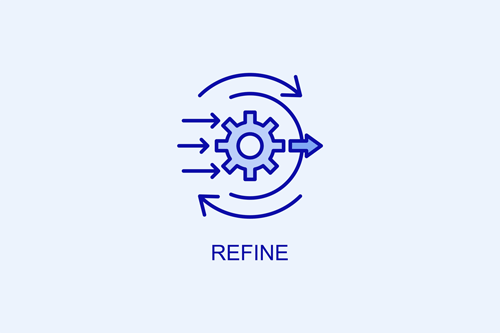
The reliable operation of pump systems depends heavily on effective sealing solutions, which maintain efficiency, safety and longevity. While mechanical seals have been widely adopted for their advanced leak-prevention capabilities, compression packing continues to play a vital role in demanding applications involving aggressive media and slurries. Understanding the critical role of packing in these pump applications and how to optimize its performance reveals its unique advantages for ensuring reliability in demanding industrial environments.
The Significance of Packing in Pumps
Packing is essential for sealing the shaft in a pump, mitigating leaks and maintaining system efficiency. Unlike mechanical seals, packing is not designed to form a hermetic seal. Instead, it operates as a sealing device for controlling fluid loss to provide lubrication, dissipate heat and reduce friction of the moving components. Depending on the application, lubrication can either be self-supplied by the media or injected through a lantern ring system.
Experts highlight that packing is a versatile solution, adaptable to various media and applications. The choice of packing material—be it graphite, polytetrafluoroethylene (PTFE) or aramid fibers—depends on the application’s specific requirements, including temperature, pressure and the chemical nature of the media.
Packing Lubrucation Explained
Depending on the application and the selected packing material, the configuration can either be self-lubricated, or lubrication
can be added through a lantern ring system.
• Self-lubricating systems: The built-in lubrication in the packing coupled with the pumped media provides the necessary lubrication in these systems. Specific packing materials, such as graphite-based options, include self-lubricating properties and
are, therefore, designed to perform effectively under
such conditions.
• Forced lubrication/positive fluid pressure: External lubrication is introduced via a lantern ring for media that cannot provide adequate lubrication or are chemically aggressive. This system ensures proper lubricant distribution, prevents excessive wear and maintains seal integrity.
Select Optimal Packing
Many important factors must be considered when selecting compression packing for a pump service. The first factor to consider is the aggressive nature of the slurry and how the media’s properties may change during the service life.
Packing issues typically arise when the media starts to work its way into the packing box. Abrasives migrate and deposit across the face of the packing rings. This creates more friction, increasing the overall temperature in the system and making the packing hard and brittle. In short, the packing loses some of its sealing capability.
Therefore, to ensure long-term reliable operations in various services, the standard practice in abrasive slurry applications is to select packing materials that address the needs of each specific application.
Selecting the right packing material is vital to ensure optimal performance and compatibility with the application. Packing materials are categorized based on their suitability for specific conditions:
High-temperature applications: Graphite-based packings excel in high-temperature environments, providing excellent heat dissipation and longevity.
Abrasive services: Materials like aramid or phenolic fibers offer mechanical resistance, making them ideal for handling slurry or other abrasive media.
Chemical resistance: PTFE-based packings are highly resistant to chemical attack, ensuring durability in aggressive environments.
In some cases, a combination of materials is used to optimize performance. For instance, abrasive services may benefit from a combination of phenolic fiber for mechanical strength and graphite for heat dissipation.
While these approaches offer superior performance, they can be more challenging to install, requiring expertise and care.
Understand Key Considerations for Packing Installation
Proper installation and maintenance of packing is paramount for its effectiveness and longevity. The following are recommended practices:
Shaft alignment
Misaligned shafts are a common cause of packing failure. Poor alignment can lead to uneven wear, overheating and even destruction of the packing material. It may also cause packing rings to burn or deform, leading to system failure. Addressing alignment requires a holistic approach. It begins with regular maintenance of the equipment, including checking the condition of the shaft and the stuffing box. Proper installation techniques also play a role in mitigating alignment issues. For instance, ensuring the shaft’s roughness and tolerance levels are within acceptable limits helps maintain seal integrity and reduces wear.
Lantern rings and lubrication
For applications requiring additional lubrication, lantern rings are often installed to inject water or oil. Correct placement of the lantern ring is essential to ensure the even distribution of lubricant. Failure to do so can result in inadequate lubrication, heat buildup and eventual packing degradation.
Surface condition and maintenance
Another critical factor is the condition of the stuffing box and shaft surface. Rough or uneven surfaces can cause premature wear and failure. Routine maintenance, including retightening and replacing worn packing rings, is essential to sustain performance.
Installation precision and load distribution
It is essential to ensure all rings are properly seated, with attention to the gland follower’s position. Adequate adjustment should be allowed to accommodate wear over time. Special attention should also be paid to load distribution across the packing rings. In slurry applications, uneven pressure can allow abrasive media to penetrate, causing premature failure.
Be Aware of Common Misconceptions About Packing
One widespread misconception is that all packing materials are interchangeable. This misunderstanding can lead to the use of inappropriate materials, resulting in reduced efficiency and increased downtime. For instance, using standard acrylic packing in a high-friction environment will likely result in rapid degradation.
Another misconception is that packing should eliminate all leakage. Slight leakage is normal to ensure proper lubrication and cooling. Attempting to achieve a completely leak-free seal can cause excessive friction and overheating.
Understanding common pump packing misconceptions provides the operator with the know-how and knowledge to use innovative solutions to optimize sealing efficiency and equipment longevity.
Look for Advanced Techniques & Innovative Solutions
Advancements in the industry have led to the development of composite packing solutions that combine multiple materials to address specific challenges effectively. For instance, hybrid packing that integrates a phenolic fiber base for mechanical strength with a graphite layer for heat dissipation can significantly enhance performance in demanding applications.
Other high-performance slurry pump packing materials include Novoloid, synthetic fibers, carbon fibers, PTFE/graphite fibers and moldable, putty-like materials. Leading manufacturers leverage a combination of fibers, lubricants and impregnations to accommodate various slurry applications. These packings can be paired with restructured PTFE rings and moldable materials to achieve a reliable seal, with or without flush water.
In some cases, an engineered design that combines multiple packing styles is the most effective. Upgrading to high-performance materials designed to withstand the rigorous demands of slurry applications can provide long-term cost savings by reducing downtime and improving operational efficiency.
Seals and packing are integral to pump systems’ reliability and efficiency. By understanding the nuances of packing selection, installation and maintenance, operators can optimize performance, reduce downtime and extend equipment life span.
Whether one is dealing with slurry applications, aggressive chemicals or high temperatures, tailored packing solutions ensure pumps operate smoothly, contributing to overall system success. With ongoing innovations in packing materials and techniques, the future promises even more advancements in sealing solutions for pump applications.