the plan and exactly what indicators, such as local school closings, would tell them when to adopt the new policies. Of course, how you operate for those on-site is critical as well. Ensure you have the right hygiene practices and consumables in place for workers. One company even went as far as to tape off manufacturing workstations to allow social distancing for their essential employees at the manufacturing site. So, make sure HR policies clearly define when people should and shouldn’t come to work, how to reduce the spread and work, and what happens during and after a shutdown.
- Help others through the crisis. Now that you can supply, it’s possible that your customers or prospects can’t get products from elsewhere or are struggling with their own production teams. Can you help them through the crisis and perhaps turn that into an opportunity and a competitive advantage that lasts long after the crisis has passed? Consider these examples:
a. Some U.S. companies were in a bind because their plastic parts providers temporarily shut down. They couldn’t go to other injection molders because they didn’t have extra tooling on hand. So, customers called Forecast 3D, an additive manufacturing company with production scale 3D printing capabilities, to see if they could supply the parts instead. In normal situations, additive manufacturing might not be the right way for these customers to get their parts. However, it requires no tooling and can often turn around parts in as little as a day. For a customer who just needs enough volume to get through the crisis, this can effectively bridge the gap. Of course, the situation changes daily, and it’s critical to be able to flex as the customers’ needs change. Now, as the healthcare community struggles to get essentials such as masks, Forecast 3D is in a position to quickly manufacture mask components to help solve this issue.
b. Years ago, when the H5N1 virus was circulating, DuPont made cleaning and disinfection products for industrial and hospital use. The company re-packaged these products, along with instructions on good hygiene, to create office disinfection kits. Essentially, they re-packaged existing products into kits to make it easier for offices to keep their workspaces clean and reduce the chance of spreading the virus. Again, a simple change could be part of the solution.
The question for any business is whether you can and should be part of the solution. Can you help train people and re-package or re-direct your products so they’re easier to use in case of a disaster? Can you supply people who otherwise can’t get products because they’re not manufacturing, or an essential component is stuck somewhere? Could you reallocate your product to a business in need, like groceries or hospitals? Are you in a position to supply extra inventory to customers now in case they can’t get product in the future?
- Make sure you are prepared. This latest pandemic is a great opportunity to look at your company’s policies and practices. Use it as motivation to review your risk and adjust your risk mitigation plans, such as qualifying secondary suppliers for your approved vendor list. While no one wants to see this situation again, it’s a wake-up call to be prepared. Sudden major supply chain disruptions may be uncommon but can be catastrophic to your business, causing you to under-serve and lose customers you may never win back. Being prepared now can mean the difference between under-resourcing and losing customers or winning business for the future.