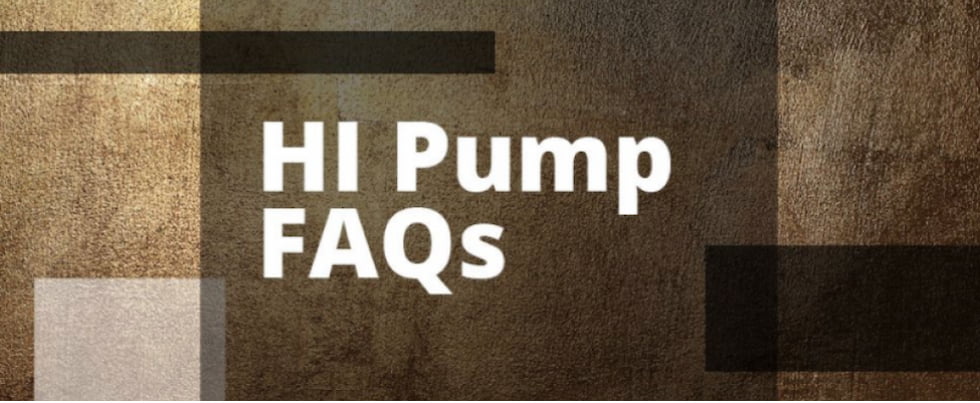
I’ve heard frequently cycling my pump’s motor can damage it. How can I mitigate this?
The amount of stress caused by line starting an alternating current (AC) induction motor has resulted in recommended limits for the number of starts per hour and the minimum amount of time between starts. National Electrical Manufacturers Association (NEMA) MG 10 provides a table for NEMA Design A and B motors from 1 horsepower (hp) through 250 hp.
This deals with 2-, 4- and 6-pole AC induction motors. Image 1 shows that 2-pole motors and large hp motors have the most stringent starting limitations.
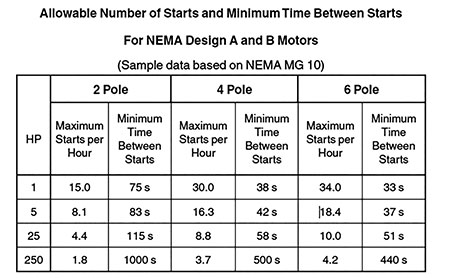
One option to mitigate harmful effects of cycling power is to use a reduced-voltage soft starter (RVSS). A solid-state RVSS reduces the voltage supplied to the motor during starting and reduces the current inrush.
This can reduce some of the stress on the motor. However, because the frequency of the alternating current from the RVSS will still be the same as the power line frequency, the slip of the motor will start at 100 percent. This will generate a large current surge in the motor’s rotor, although it will not be as large as if the motor was started at full power line voltage.
Also, the starting torque available to the motor is proportional to the starting current squared. If the motor is driving a pump with a high starting torque, it may be necessary for the soft starter to provide the motor with a high starting voltage and current to produce enough starting torque. This will increase the stress on the motor.
Finally, the high slip that accompanies the use of an RVSS starter generates additional heat in the motor until the motor reaches normal running speed. Therefore, it is important to ensure the motor produces enough torque during starting to quickly get the motor up to speed.
Variable frequency drives (VFDs) are another way to control the acceleration of the start and reduce the harmful effects of cycling power frequently to the motor. A VFD is different than an RVSS since the VFD controls both the voltage and the frequency of the AC power that is supplied to the motor, starting both at low value.
The low slip of the motor keeps the motor’s current draw low throughout the starting process. In addition, by maintaining normal motor slip, the VFD-driven motor can produce full rated torque throughout the motor’s speed range.
Another advantage of using a VFD is that sometimes the system can be designed and controlled so that it operates at lower speed, but for longer periods of time prior to cycling off. The need to cycle the pump is reduced in addition to the lower stress of the controlled acceleration.