More than 5 million wells worldwide employ artificial lift systems. In North America, it is estimated that 90 percent of wells use artificial lift processes. Typically the technologies applied are pumped wells with rod or beam pumps and electrical submersible pumps (ESPs), or hydraulic and gas lift systems. It is often necessary to install artificial lift systems in early production depending on the producing formation and expected reduction of the natural reservoir pressure. In unconventional production, including shale and tight formations, artificial lift is needed at the start of production to compensate for rapid decrease of the flowing pressure. The wellbore architecture is also complicated with deeper wells, deviated and long horizontal legs and multi-well entries.
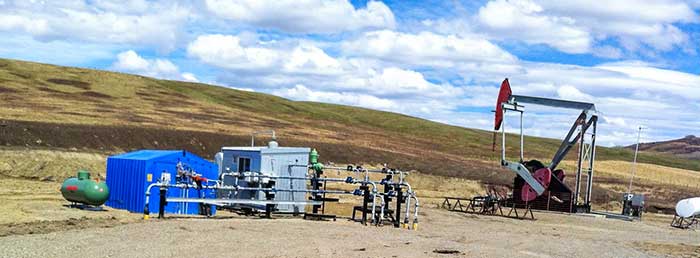
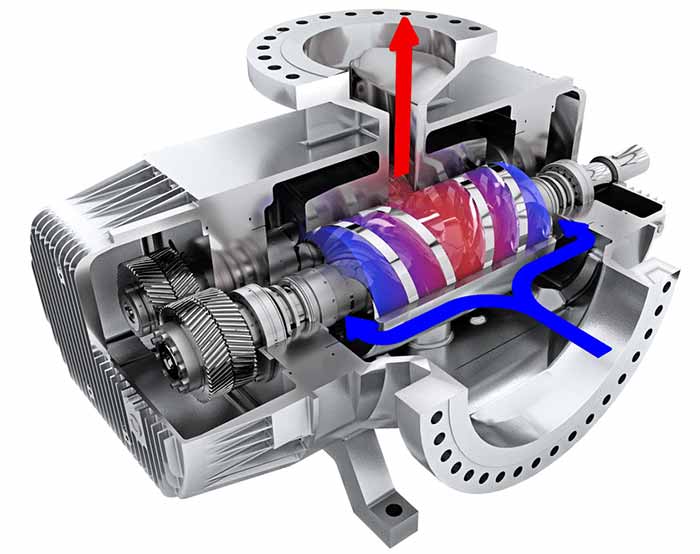
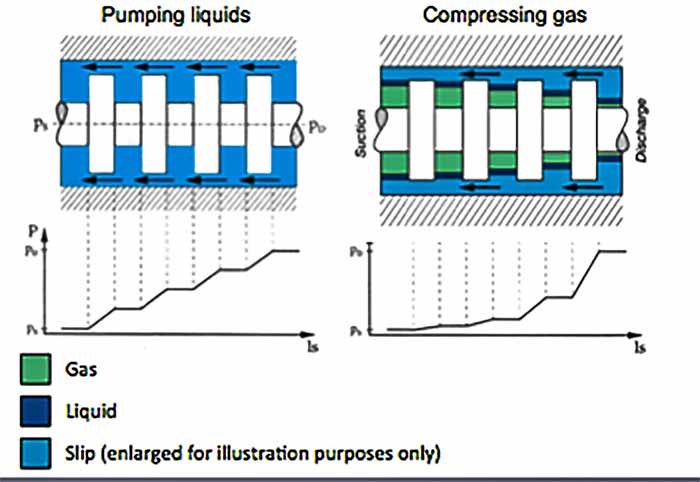
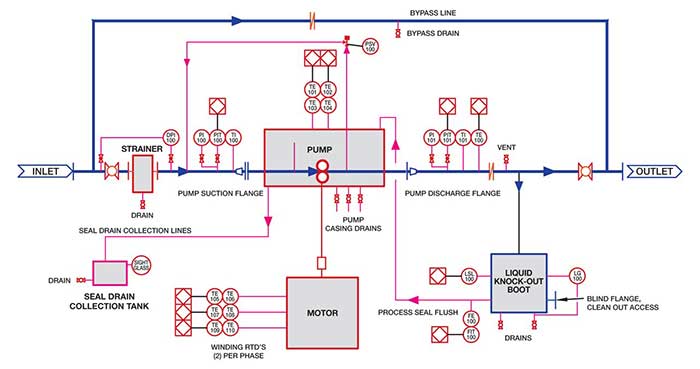